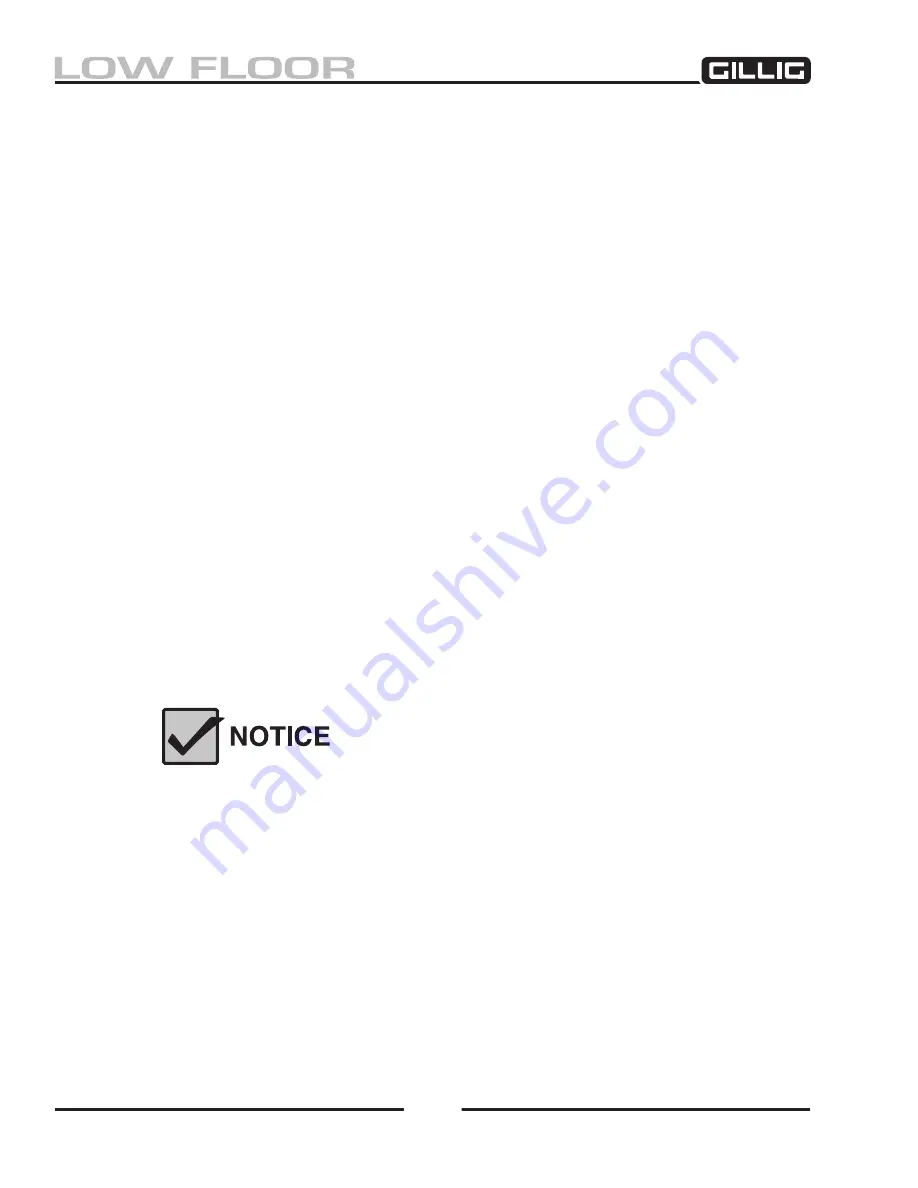
248
Air System
5. Check all lines and fittings leading to and from the air dryer for leakage and integrity.
6. Check the operation of the end cover heater and thermostat assembly during cold weather opera-
tion (Figure 6-
46
).
a. Electric Power to the Dryer: With the ignition “On” check for power at the dryer’s electrical
terminal with a voltmeter or light tester. The air dryer is a single terminal device, so check for
power between the terminal and the end cover or chassis frame. If there is no voltage, look
for a blown fuse, broken wires, or corrosion in the wiring harness.
b. Thermostat and Heater Operation: Turn off the ignition switch and cool the end cover assem-
bly to below 40° F (4° C). Using an ohmmeter, check the resistance between the electrical
terminal and the end cover. The resistance should be 2.0–4.0 ohms for a 12 volt, 60 watt end
cover and 4.0–7.0 ohms for a 24 volt, 120 watt end cover. Warm the end cover to over 90° F
(32° C) and check the resistance as above. The resistance should exceed 1,000 ohms. If the
resistance values are within the stated limits, the thermostat and heater are operating properly.
If the resistance values obtained are outside the stated limits, proceed to the next step.
c. Heater Element Inspection: With the ignition switch in the “
OFF
” position, remove the
thermostat cover. Using an ohmmeter, check the resistance between the metal end cover and
the heater post. For a 12 volt, 60 watt end cover, the resistance should be 2.0–2.8 ohms. For
a 24 volt, 120 watt end cover the resistance should be 4.0–4.6 ohms. If the heater resistance
value is outside these limits, a new or remanufactured end cover should be installed, since the
heater element is not serviceable. If the heater resistance value obtained is within the stated
values, the thermostat should be replaced. Check that a good ground path exists between the
air dryer end cover casting and the coach chassis. Correct the path if needed.
d. Reassembly. Reinstall the thermostat cover. Take special care to assure that the rubber spacer
and the gasket are correctly installed.
7. Rebuild the air dryer, including the desiccant kit, per the maintenance schedule in the Preventive
Maintenance chapter.
The desiccant change interval may vary from vehicle to vehicle. The
typical desiccant cartridge life is three years, although many will
perform for longer periods. In order to take maximum advantage of
desiccant life and assure that replacement is accomplished only when
necessary, it is important that the maintenance procedures above are
performed as scheduled.
Содержание LOW FLOOR
Страница 18: ...Specifications 18...
Страница 58: ...Preventive Maintenance 58...
Страница 110: ...Engine 110...
Страница 138: ...Transmission Driveline Rear Axle 138...
Страница 182: ...Suspension 182...
Страница 260: ...Air System 260...
Страница 420: ...Electrical System 420 Deutsch DT Series Connectors...
Страница 421: ...Electrical System 421...
Страница 422: ...Electrical System 422 Deutsch HD 10 Series Connectors...
Страница 423: ...Electrical System 423...
Страница 424: ...Electrical System 424 Deutsch HD 30 Series Connectors...
Страница 425: ...Electrical System 425...
Страница 442: ...Heating Air Conditioning 442...
Страница 486: ...Body and Interior 486 Driver s Seat Troubleshooting Use the following chart to troubleshoot the USSC seat...
Страница 492: ...Body and Interior 492 Figure 11 33 USSC Seat Assembly...
Страница 493: ...Body and Interior 493 Figure 11 34 USSC Seat Suspension Assembly...
Страница 495: ...Body and Interior 495 Figure 11 37 Seat Air Connections...
Страница 506: ...GILLIG CORPORATION 25800 Clawiter Road Hayward CA 94545 Phone 510 785 1500 Fax 510 785 6819 Printed November 2006...