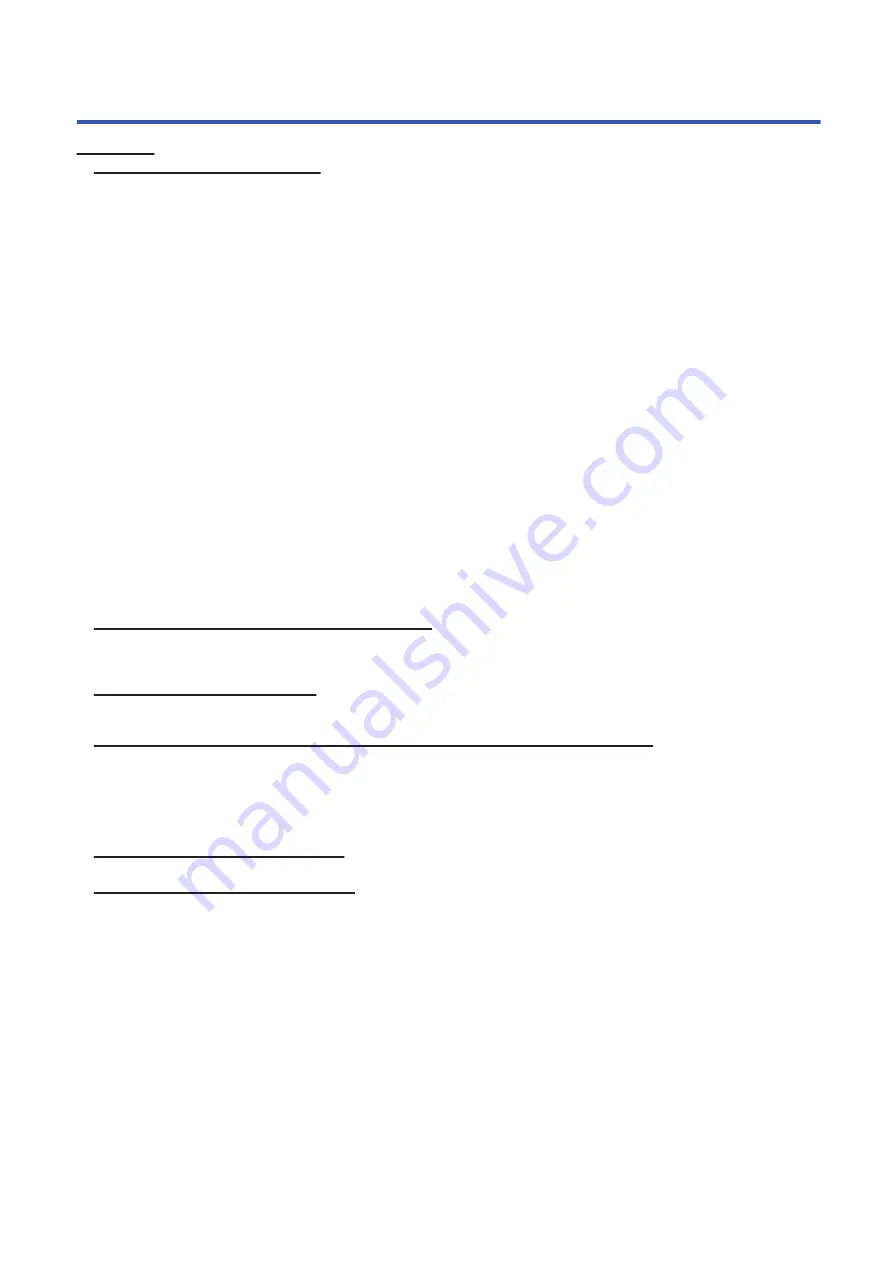
255
WARRANTY
Warranty
1. Warranty period and coverage
We will repair any failure or defect hereinafter referred to as "failure" in our FA equipment hereinafter referred to as the "Product" arisen
during warranty period at no charge due to causes for which we are responsible through the distributor from which you purchased the
Product or our service provider. However, we will charge the actual cost of dispatching our engineer for an on-site repair work on
request by customer in Japan or overseas countries. We are not responsible for any on-site readjustment and/or trial run that may be
required after a defective unit are repaired or replaced.
