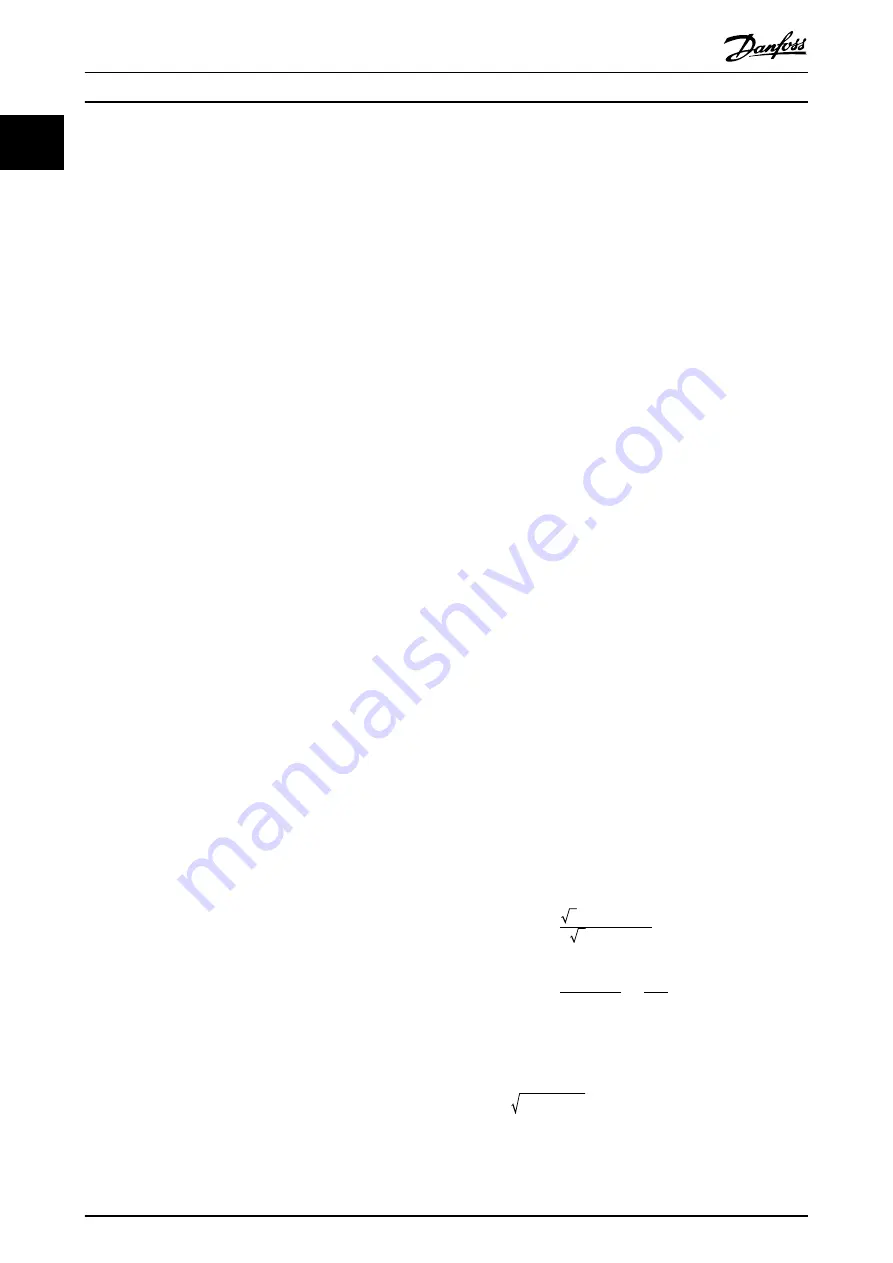
NLCP
Numerical local control panel interface for control and
programming of the frequency converter. The display is
numerical and the panel is used to show process values.
The NLCP has no storage and copy functions.
lsb
Least significant bit.
msb
Most significant bit.
MCM
Short for mille circular mil, an American measuring unit for
cable cross-section. 1 MCM=0.5067 mm
2
.
Online/offline parameters
Changes to online parameters are activated immediately
after the data value is changed. Press [OK] to activate
changes to off-line parameters.
Process PID
The PID control maintains the required speed, pressure,
temperature, and so on, by adjusting the output frequency
to match the varying load.
PCD
Process control data.
Power cycle
Switch off the mains until the display (LCP) is dark, then
turn power on again.
Pulse input/incremental encoder
An external, digital pulse transmitter used for feeding back
information on motor speed. The encoder is used in
applications where great accuracy in speed control is
required.
RCD
Residual current device.
Set-up
Save parameter settings in 4 set-ups. Change between the
4 parameter set-ups and edit 1 set-up, while another set-
up is active.
SFAVM
Switching pattern called stator flux-oriented asynchronous
vector modulation (
parameter 14-00 Switching Pattern
).
Slip compensation
The frequency converter compensates for the motor slip by
giving the frequency a supplement that follows the
measured motor load keeping the motor speed almost
constant.
SLC
The SLC (smart logic control) is a sequence of user-defined
actions executed when the associated user-defined events
are evaluated as true by the SLC. (See
chapter 3.13 Parameters: 13-** Smart Logic Control
STW
Status word.
FC standard bus
Includes RS485 bus with FC protocol or MC protocol. See
parameter 8-30 Protocol
.
THD
Total harmonic distortion states the total contribution of
harmonics.
Thermistor
A temperature-dependent resistor placed on the frequency
converter or the motor.
Trip
A state entered in fault situations, for example if the
frequency converter is subject to an overtemperature or
when the frequency converter is protecting the motor,
process, or mechanism. The frequency converter prevents a
restart until the cause of the fault has disappeared. To
cancel the trip state, restart the frequency converter. Do
not use the trip state for personal safety.
Trip lock
The frequency converter enters this state in fault situations
to protect itself. The frequency converter requires physical
intervention, for example when there is a short circuit on
the output. A trip lock can only be canceled by discon-
necting mains, removing the cause of the fault, and
reconnecting the frequency converter. Restart is prevented
until the trip state is canceled by activating reset or,
sometimes, by being programmed to reset automatically.
Do not use the trip lock state for personal safety.
VT characteristics
Variable torque characteristics used for pumps and fans.
VVC
+
If compared with standard voltage/frequency ratio control,
voltage vector control (VVC
+
) improves the dynamics and
the stability, both when the speed reference is changed
and in relation to the load torque.
60
°
AVM
60
°
asynchronous vector modulation
(
parameter 14-00 Switching Pattern
).
Power factor
The power factor is the relation between I
1
and I
RMS
.
Power factor =
3 x U x I
1
cosϕ
3 x U x I
RMS
The power factor for 3-phase control:
Power factor = I1 x cosϕ1
I
RMS
=
I
1
I
RMS
since cosϕ1 = 1
The power factor indicates to which extent the frequency
converter imposes a load on the mains supply.
The lower the power factor, the higher the I
RMS
for the
same kW performance.
I
RMS
= I
1
2
+ I
5
2
+ I
7
2
+ .. + I
n
2
In addition, a high power factor indicates that the different
harmonic currents are low.
Introduction
VLT
®
AutomationDrive FC 301/302
6
Danfoss A/S © 10/2018 All rights reserved.
MG33MP02
1
1
Summary of Contents for VLT AutomationDrive FC 302
Page 2: ......