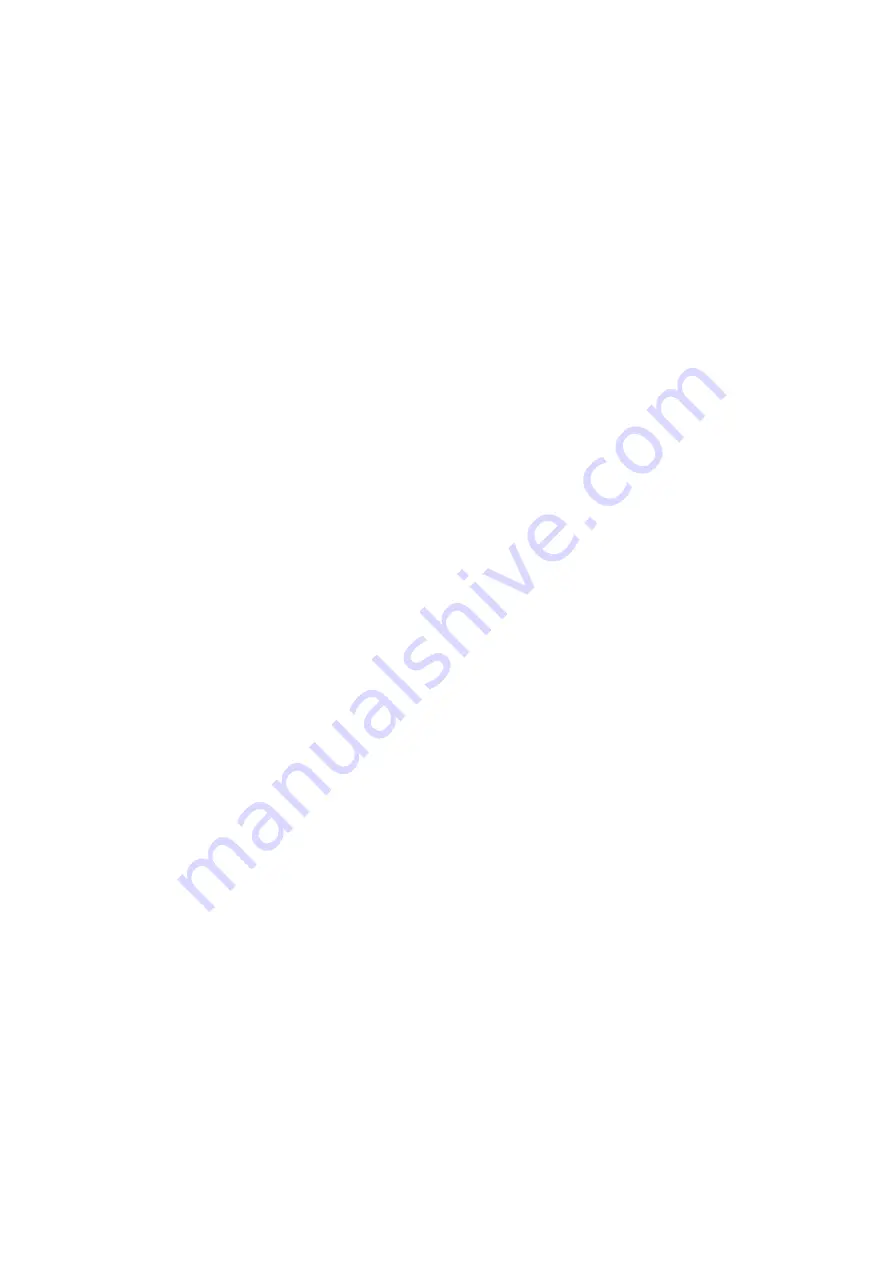
Appendix
HTX30 Product Manual
8-38
JIMn parameter tree
SWVer (Software version)
BbVer (Boot Block Software version)
BkVer (Backup Software version)
Amend (Amendment)
PCBAm (PCB amendment)
JtMdl (Jet Model)
JtRev (Jet Type Rev)
Str / Enab (Steering Enabled)
Rev / Enab (Reverse Enabled)
Calib / Type (Calibration Type)
Unpwr / Calib (Unpowered Calibration)
Str / Port (Limit Port)
Str / Stbd (Limit Stbd)
Str / Mid (Steering Mid)
Rev / Up (Limit Up)
Rev / Down (Limit Down)
Zero / Spd (Zero Speed)
Pwred / Calib (Powered Calibration)
DbPrt (Deadband Port)
DbStb (Deadband Stbd)
DbUp (Deadband Up)
DbDwn (Deadband Down)
Lmt / Port (Limit Port)
Lmt / Stbd (Limit Stbd)
Mid (Steering Mid)
Lmt / Up (Limit Up)
Lmt / Down (Limit Down)
Zero / Spd (Zero Speed)
Str / Ctrl (Steering Control)
Kp (Kp)
Ki (Ki)
Kd (Kd)
DithA (Dither Ampilitude)
DithT (Dither Time Period)
Dith / Stat (Dither when Stat)
SUPrt (Drive Setup Port)
SUStb (Drive Setup Stbd)
Rev / Ctrl (Reverse Control)
KpUp (Kp Up)
KpDn (Kp Down)
Ki (Ki)
Kd (Kd)
DithA (Dither Ampilitude)
DithT (Dither Time Period)
Dith / Stat (Dither when Stat)
SUUp (Drive Setup Up)
SUDwn (Drive Setup Down)
Str / Adv (Steering Advanced)
Fbk / Invrt (Feedback Invert)
DbOff (Deadband Offset)
Drv / MaxV (Drive Max Volt)
Err / Min (Error min)
Alarm / time (Alarm time)
Alarm / Retry (Alarm retries)
Str / BOff (Limit Backoff)
Str / Limit (Demand Rate Limit)
Rev / Adv (Reverse Advanced)
Fbk / Invrt (Feedback Invert)
DbOff (Deadband Offset)
Drv / MaxV (Drive Max Volt)
Err / Min (Error min)
Alarm / Time (Alarm time)
Alarm / Retry (Alarm retries)
Max / Lin (Max Linear)
Up / BOff (Rev Up Limit Backoff)
Dwn / BOff (Rev Down Limit Backoff)
Rev / Limit (Demand Rate Limit)
Adv (Advanced)
DBIni (Drive Deadband Initial)
HydIn (Hydraulic Input)
ByFlt (Bypass ADC filter)
Drv / Comp (Drive Compensation)
SWght (Str Load Weight)
RWght (Rev Load Weight)
LTotD (Load Total Drv)
Sens (Sensors)
OilT (JHPU Oil Temp)
OilL (JHPU Oil Level)
brgT (Bearing Oil Temp Switch)
Jet / Rpm / PPR (Jet Rpm Pulses per Rev)
Jet / Rpm / Stagd (Jet Rpm Staggered)
Bkp (Backup)
StrKp (Str Kp)
RevKp (Rev Kp)
StrKi (Str Ki)
RevKi (Rev Ki)
Eng / Mode (Eng Dmd Mode)
Eng / High (Eng Dmd High)
Eng / Low (Eng Dmd Low)
EngA (Eng Dmd A)
EngB (Eng Dmd B)
Eng / Inv (Eng Dmd Invert)
Summary of Contents for HTX30
Page 1: ...HTX30 HTX30 Product Manual R0A5 blue ARROW...
Page 8: ...1 vi...
Page 20: ......
Page 26: ......
Page 178: ......
Page 181: ...Notes...