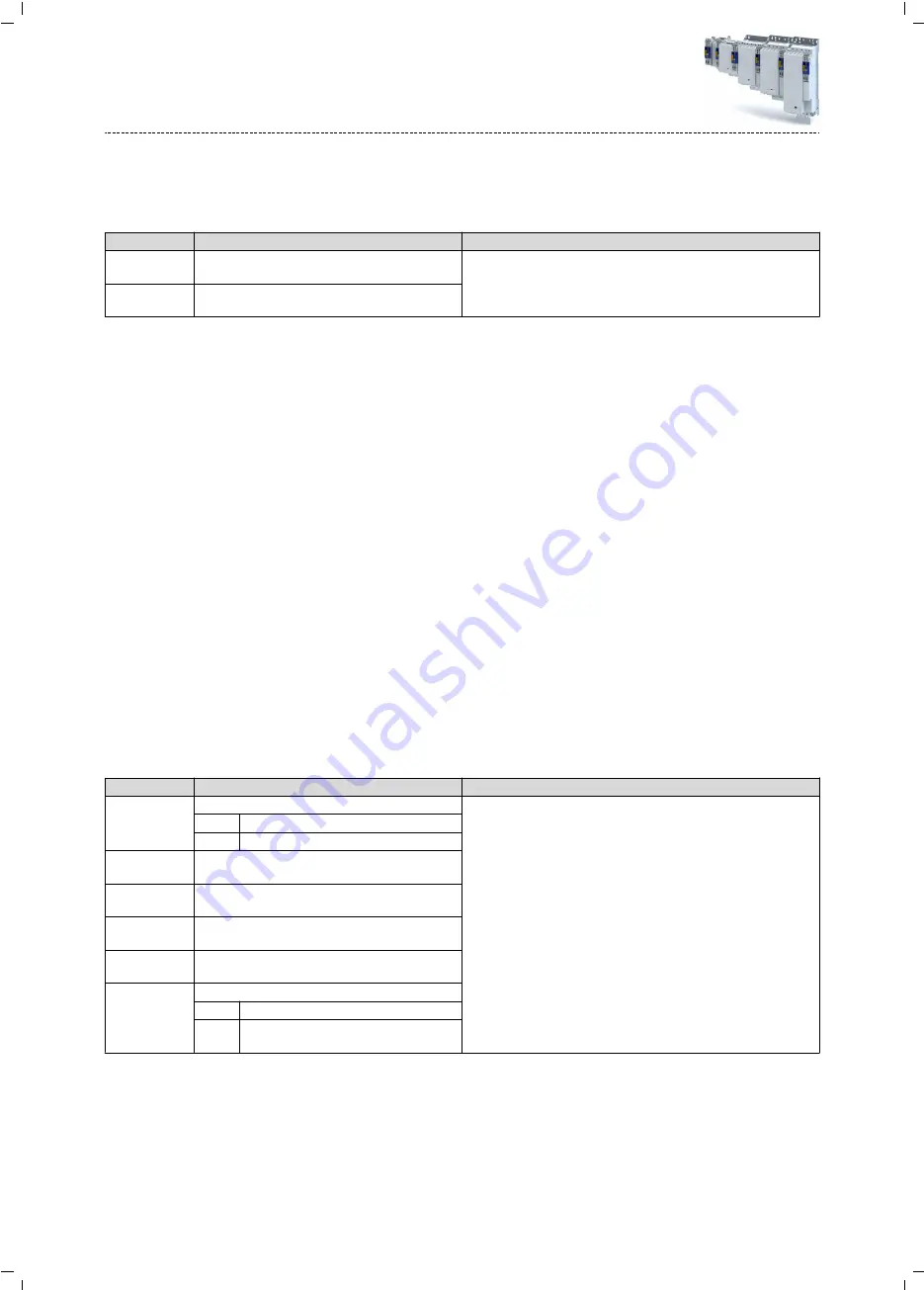
6.2.2
Halt
By triggering this function, the technology application enables the axis to be braked to stand-
still with the values parameterised for deceleration and jerk based on the current setpoints.
Parameter
Address
Name / setting range / [default setting]
Info
0x500A:186
Deceleration of Halt
0.00 ... [1800.00] ... 21474836.47
0x500A:187
Jerk of Halt
0.00 ... [0.00] ... 21474836.47
6.2.3
Following error monitoring
The difference between the setpoint position and the actual position is the following error.
The following error should be "0". If the position control is set optimally, only a minimal fol-
lowing error will occur. The following error is compensated dynamically and does not grow
continuously.
However, certain processes impose a certain maximum limit in terms of the difference
between the setpoint position and the actual position. If the limit is exceeded, it might be (for
example) because of a failure to perform a movement within the machine, meaning that the
system component does not reach the defined position at the relevant point in time. In such
cases, it is appropriate to trigger an error response. The error response is adjustable.
For diagnostic purposes, the current and maximum following error are displayed in the diag-
nostic parameter.
Behaviour when the following error monitoring is active (
= activated)
Two following error limits can be parameterised.
Exceedance of following error limit 1 (
):
•
A warning is displayed.
•
The current movement of the axis is not interrupted.
Exceedance of following error limit 2 (
):
•
The set error response is executed.
Parameter
Address
Name / setting range / [default setting]
Info
0x500A:054
Following error monitoring
false Inactive
true Active
0x500A:055
Following error: Warning threshold
0.0000 ... [180.0000] ... 214748.3647
0x500A:056
Following error: Error threshold
0.0000 ... [360.0000] ... 214748.3647
0x500A:057
Actual following error
•
Read only
0x500A:058
Max. following error
•
Read only
0x500A:059
Response to following error
20 Fault > Application quick stop > Quick stop
21 Fault> Application quick stop > Inverter disa-
bled
Technology application (TA) basic settings
Motion settings
Following error monitoring
54
Содержание i950 Series
Страница 1: ...Inverters i950 servo inverters Commissioning EN ...
Страница 2: ......
Страница 312: ...15 Configure engineering port The given path leads you to the engineering port Configure engineering port 312 ...
Страница 397: ...19 Safety functions Supported safety functions for Basic Safety STO 4Safe Torque Off STO 398 Safety functions 397 ...
Страница 497: ......
Страница 498: ......
Страница 499: ......