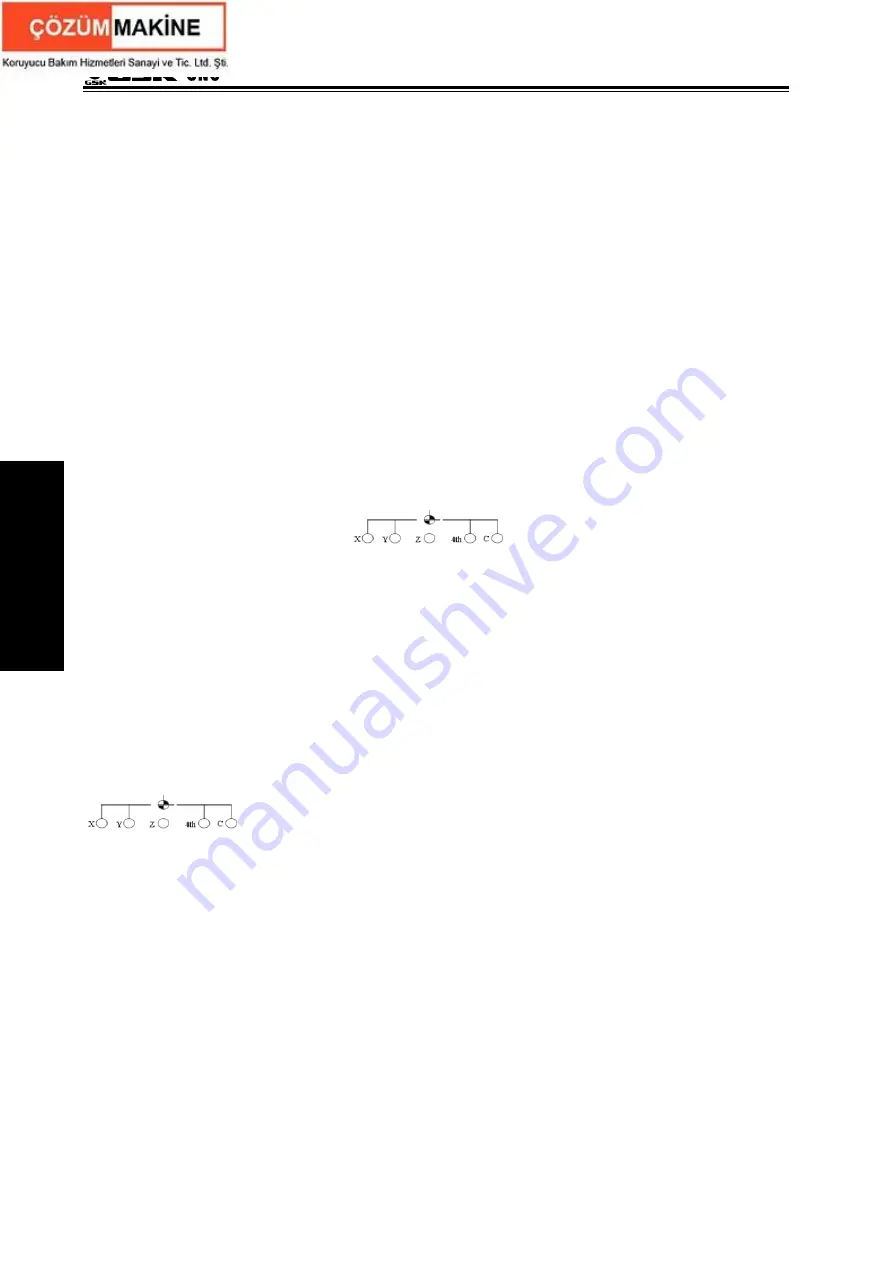
GSK988T Turning CNC System User Manual
264
Ⅱ
Operation
Chapter
Ⅴ
Manual Operation
5.1 Manual Reference Position Return
There is a specified point in CNC machine, which can set the position of the machine working
table. The specified point is taken as the reference position, in the position, the tool is changed and
the coordinate system is set. After connecting the power supply, the tool traverses to the reference
position. Manual reference position return is to use the switch and the button on the panel to traverse
the tool to the reference position.
GSK988T system has three kind of reference position return mode: zero return with a dog, zero
return without a dog and absolute encoder zero return.
¾
Setting a reference position with a dog:
When DLZx(No.1006 Bit 1) is set to 0, the reference position setting with a dog is invalid(i.e. the
reference position setting with a dog is valid), a deceleration switch must be installed on the machine
to realize the reference position return.
Process: The tool traverses in the direction specified by ZMI(No.1006 Bit5), to the deceleration
point at the rapid traverse speed, and then at the FL speed to the reference position. The reference
position return completion light(LED)
lights and the reference position return
ends and the system automatically sets the coordinate system.
Note: The rapid traverse speed, the rapid traverse override F0, the reference position return FL speed for
each axis are separately set by the parameters No.1420, No.1421, No.1425.
¾
Setting reference position without a dog:
When DLZx(No.1006 Bit 1) is set to 1, the reference position setting without a dog is valid. The
reference position return can be completed without a deceleration switch installed on the machine.
Process: The tool traverses in the direction specified by ZMI(No.1006 Bit5) when the machine is
turned on every time and the reference position return is executed, and after the system has checked
the 1
st
PC signal of the motor, the reference position return completion light(LED)
lights and the reference position return ends and the system automatically
sets the coordinate system.
Note: Because there is no dog, the system checks the first PC signal of the encoder as the position of
the reference position, the set reference positions every time are different, and so the tool offset
must be set again after the reference position is set in the mode.
¾
Reference position setting with an absolute encoder
When the machine is allocated with the absolute encoder and the reference position return
function with an absolute position encoder is valid, and the system has not created the reference
position, the reference position return with the absolute position encoder must be executed. After
the tool returns to the reference position, the reference position return completion light LED lights
and the system automatically sets the coordinate system.
The reference position return steps:
Содержание 988T
Страница 6: ...GSK988T Turning CNC System User Manual VI ...
Страница 14: ...GSK988T Turning CNC System User Manual XIV ...
Страница 15: ...Chapter 1 Programming Fundamentals 1 Ⅰ Programming Ⅰ PROGRAMMING ...
Страница 16: ...GSK988T Turning CNC System User Manual 2 Ⅰ Programming ...
Страница 194: ...GSK988T Turning CNC System User Manual 180 Ⅰ Programming ...
Страница 195: ...Chapter Ⅰ Overview 181 Ⅱ Operation Ⅱ OPERATION ...
Страница 196: ...GSK988T Turning CNC System User Manual 182 Ⅱ Operation ...
Страница 215: ...Chapter Ⅲ Windows 201 Ⅱ Operation Note It can be displayed after U disk is inserted in the U disk catalog ...
Страница 217: ...Chapter Ⅲ Windows 203 Ⅱ Operation ...
Страница 267: ...Chapter Ⅲ Windows 253 Ⅱ Operation Fig 3 51 Fig 3 52 ...
Страница 412: ...GSK988T Turning CNC system User Manual 398 Appendix Fig 3 5 Horizontal operation panel appearance dimension ...