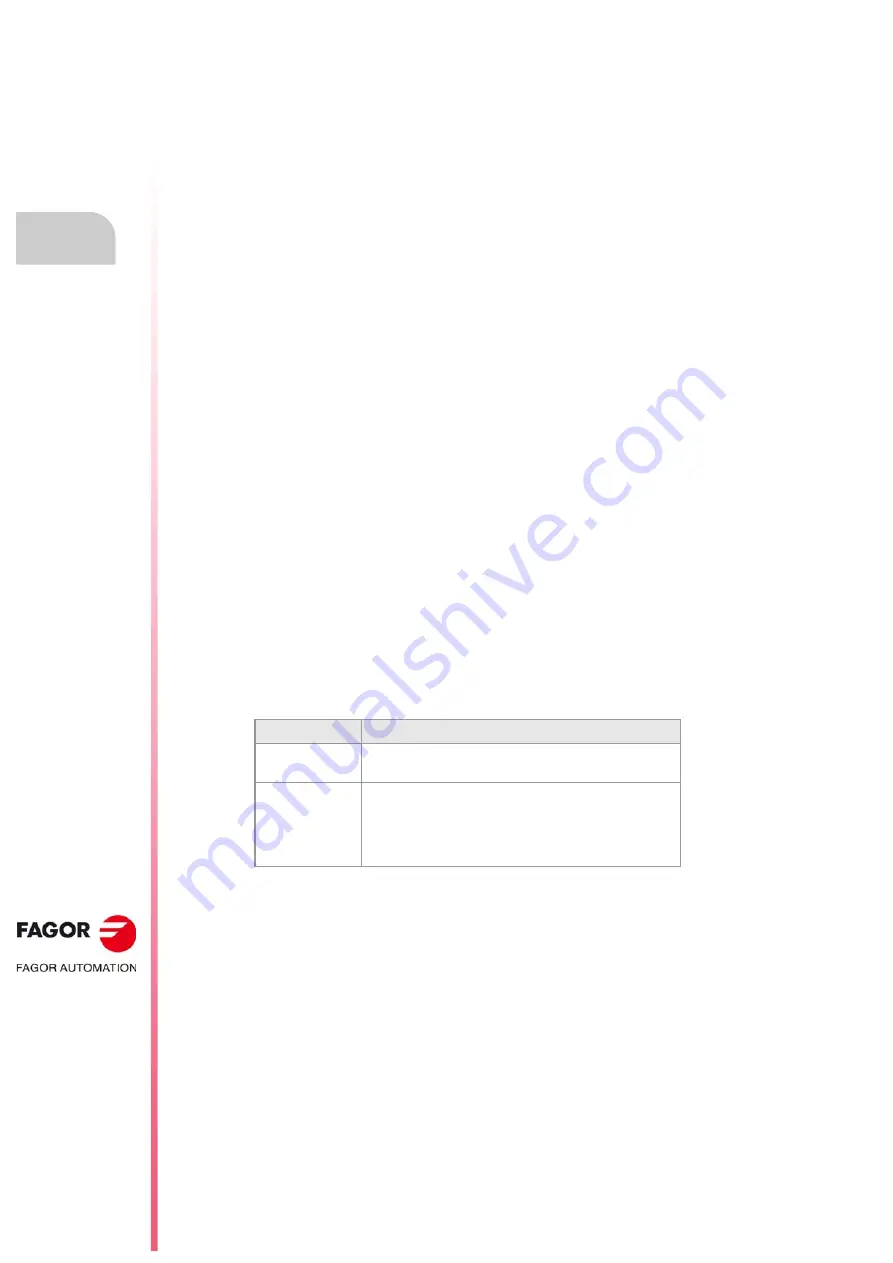
Installation manual.
CNC 8060
CNC 8065
2.
MACHINE PA
RAMETERS.
Gen
e
ral machin
e parameters.
·104·
(R
EF
: 1709)
2.3.26
Synchronized switching.
SWTOUTPUT
Local digital output associated with synchronized switching.
Possible values: From 0 to NLOCOUT (Number of local digital outputs).
Default value: 0.
Associated variable: (V.)MPG.SWTOUTPUT
Local digital output associated with synchronized switching. For synchronized switching,
only local outputs associated with pins LI/O1 (local output 1) and LI/O2 (local output 2) may
be used because they have been set for Laser applications. That requires setting parameter
NLOCOUT = 8.
Synchronized switching refers to the process to control a local digital output of the CNC
depending on the type of movement programmed on the axes. The selected digital output
is activated when switching from G0 to G1/G2/G3. The selected digital output is canceled
when switching from G1/G2/G3 to G0.
In order for this feature to work better, the parameters of the axes involved in the movements
must be set with the same values (gain, filters, acceleration and deceleration, feed forward,
etc.) and must also work with the least amount of following error (lag) as possible.
SWTDELAY
Delay of the device associated with synchronized switching.
Possible values: From 0 to 100 ms.
Default value: 0 ms.
Associated variable: (V.)MPG.SWTDELAY
This parameter sets the delay between digital output on/off and the device that is connected
to it.
SWTG0FEED
Observe the G00 feedrate during the synchronized switching.
Possible values: Yes / No.
Default value: Yes.
Associated variable: (V.)MPG.SWTG0FEED
The SWTG0FEED parameter determines the feedrate for the sections in G0.
The behavior can be modified from the part program with the instruction #SWTOUT. If
according to the parameter or the command (#SWTOUT) the G0s are executed as G1
(constant feedrate), G0 is displayed in the history.
SWTG0FEED
Meaning.
Yes
Movements in G0 are carried out at a rapid feedrate
(parameter G00FEED).
No
The cut is made at a constant feedrate (with the feedrate of
the previous G1/G2/G3), without accelerating in the
sections in G0. This option makes it possible to prevent
possible problems with machine frequency excitation, thus
producing better quality precision and surface cuts.
Summary of Contents for CNC 8060
Page 1: ...Ref 1709 8060 8065 CNC Installation manual...
Page 10: ...BLANK PAGE 10...
Page 14: ...BLANK PAGE 14...
Page 20: ...BLANK PAGE 20...
Page 32: ...BLANK PAGE 32...
Page 36: ...BLANK PAGE 36...
Page 38: ...BLANK PAGE 38...
Page 40: ...BLANK PAGE 40...
Page 41: ...PART 1 INSTALLATION MANUAL...
Page 42: ...BLANK PAGE 42...
Page 532: ...Installation manual CNC 8060 CNC 8065 9 CNC VARIABLES 532 REF 1709...
Page 533: ...PART 2 CONCEPTS...
Page 534: ...BLANK PAGE 534...
Page 548: ...Installation manual CNC 8060 CNC 8065 10 GENERAL SETUP Configuration examples 548 REF 1709...
Page 644: ...Installation manual CNC 8060 CNC 8065 14 SUBROUTINES Assistance for subroutines 644 REF 1709...
Page 668: ...Installation manual CNC 8060 CNC 8065 15 HARDWARE Configure the PT100 inputs 668 REF 1709...
Page 697: ...Installation manual CNC 8060 CNC 8065 697 User notes REF 1709...