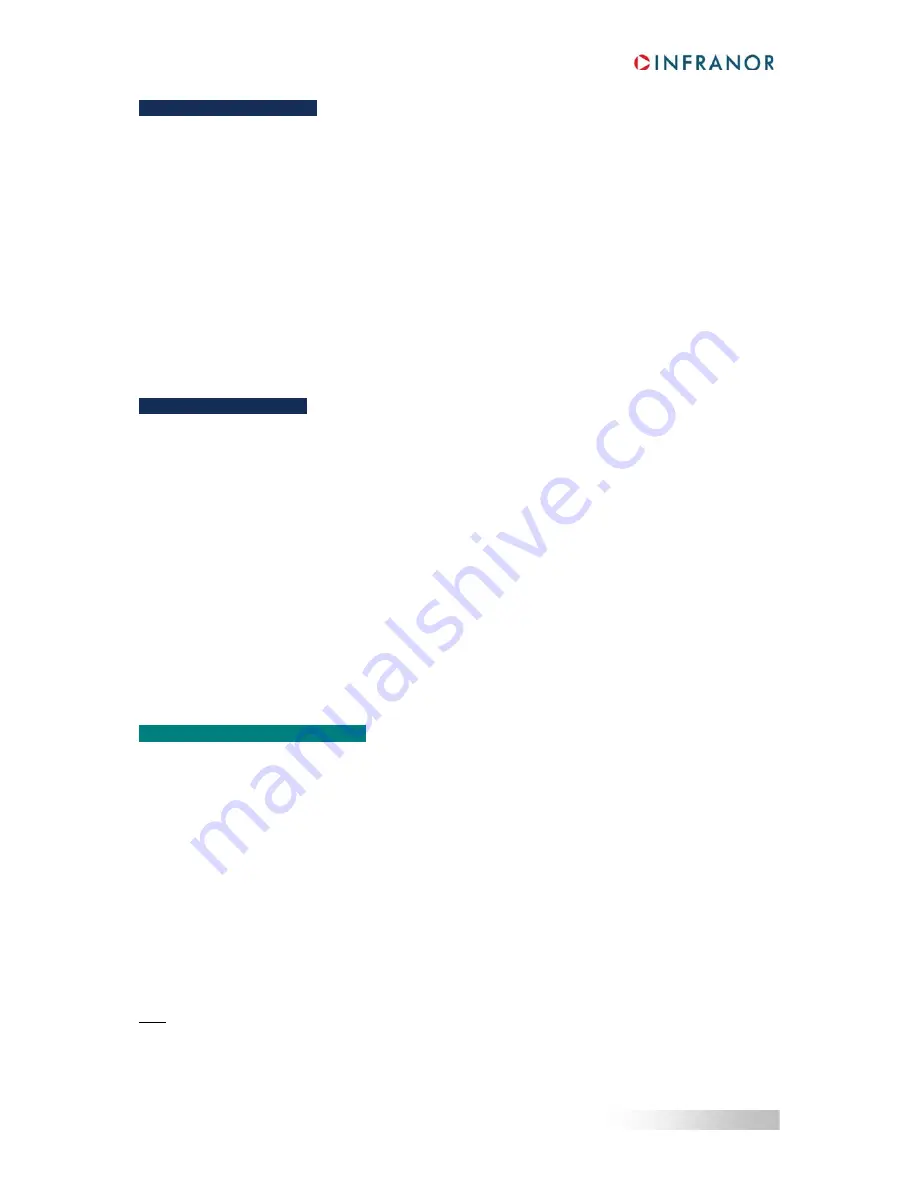
24
XtrapulsPac – User Guide
Chapter 2 - Commissioning
2.4.9
-
L
OGIC
I/O
S EXTENSION
The external CANopen I/Os module extension is supported by the XtrapulsPac-ak version of the servo drive. The
external I/Os module is connected to the CAN bus on the same network as the servo drive. When many servo
drives are connected on the CAN bus, a given I/Os module can only be assigned to one servo drive.
The basic setup of an external I/Os module is the following:
- adjust first the I/Os module baudrate equal to the servo drive baudrate,
- adjust also the address of the I/Os module on the CAN bus network,
- then select the address of the I/Os module in the servo drive configuration window,
- connect the servo drive to the I/Os module.
The default setting is the following:
- SDO communication between the servo drive and I/Os module,
- module inputs 1 to 5 are assigned to the virtual drive inputs IN6 to IN10,
- module outputs 1 to 3 are assigned to the virtual drive outputs OUT4 to OUT6.
2.4.10
-
B
RAKING
R
ESISTOR
When the drive is operating in standalone mode (AC main connection without GDPS), select the correct braking
resistor operation according to the drive configuration on the X9 connector. If the drive is operating with a GDPS
power supply (DC bus connection), the drive braking resistor parameters are not valid.
- When
the
Internal braking resistor
operation is selected the
Duty cycle limit
parameter value is limited
at 25 per thousand. This means a maximum braking transistor conduction of 25 ms over a period of 1
second. This selection allows protecting the drive internal 35W braking resistor against overheating and
failure.
- When
the
External braking resistor
operation is selected the
Duty cycle limit
parameter value is
limited at 70 per thousand. This means a maximum braking transistor conduction of 70 ms over a period
of 1 second.
The parameter
Braking resistor duty cycle limit
allows limiting the external braking resistor average power in
order to protect it against overheating and failure. The
Duty cycle limit
parameter value is calculated according
to the external braking resistor specifications as described below:
Duty cycle limit = Braking resistor rated power (W) x Braking resistor ohmic value (Ohms) / Braking on threshold
(V) / Braking on threshold (V).
2.5 - DRIVE PARAMETER SAVING
When all adjustments and settings have been tested, they can be stored in the non-volatile drive memory by
selecting the command
Drive parameter file
>
Store parameters to flash memory
. In this case, all drive
standard parameters are saved in the drive file
DRIVEPAR.TXT.
The drive file DRIVEPAR.TXT can then be transferred to the project directory in the PC by selecting the command
Drive parameter file
>
Backup parameters to PC file
.
The command
Drive parameter file
>
Restore parameters
allows transferring a file DRIVEPAR.TXT saved in
the PC directory to the drive.
A user parameter list can also be edited and saved in the file USER_PAR.TXT by using the command
User
parameter file
>
Edit Parameters
. The USER_PAR.TXT file can then be transferred to the drive by selecting the
command
User parameter file
>
Restore parameters
. A drive file USER_PAR.TXT can be transferred from the
drive to the PC directory by selecting the command
User parameter file
>
Backup parameters to PC file
. The
user parameter file USER_PAR.TXT can be used for saving drive parameters that are not saved in the file
DRIVEPAR.TXT (standard drive parameter list).
Note: The commands
Tools
>
Drive file backup
and
Tools
>
Drive file restoring
concern all project drive files:
DRIVEPAR.TXT, USER_PAR.TXT, SEQUENCE.TXT, and so on.