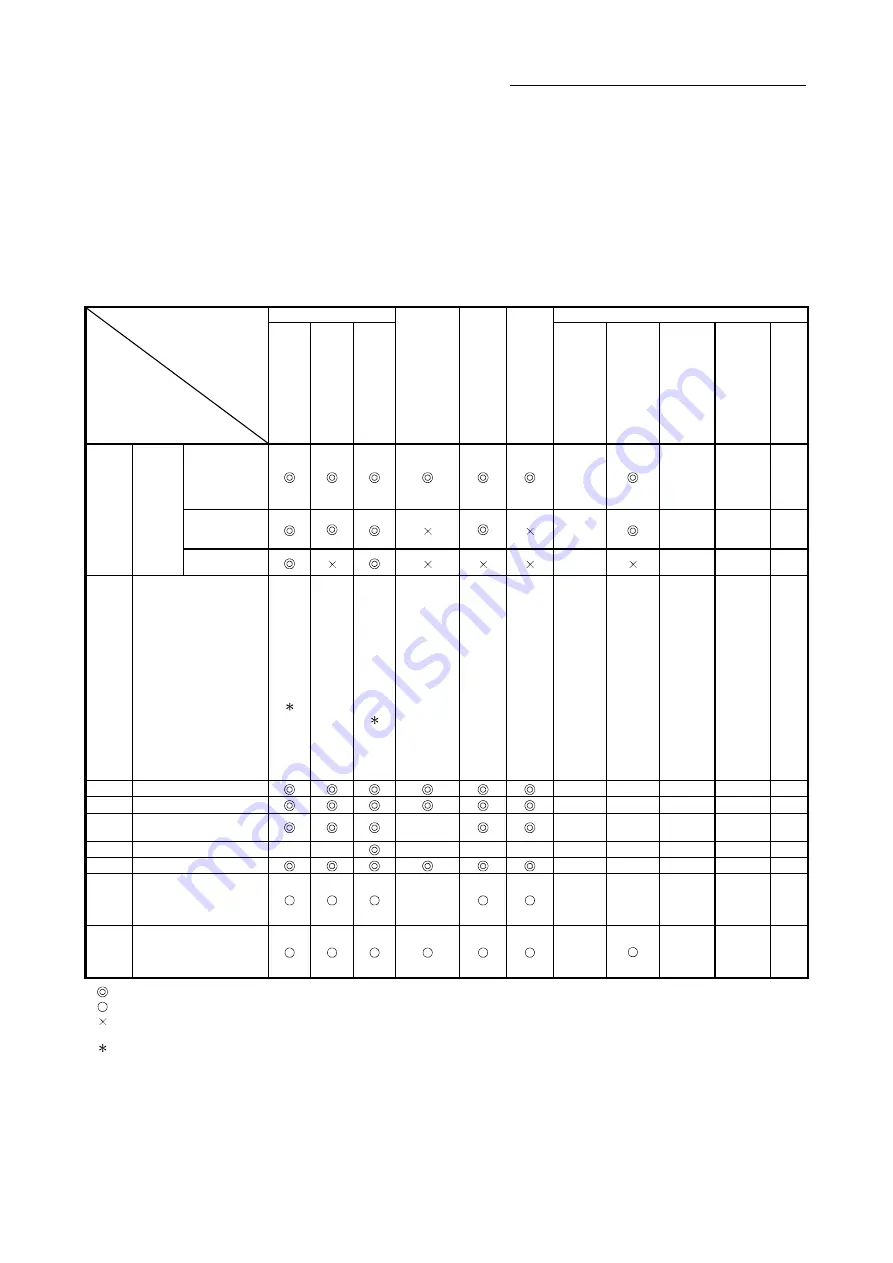
5 - 9
Chapter 5 Data Used for Positioning Control
5.1.6 Setting items for positioning data
Positioning data must be set for carrying out any "major positioning control". The table
below lists the items to be set for producing the positioning data.
One to 600 positioning data items can be set for each axis.
