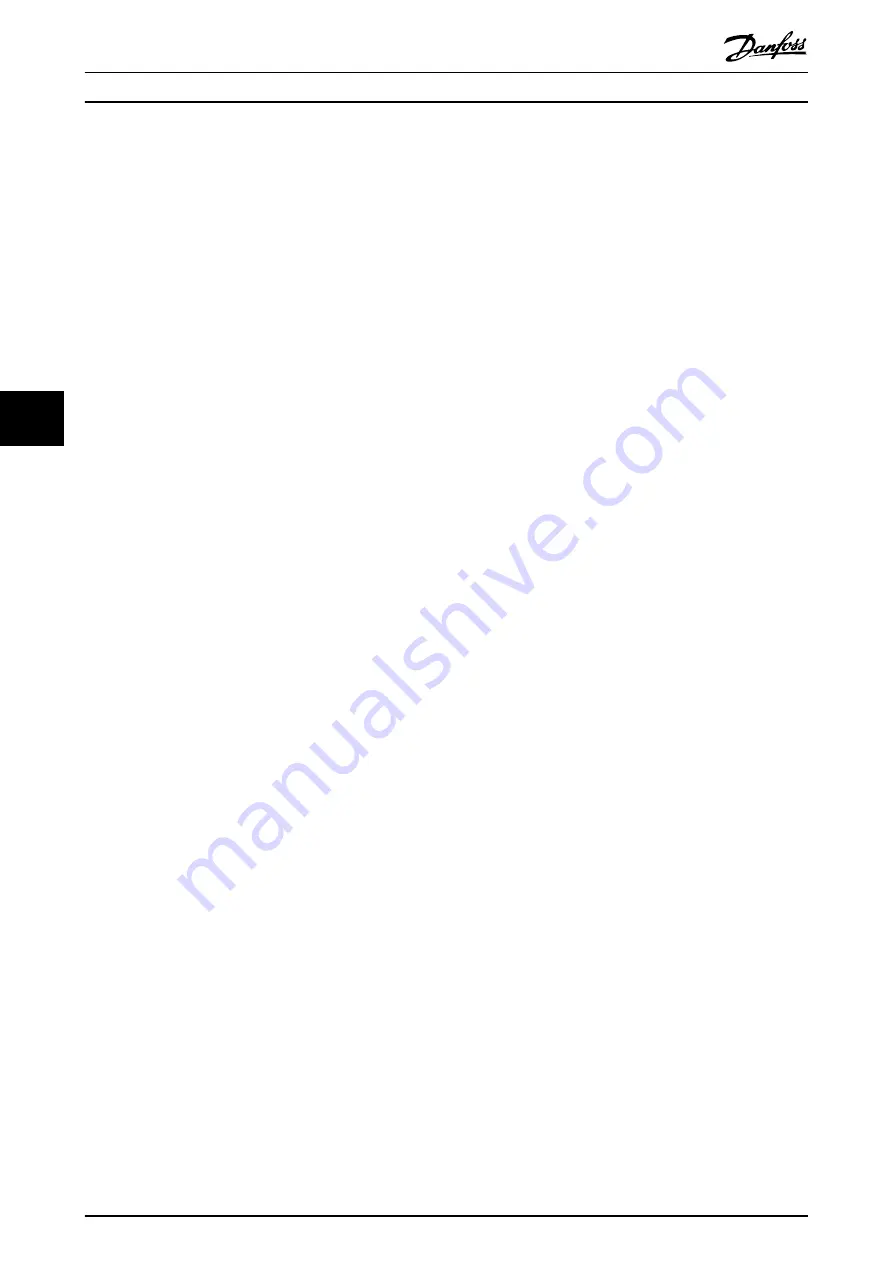
Troubleshooting
•
Check the settings in
parameter 1-24 Motor
Current
.
ALARM 53, AMA motor too big
The motor is too large for the AMA to operate.
ALARM 54, AMA motor too small
The motor is too small for the AMA to operate.
ALARM 55, AMA parameter out of range
The AMA cannot run because the parameter values of the
motor are outside of the acceptable range.
ALARM 56, AMA interrupted by user
The AMA is manually interrupted.
ALARM 57, AMA internal fault
Try to restart the AMA. Repeated restarts can overheat the
motor.
ALARM 58, AMA Internal fault
Contact the Danfoss supplier.
WARNING 59, Current limit
The current is higher than the value in
parameter 4-18 Current Limit
. Ensure that the motor data in
parameters 1-20 to 1-25
is set correctly. Increase the current
limit if necessary. Ensure that the system can operate safely
at a higher limit.
WARNING 60, External interlock
A digital input signal indicates a fault condition external to
the frequency converter. An external interlock has
commanded the frequency converter to trip. Clear the
external fault condition. To resume normal operation, apply
24 V DC to the terminal programmed for external interlock,
and reset the frequency converter.
WARNING/ALARM 61, Feedback error
An error between calculated speed and speed
measurement from feedback device.
Troubleshooting
•
Check the settings for warning/alarm/disabling in
parameter 4-30 Motor Feedback Loss Function
.
•
Set the tolerable error in
parameter 4-31 Motor
Feedback Speed Error
.
•
Set the tolerable feedback loss time in
parameter 4-32 Motor Feedback Loss Timeout
.
WARNING/ALARM 62, Output frequency at maximum
limit
If the output frequency reaches the value set in
parameter 4-19 Max Output Frequency
, the drive issues a
warning. The warning ceases when the output drops
below the maximum limit. If the drive is unable to limit
the frequency, it trips and issues an alarm. The latter may
happen in the flux mode if the drive loses control of the
motor.
Troubleshooting
•
Check the application for possible causes.
•
Increase the output frequency limit. Ensure that
the system can operate safely at a higher output
frequency.
ALARM 63, Mechanical brake low
The actual motor current has not exceeded the release
brake current within the start delay time window.
WARNING 64, Voltage limit
The combination of load and speed requires a motor
voltage higher than the actual DC-link voltage.
WARNING/ALARM 65, Control card over temperature
The cutout temperature of the control card is 85
°
C
(185
°
F).
Troubleshooting
•
Check that the ambient operating temperature is
within the limits.
•
Check for clogged filters.
•
Check the fan operation.
•
Check the control card.
WARNING 66, Heat sink temperature low
The frequency converter is too cold to operate. This
warning is based on the temperature sensor in the IGBT
module. Increase the ambient temperature of the unit.
Also, a trickle amount of current can be supplied to the
frequency converter whenever the motor is stopped by
setting
parameter 2-00 DC Hold/Preheat Current
to 5% and
parameter 1-80 Function at Stop
.
ALARM 67, Option module configuration has changed
One or more options have either been added or removed
since the last power-down. Check that the configuration
change is intentional and reset the unit.
ALARM 68, Safe Stop activated
Safe Torque Off (STO) has been activated. To resume
normal operation, apply 24 V DC to terminal 37, then send
a reset signal (via bus, digital I/O, or by pressing [Reset]).
ALARM 69, Power card temperature
The temperature sensor on the power card is either too
hot or too cold.
Troubleshooting
•
Check that the ambient operating temperature is
within limits.
•
Check for clogged filters.
•
Check fan operation.
•
Check the power card.
ALARM 70, Illegal FC configuration
The control card and power card are incompatible. To
check compatibility, contact the Danfoss supplier with the
type code from the unit nameplate and the part numbers
of the cards.
Troubleshooting
VLT
®
AutomationDrive FC 301/302
336
Danfoss A/S © 10/2018 All rights reserved.
MG33MP02
6
6
Summary of Contents for VLT AutomationDrive FC 302
Page 2: ......