[Term]
For terms of warranty, please contact your original place of purchase.
[Limitations]
(1) You are requested to conduct an initial failure diagnosis by yourself, as a general rule.
It can also be carried out by us or our service company upon your request and the actual cost will be charged. However, it will not
be charged if we are responsible for the cause of the failure.
(2) This limited warranty applies only when the condition, method, environment, etc. of use are in compliance with the terms and
conditions and instructions that are set forth in the instruction manual and user manual for the Product and the caution label affixed
to the Product.
(3) Even during the term of warranty, the repair cost will be charged on you in the following cases;
1. a failure caused by your improper storing or handling, carelessness or negligence, etc., and a failure caused by your hardware
or software problem
2. a failure caused by any alteration, etc. to the Product made on your side without our approval
3. a failure which may be regarded as avoidable, if your equipment in which the Product is incorporated is equipped with a safety
device required by applicable laws and has any function or structure considered to be indispensable according to a common
sense in the industry
4. a failure which may be regarded as avoidable if consumable parts designated in the instruction manual, etc. are duly maintained
and replaced
5. any replacement of consumable parts (battery, fan, smoothing capacitor, etc.)
6. a failure caused by external factors such as inevitable accidents, including without limitation fire and abnormal fluctuation of
voltage, and acts of God, including without limitation earthquake, lightning and natural disasters
7. a failure generated by an unforeseeable cause with a scientific technology that was not available at the time of the shipment of
the Product from our company
8. any other failures which we are not responsible for or which you acknowledge we are not responsible for
2. Term of warranty after the stop of production
(1) We may accept the repair at charge for another seven (7) years after the production of the product is discontinued. The
announcement of the stop of production for each model can be seen in our Sales and Service, etc.
(2) Please note that the Product (including its spare parts) cannot be ordered after its stop of production.
3. Service in overseas countries
Our regional FA Center in overseas countries will accept the repair work of the Product. However, the terms and conditions of the repair
work may differ depending on each FA Center. Please ask your local FA center for details.
4. Exclusion of loss in opportunity and secondary loss from warranty liability
Regardless of the gratis warranty term, Mitsubishi shall not be liable for compensation to:
(1) Damages caused by any cause found not to be the responsibility of Mitsubishi.
(2) Loss in opportunity, lost profits incurred to the user by Failures of Mitsubishi products.
(3) Special damages and secondary damages whether foreseeable or not, compensation for accidents, and compensation for
damages to products other than Mitsubishi products.
(4) Replacement by the user, maintenance of on-site equipment, start-up test run and other tasks.
5. Change of Product specifications
Specifications listed in our catalogs, manuals or technical documents may be changed without notice.
6. Application and use of the Product
(1) For the use of our AC Servo, its applications should be those that may not result in a serious damage even if any failure or
malfunction occurs in AC Servo, and a backup or fail-safe function should operate on an external system to AC Servo when any
failure or malfunction occurs.
(2) Our AC Servo is designed and manufactured as a general purpose product for use at general industries.
Therefore, applications substantially influential on the public interest for such as atomic power plants and other power plants of
electric power companies, and also which require a special quality assurance system, including applications for railway companies
and government or public offices are not recommended, and we assume no responsibility for any failure caused by these
applications when used.
In addition, applications which may be substantially influential to human lives or properties for such as airlines, medical treatments,
railway service, incineration and fuel systems, man-operated material handling equipment, entertainment machines, safety
machines, etc. are not recommended, and we assume no responsibility for any failure caused by these applications when used.
We will review the acceptability of the abovementioned applications, if you agree not to require a specific quality for a specific
application. Please contact us for consultation.
(3) Mitsubishi Electric shall have no responsibility or liability for any problems involving programmable controller trouble and system
trouble caused by DoS attacks, unauthorized access, computer viruses, and other cyberattacks.