For details of the major positioning controls, refer to Chapter 9 "Major Positioning
Control". For details of the individual setting items, refer to Section 5.3 "List of
positioning data".
Major positioning control
Positioning data
Position control
1
to
4 axi
s
sp
ee
d co
nt
ro
l
S
peed
-p
os
iti
on
sw
itch
in
g
co
nt
ro
l
P
os
iti
on
-s
pee
d s
w
itch
in
g
co
nt
ro
l
Other control
1-
axi
s l
ine
ar
c
ont
rol
2/
3/
4-
axi
s l
ine
ar
in
te
rp
ol
at
io
n co
nt
ro
l
1-
axi
s fi
xe
d-
fe
ed
co
nt
rol
2/
3/
4-
axi
s fi
xe
d-
fe
ed
co
nt
ro
l
2-
axi
s ci
rc
ul
ar
in
te
rp
ol
at
io
n co
nt
ro
l
N
O
P
in
st
ru
ct
ion
C
urre
nt
va
lu
e ch
ang
ing
JUM
P
in
st
ru
cti
on
LO
OP
LE
N
D
[Da.1]
Operation
pattern
Independent
positioning
control
(Positioning
complete)
–
– –
–
Continuous
positioning
control
–
– –
–
Continuous path
control
–
– –
–
[Da.2] Control method
Linear 1
Linear 2
Linear 3
Linear 4
Fixed-
feed 1
Fixed-
feed 2
Fixed-
feed 3
Fixed-
feed 4
Circular
sub
Circular
right
Circular
left
Forward
run speed 1
Reverse run
speed 1
Forward
run speed 2
Reverse run
speed 2
Forward
run speed 3
Reverse run
speed 3
Forward
run speed 4
Reverse run
speed 4
Forward
run
speed/
position
Reverse
run
speed/
position
Forward
run
position/
speed
Reverse
run
position/
speed
NOP
Current
value
changing
JUMP
instruction
LOOP LEND
[Da.3] Acceleration time No.
– – – –
–
[Da.4] Deceleration time No.
– – – –
–
[Da.6]
Positioning address/
movement amount
–
–
New
address
– –
–
[Da.7] Arc address
– –
– –
– – – – –
–
[Da.8] Command speed
–
– – –
–
[Da.9]
Dwell time/JUMP destination
positioning data No.
–
–
–
JUMP
destination
positioning
data No.
– –
[Da.10]
M code/Condition data No./
Number of LOOP to LEND
repetitions
–
JUMP
condition
data No.
Number of
LOOP to
LEND
repetitions
–
: Always set
: Set as required ("–" when not required)
: Setting not possible (If set, the error "Continuous path control not possible" (error code: 516) will occur at start.)
– : Setting not required (If the value is the default value or within the setting range, there is no problem.)
: Two control systems are available: the absolute (ABS) system and incremental (INC) system.
Summary of Contents for MELSEC Q Series
Page 2: ......
Page 30: ...A 28 MEMO ...
Page 32: ...MEMO ...
Page 97: ...3 29 Chapter 3 Specifications and Functions MEMO ...
Page 102: ...3 34 Chapter 3 Specifications and Functions MEMO ...
Page 282: ...5 162 Chapter 5 Data Used for Positioning Control MEMO ...
Page 374: ...7 16 Chapter 7 Memory Configuration and Data Process MEMO ...
Page 376: ...MEMO ...
Page 400: ...8 24 Chapter 8 HPR Control MEMO ...
Page 425: ...9 25 Chapter 9 Major Positioning Control MEMO ...
Page 528: ...9 128 Chapter 9 Major Positioning Control MEMO ...
Page 554: ...10 26 Chapter 10 High Level Positioning Control MEMO ...
Page 586: ...11 32 Chapter 11 Manual Control MEMO ...
Page 800: ...16 54 Chapter 16 Troubleshooting MEMO ...
Page 830: ...Appendix 30 Appendices MEMO ...
Page 833: ......