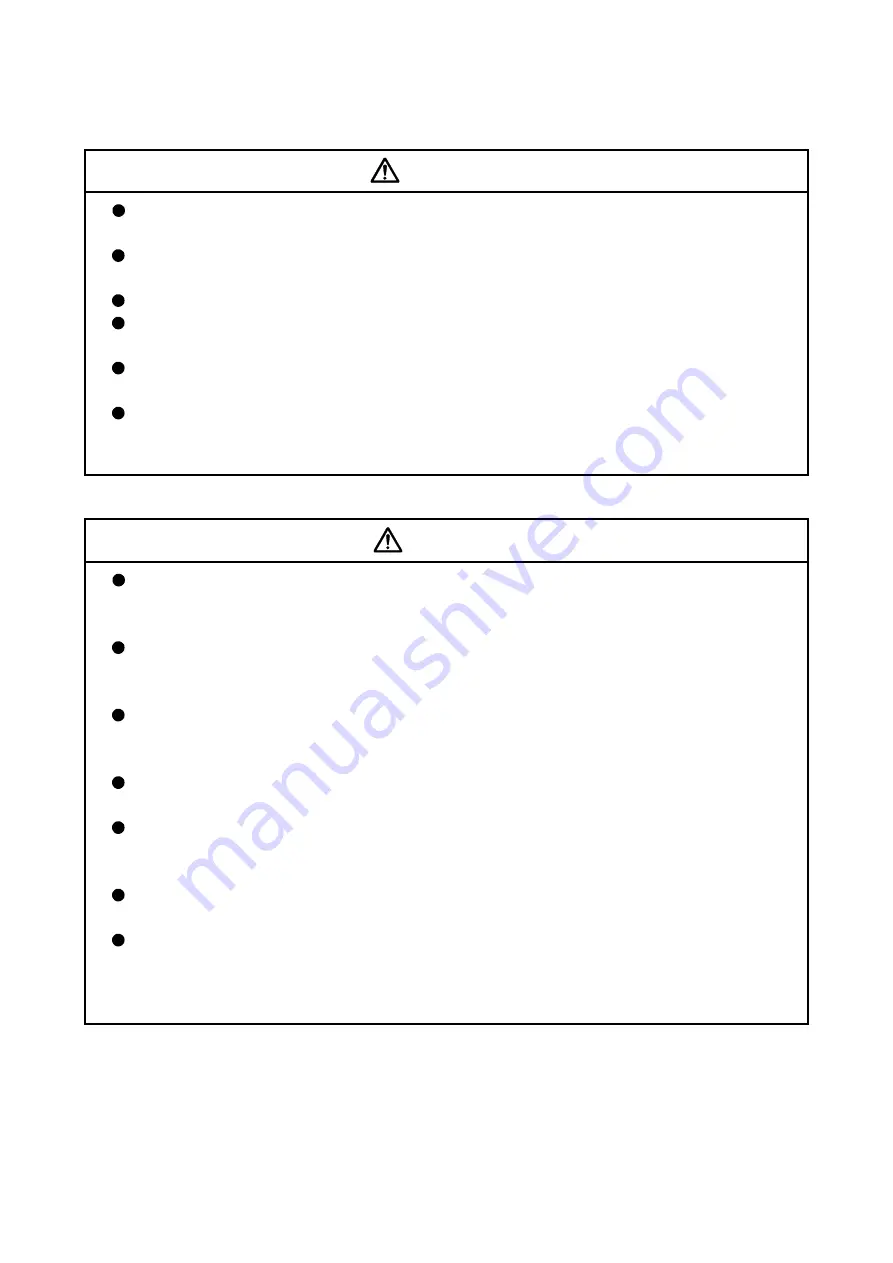
A - 4
CAUTION
The system must have a mechanical allowance so that the machine itself can stop even if the
stroke limits switch is passed through at the max. speed.
Use wires and cables that have a wire diameter, heat resistance and bending resistance
compatible with the system.
Use wires and cables within the length of the range described in the instruction manual.
The ratings and characteristics of the parts (other than module, servo amplifier and servomotor)
used in a system must be compatible with the module, servo amplifier and servomotor.
Install a cover on the shaft so that the rotary parts of the servomotor are not touched during
operation.
There may be some cases where holding by the electromagnetic brake is not possible due to the
life or mechanical structure (when the ball screw and servomotor are connected with a timing belt,
etc.). Install a stopping device to ensure safety on the machine side.
(2) Parameter settings and programming
DANGER
Set the parameter values to those that are compatible with the module, servo amplifier,
servomotor and regenerative resistor model and the system application. The protective functions
may not function if the settings are incorrect.
The regenerative resistor model and capacity parameters must be set to values that conform to
the operation mode and servo amplifier. The protective functions may not function if the settings
are incorrect.
Set the mechanical brake output and dynamic brake output validity parameters to values that are
compatible with the system application. The protective functions may not function if the settings
are incorrect.
Set the stroke limit input validity parameter to a value that is compatible with the system
application. The protective functions may not function if the setting is incorrect.
Set the servomotor encoder type (increment, absolute position type, etc.) parameter to a value
that is compatible with the system application. The protective functions may not function if the
setting is incorrect.
Use the program commands for the program with the conditions specified in the instruction
manual.
Set the sequence function program capacity setting, device capacity, latch validity range, I/O
assignment setting, and validity of continuous operation during error detection to values that are
compatible with the system application. The protective functions may not function if the settings
are incorrect.
Summary of Contents for MELSEC Q Series
Page 2: ......
Page 30: ...A 28 MEMO ...
Page 32: ...MEMO ...
Page 97: ...3 29 Chapter 3 Specifications and Functions MEMO ...
Page 102: ...3 34 Chapter 3 Specifications and Functions MEMO ...
Page 282: ...5 162 Chapter 5 Data Used for Positioning Control MEMO ...
Page 374: ...7 16 Chapter 7 Memory Configuration and Data Process MEMO ...
Page 376: ...MEMO ...
Page 400: ...8 24 Chapter 8 HPR Control MEMO ...
Page 425: ...9 25 Chapter 9 Major Positioning Control MEMO ...
Page 528: ...9 128 Chapter 9 Major Positioning Control MEMO ...
Page 554: ...10 26 Chapter 10 High Level Positioning Control MEMO ...
Page 586: ...11 32 Chapter 11 Manual Control MEMO ...
Page 800: ...16 54 Chapter 16 Troubleshooting MEMO ...
Page 830: ...Appendix 30 Appendices MEMO ...
Page 833: ......