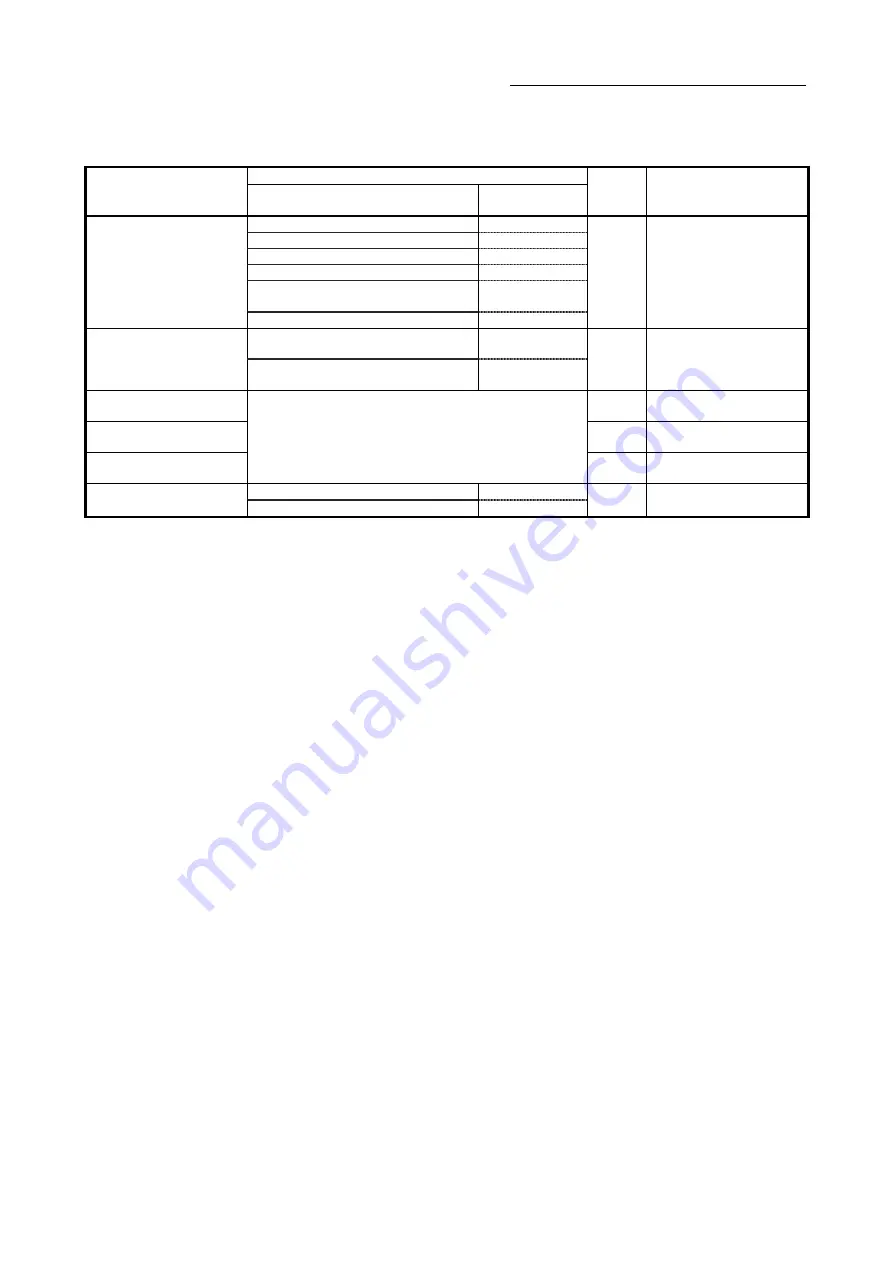
5 - 50
Chapter 5 Data Used for Positioning Control
5.2.5 HPR basic parameters
Item
Setting value, setting range
Default
value
Buffer memory address
Value set with GX Works2
Value set with
sequence program
[Pr.43]
HPR method
0 : Proximity dog method [RJ010 mode]
0
0 70+150n
4 : Count method 1) [RJ010 mode]
4
5 : Count method 2) [RJ010 mode]
5
6 : Data set method [RJ010 mode]
6
7 : Scale origin signal detection method
[RJ010 mode]
7
8: Driver HPR method [CiA402 mode]
8
[Pr.44]
HPR direction
0 : Positive direction (address increment
direction)
0
0 71+150n
1 : Negative direction (address decrement
direction)
1
[Pr.45]
HP address
The setting value range differs depending on the "[Pr.1] Unit
setting".
0
72+150n
73+150n
[Pr.46]
HPR speed
1
74+150n
75+150n
[Pr.47]
Creep speed [RJ010 mode]
1
76+150n
77+150n
[Pr.48]
HPR retry [RJ010 mode]
0 : Do not retry HPR with limit switch
0
0 78+150n
1 : Retry HPR with limit switch
1
n: Axis No.-1
[Pr.43] HPR method
Set the "HPR method" for carrying out machine HPR.
0: Proximity dog method [RJ010 mode]
...... After decelerating at the proximity dog ON, stop at the zero signal and
complete the machine HPR.
4: Count method 1) [RJ010 mode]
...... After decelerating at the proximity dog ON, move the designated distance,
and complete the machine HPR with the zero signal.
5: Count method 2) [RJ010 mode]
...... After decelerating at the proximity dog ON, move the designated distance,
and complete the machine HPR.
6: Data set method [RJ010 mode]
...... The position where the machine HPR has been made will be the HP.
7: Scale origin signal detection method [RJ010 mode]
...... After deceleration stop at the proximity dog ON, move to the opposite
direction against the HPR direction, and move to the HPR direction after
deceleration stop once at the detection of the first zero signal. Then, it
stops at the detected nearest zero signal, and completes the machine
HPR.
8: Driver HPR method [CiA402 mode]
...... Carry out the HPR operation on the driver side. The HPR operation and
parameters depend on the specifications of the driver.
Refer to Section 8.2.8 "Driver HPR method" for details.
When HPR method that cannot be executed is set, the error "HPR method invalid"
(error code: 232) occurs and the HPR is not executed.
Note) Refer to Section 8.2 "Machine HPR" for details on the HPR methods.
Summary of Contents for MELSEC Q Series
Page 2: ......
Page 30: ...A 28 MEMO ...
Page 32: ...MEMO ...
Page 97: ...3 29 Chapter 3 Specifications and Functions MEMO ...
Page 102: ...3 34 Chapter 3 Specifications and Functions MEMO ...
Page 282: ...5 162 Chapter 5 Data Used for Positioning Control MEMO ...
Page 374: ...7 16 Chapter 7 Memory Configuration and Data Process MEMO ...
Page 376: ...MEMO ...
Page 400: ...8 24 Chapter 8 HPR Control MEMO ...
Page 425: ...9 25 Chapter 9 Major Positioning Control MEMO ...
Page 528: ...9 128 Chapter 9 Major Positioning Control MEMO ...
Page 554: ...10 26 Chapter 10 High Level Positioning Control MEMO ...
Page 586: ...11 32 Chapter 11 Manual Control MEMO ...
Page 800: ...16 54 Chapter 16 Troubleshooting MEMO ...
Page 830: ...Appendix 30 Appendices MEMO ...
Page 833: ......