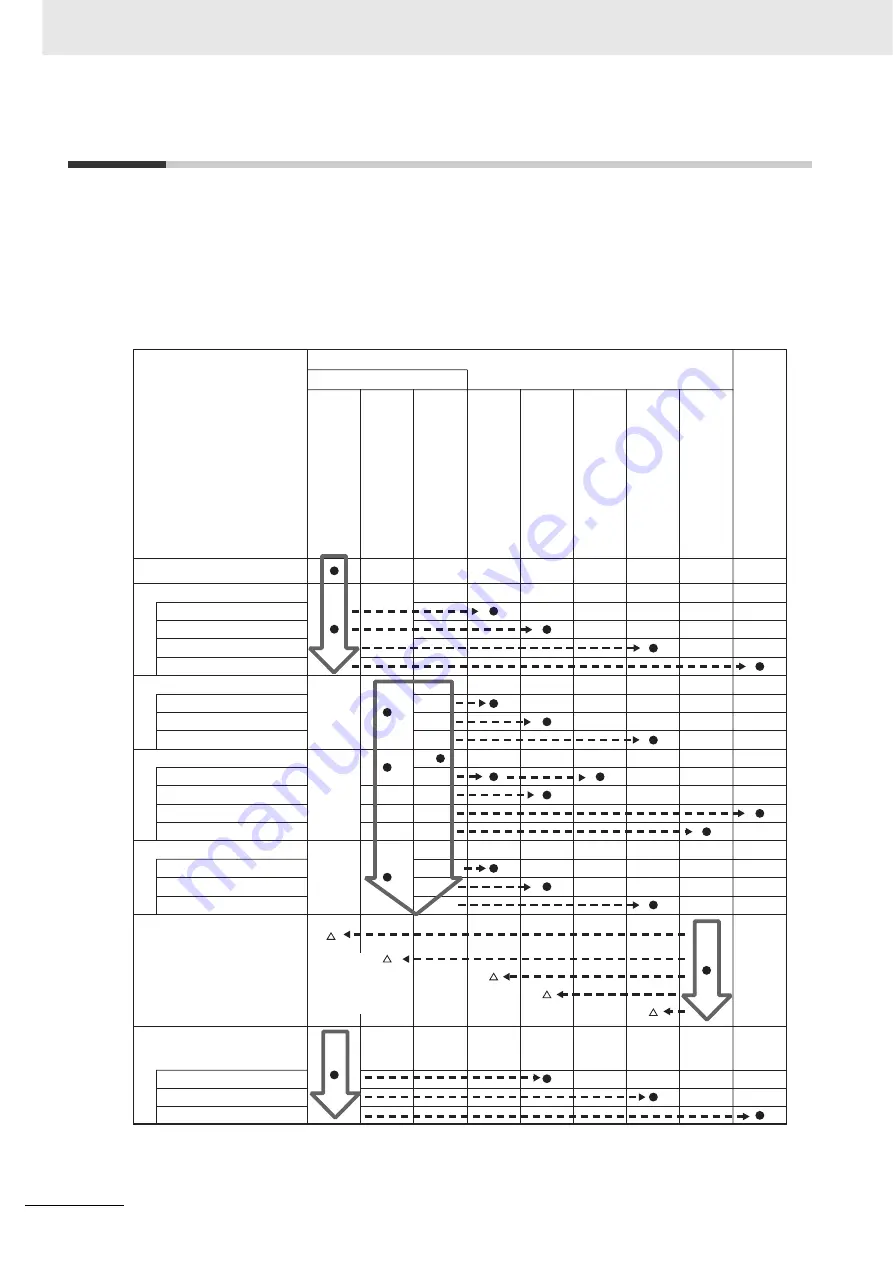
Relevant Manuals
2
NJ-series CPU Unit Motion Control User’s Manual (W507)
Relevant Manuals
There are three manuals that provide basic information on the NJ-series CPU Units: the
NJ-series CPU
Unit Hardware User’s Manual
, the
NJ-series CPU Unit Software User’s Manual
(this manual), and the
NJ-series Instructions Reference Manual
.
Most operations are performed from the Sysmac Studio Automation Software. Refer to the
Sysmac Stu-
dio Version 1 Operation Manual
(Cat. No. W504) for information on the Sysmac Studio.
Other manuals are necessary for specific system configurations and applications.
Read all of the manuals that are relevant to your system configuration and application to make the most
of the NJ-series CPU Unit.
NJ-series User’s Manuals
Basic information
Introduction to NJ-series Controllers
Setting devices and hardware
Using motion control
Using EtherCAT
Using EtherNet/IP
Using CJ-series Units
Software settings
Using motion control
Using EtherCAT
Using EtherNet/IP
Programming
Using motion control
Using EtherCAT
Using CJ-series Units
Programming error processing
Testing operation and debugging
Using motion control
Using EtherCAT
Using EtherNet/IP
Maintenance
Using EtherCAT
Using EtherNet/IP
Using CJ-series Units
NJ-series CPU Unit
Hardware User´s Manual
NJ-series CPU Unit
Software User´s Manual
NJ-series Instructions
Reference Manual
NJ-series CPU Unit Motion
Control User´s Manual
NJ-series CPU Unit Built-in
EtherCAT Port User´s Manual
NJ-series Motion Control
Instructions Reference Manual
NJ-series CPU Unit Built-in
EtherNet/IP Port User´s Manual
NJ-series Troubleshooting Manual
CJ-series Special Unit Operation
Manuals for NJ-series CPU Unit
Troubleshooting and managing
errors in an NJ-series Controller
Use the
relevant
manuals for
references
according to
any error that
occurs.
Summary of Contents for NJ501-1300
Page 12: ...Sections in this Manual 10 NJ series CPU Unit Motion Control User s Manual W507...
Page 18: ...16 NJ series CPU Unit Motion Control User s Manual W507 CONTENTS...
Page 22: ...Read and Understand this Manual 20 NJ series CPU Unit Motion Control User s Manual W507...
Page 34: ...Revision History 32 NJ series CPU Unit Motion Control User s Manual W507...
Page 86: ...3 Configuring Axes and Axes Groups 3 28 NJ series CPU Unit Motion Control User s Manual W507...
Page 122: ...5 Motion Control Parameters 5 24 NJ series CPU Unit Motion Control User s Manual W507...
Page 158: ...6 Motion Control Programming 6 36 NJ series CPU Unit Motion Control User s Manual W507...
Page 166: ...7 Manual Operation 7 8 NJ series CPU Unit Motion Control User s Manual W507...
Page 182: ...8 Homing 8 16 NJ series CPU Unit Motion Control User s Manual W507...
Page 346: ...10 Sample Programming 10 92 NJ series CPU Unit Motion Control User s Manual W507...
Page 422: ...Appendices A 18 NJ series CPU Unit Motion Control User s Manual W507...
Page 423: ...Index 1 NJ series CPU Unit Motion Control User s Manual W507 I Index...
Page 430: ...Index 8 NJ series CPU Unit Motion Control User s Manual W507 Index...