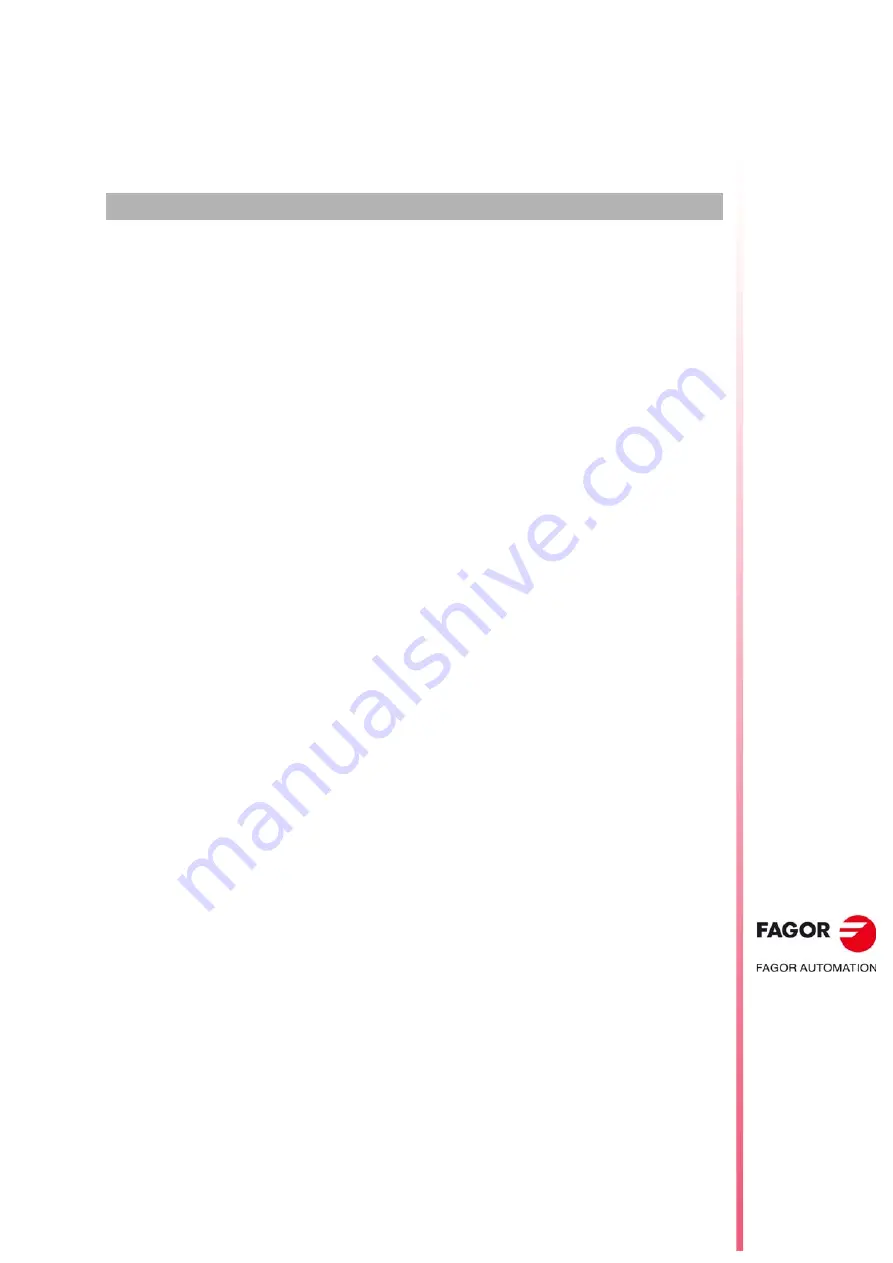
CNC 8060
CNC 8065
6
·389·
(R
EF
: 1709)
LOGIC CNC INPUTS AND OUTPUTS.
CNC's physical inputs and outputs are the set of system inputs and outputs that are governed
by the PLC and communicate with the outside world through CNC connectors.
The CNC also has a number of logic inputs and outputs to exchange the internal data with
the marks and registers of the PLC. This way, the PLC has access to some internal CNC
data. Each of these logic inputs and outputs may be referred to using its associated
mnemonic. The mnemonics that begin with a "_" sign indicate that the signal is active low
(0 V).
CNCREADY
_ALARM
AUXEND
_EMERGEN
MANUAL
_STOP
The CNC's logic outputs or PLC consulting signals are grouped into:
• General consulting signals.
• Axis consulting signals.
• Spindle consulting signals.
• Consultation signals of the independent interpolator.
• Tool manager consulting signals.
• Keystroke consulting signals.
The CNC's logic inputs or signals that may be modified via PLC are grouped into:
• General modifiable signals.
• Axis modifiable signals.
• Spindle modifiable signals.
• Modifiable signals of the independent interpolator.
• Tool manager modifiable signals.
• Keystroke modifiable signals.
Abbreviations used in this chapter.
(=0)
Low logic level.
(=1)
High logic level.
(g.m.p.)
General machine parameter.
(a.m.p.)
Machine parameters for axes and spindles.
Summary of Contents for CNC 8060
Page 1: ...Ref 1709 8060 8065 CNC Installation manual...
Page 10: ...BLANK PAGE 10...
Page 14: ...BLANK PAGE 14...
Page 20: ...BLANK PAGE 20...
Page 32: ...BLANK PAGE 32...
Page 36: ...BLANK PAGE 36...
Page 38: ...BLANK PAGE 38...
Page 40: ...BLANK PAGE 40...
Page 41: ...PART 1 INSTALLATION MANUAL...
Page 42: ...BLANK PAGE 42...
Page 532: ...Installation manual CNC 8060 CNC 8065 9 CNC VARIABLES 532 REF 1709...
Page 533: ...PART 2 CONCEPTS...
Page 534: ...BLANK PAGE 534...
Page 548: ...Installation manual CNC 8060 CNC 8065 10 GENERAL SETUP Configuration examples 548 REF 1709...
Page 644: ...Installation manual CNC 8060 CNC 8065 14 SUBROUTINES Assistance for subroutines 644 REF 1709...
Page 668: ...Installation manual CNC 8060 CNC 8065 15 HARDWARE Configure the PT100 inputs 668 REF 1709...
Page 697: ...Installation manual CNC 8060 CNC 8065 697 User notes REF 1709...