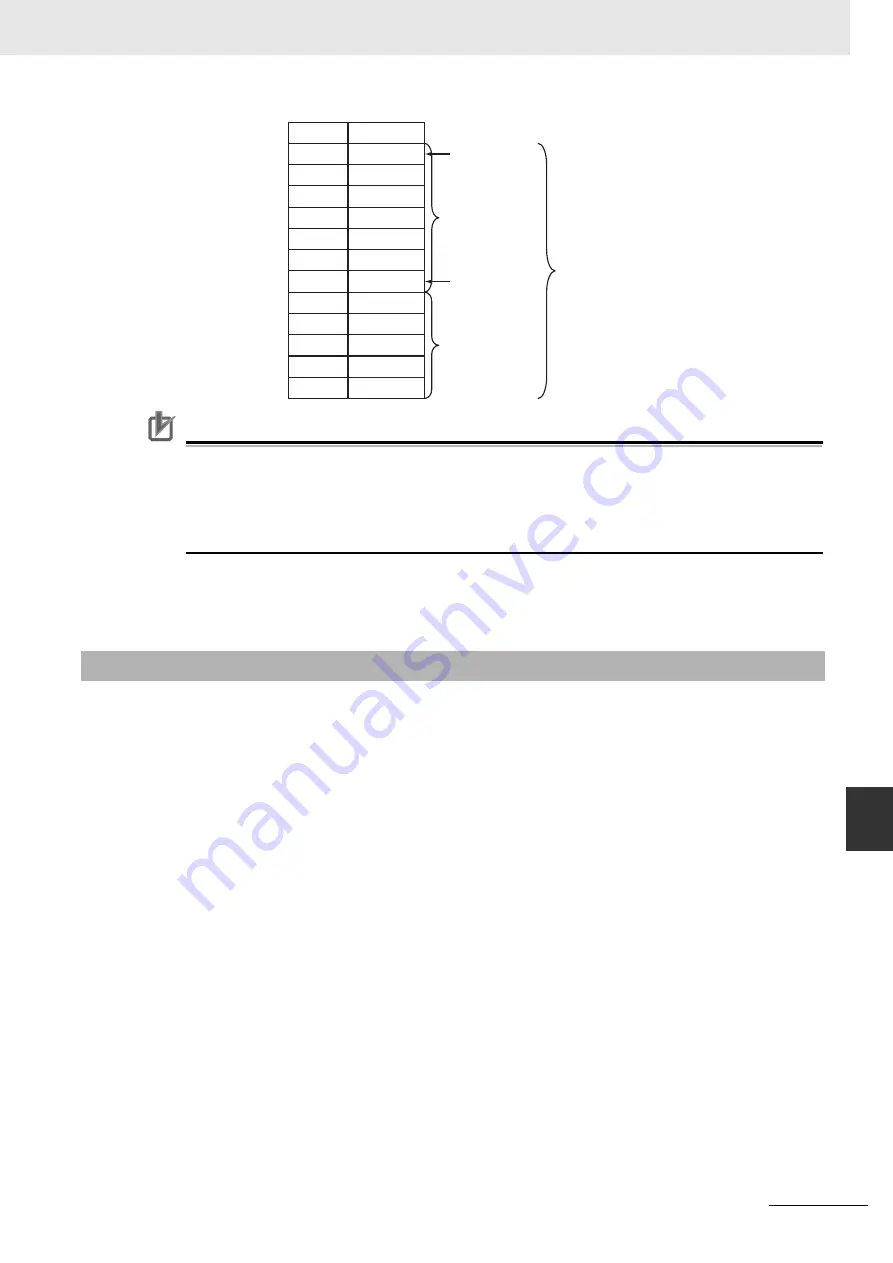
9-19
9 Motion Control Functions
NJ-series CPU Unit Motion Control User’s Manual (W507)
9-2 Sing
le-axi
s Sync
hr
o
n
iz
ed
Co
ntr
o
l
9
9-2-6
S
y
nchrono
us P
ositio
ning
Precautions for Correct Use
Precautions for Correct Use
•
You cannot change the maximum number of cam data from the user program.
•
Execute this instruction after overwriting the cam data in any way that changes the number of
valid cam data. If the number of valid cam data is not updated, the cam operation and the
operation of the
EndOfProfile
(End of Cam Cycle) of the MC_CamIn instruction may not be as
expected.
For details on the Set Cam Table Properties instruction, refer to the MC_SetCamTableProperty (Set
Cam Table Properties) instruction in the
NJ-series Motion Control Instructions Reference Manual
(Cat.
No. W508).
This function performs positioning using a trapezoidal curve while synchronizing the specified slave
axis to the specified master axis. This is a type of electronic cam, but it does not use cam tables created
in the Cam Editor. Operation starts when the MC_MoveLink (Synchronous Positioning) instruction is
executed. Use the MC_Stop instruction to stop the axes in motion. Operation is performed for the
Slave
(Slave Axis) and the following are set:
Master
(Master Axis),
MasterDistance
(Master Distance),
Mas-
terDistanceInACC
(Master Distance In Acceleration),
MasterDistanceInDEC
(Master Distance In Decel-
eration),
SlaveDistance
(Slave Axis Travel Distance), and
MasterStartDistance
(Master Following
Distance). The command position or actual position can be specified for the master axis. You can spec-
ify one of the following as the start condition for synchronous operation: start of instruction, when trigger
is detected, or when master axis reaches the master following distance.
The velocity and position of the slave axis are determined by the ratio of the travel distances of the mas-
ter axis and the slave axis as shown in the following figure. The sync start position shown in the follow-
ing figure represents the position where the sync start condition is met.
9-2-6
Synchronous Positioning
.
.
.
.
.
.
.
.
.
.
.
.
.
.
.
.
.
.
MyCam1 [0]
MyCam1 [997]
MyCam1 [998]
MyCam1 [999]
MyCam1 [1000]
MyCam1 [4999]
Phase
Displacement
0
0
0
0
Maximum number of data: 5,000
Invalid data
Cam end point
Valid data
Cam start point
Cam data structure array
359.8
359.9
360.0
0
2
1
0
0
Summary of Contents for NJ501-1300
Page 12: ...Sections in this Manual 10 NJ series CPU Unit Motion Control User s Manual W507...
Page 18: ...16 NJ series CPU Unit Motion Control User s Manual W507 CONTENTS...
Page 22: ...Read and Understand this Manual 20 NJ series CPU Unit Motion Control User s Manual W507...
Page 34: ...Revision History 32 NJ series CPU Unit Motion Control User s Manual W507...
Page 86: ...3 Configuring Axes and Axes Groups 3 28 NJ series CPU Unit Motion Control User s Manual W507...
Page 122: ...5 Motion Control Parameters 5 24 NJ series CPU Unit Motion Control User s Manual W507...
Page 158: ...6 Motion Control Programming 6 36 NJ series CPU Unit Motion Control User s Manual W507...
Page 166: ...7 Manual Operation 7 8 NJ series CPU Unit Motion Control User s Manual W507...
Page 182: ...8 Homing 8 16 NJ series CPU Unit Motion Control User s Manual W507...
Page 346: ...10 Sample Programming 10 92 NJ series CPU Unit Motion Control User s Manual W507...
Page 422: ...Appendices A 18 NJ series CPU Unit Motion Control User s Manual W507...
Page 423: ...Index 1 NJ series CPU Unit Motion Control User s Manual W507 I Index...
Page 430: ...Index 8 NJ series CPU Unit Motion Control User s Manual W507 Index...