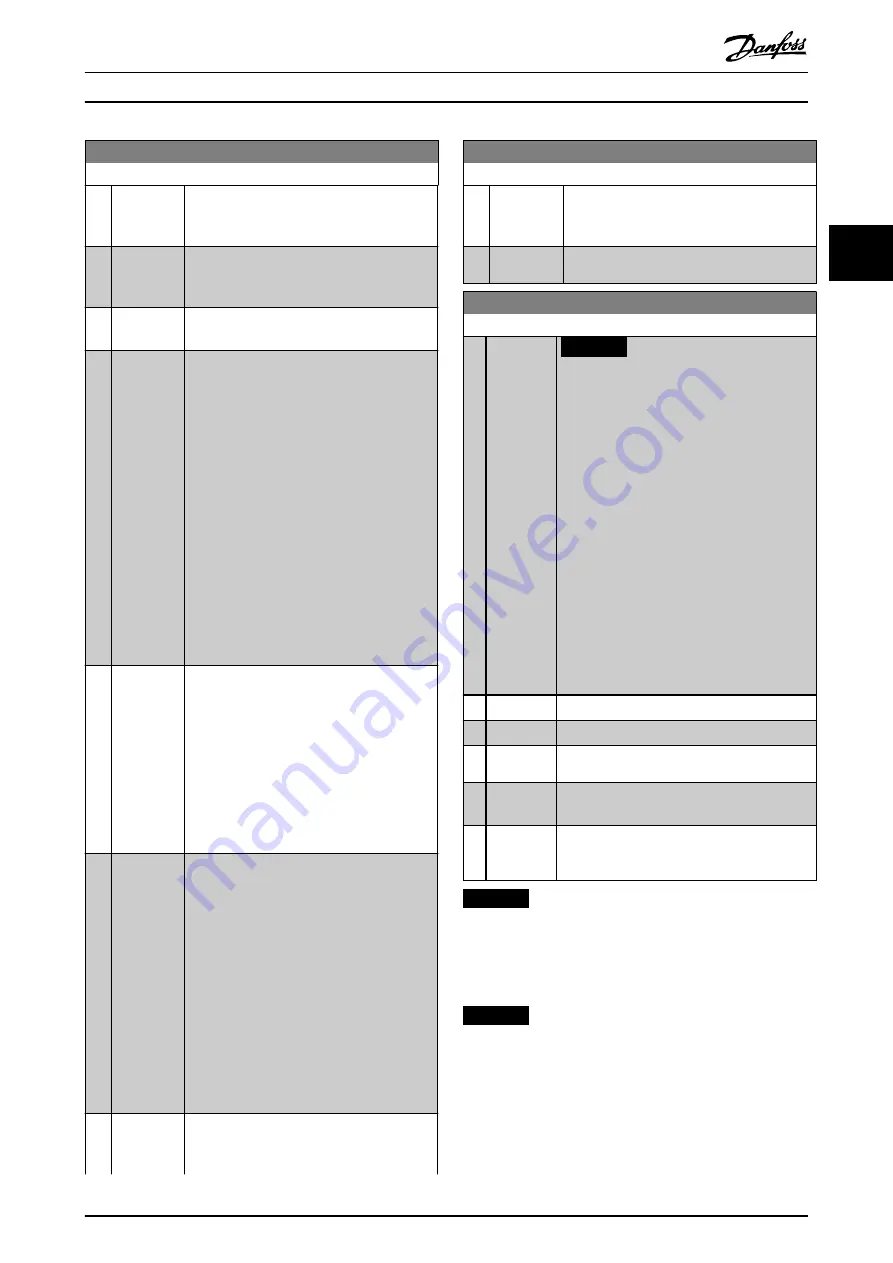
1-72 Start Function
Option:
Function:
[0] DC Hold/
delay time
Energizes motor with a DC hold current
(
parameter 2-00 DC Hold Current
) during the
start delay time.
[1] DC Brake/
delay time
Energizes motor with a DC brake current
(
parameter 2-01 DC Brake Current
) during the
start delay time.
[2]
*
Coast/delay
time
Motor coasted during the start delay time
(inverter off).
[3] Start speed
cw
Only possible with VVC
+
.
Connect the function described in
parameter 1-74 Start Speed [RPM]
and
in the start delay
time.
Regardless of the value applied by the
reference signal, the output speed applies the
setting of the start speed in
parameter 1-74 Start Speed [RPM]
or
parameter 1-75 Start Speed [Hz]
, and the
output current corresponds to the setting of
the start current in
. This function is typically used in
hoisting applications without counterweight
and especially in applications with a cone-
motor where the start is clockwise, followed
by rotation in the reference direction.
[4] Horizontal
operation
Only possible with VVC
+
.
For obtaining the function described in
parameter 1-74 Start Speed [RPM]
and
during the start
delay time. The motor rotates in the reference
direction. If the reference signal equals 0,
parameter 1-74 Start Speed [RPM]
is ignored
and the output speed equals 0. The output
current corresponds to the setting of the start
current in
.
[5] VVC+/Flux
clockwise
For the function described in
parameter 1-74 Start Speed [RPM]
only. The
start current is calculated automatically. This
function uses the start speed in the start delay
time only. Regardless of the value set by the
reference signal, the output speed equals the
setting of the start speed in
parameter 1-74 Start Speed [RPM]
.
[3] Start
speed/current clockwise
and
[5] VVC
+
/Flux
clockwise
are typically used in hoisting
applications.
[4] Start speed/current in reference
direction
is particularly used in applications
with counterweight and horizontal movement.
[6] Hoist Mech.
Brake Rel
For utilizing mechanical brake control
functions (
to
parameter 2-28 Gain Boost Factor
). This
1-72 Start Function
Option:
Function:
parameter is only active in flux control
principle, in a mode with motor feedback or
sensorless mode.
[7] VVC+/Flux
counter-cw
1-73 Flying Start
Option:
Function:
NOTICE
This parameter cannot be adjusted while
the motor is running.
This function makes it possible to catch a freely
spinning motor, for exmaple coasted because of
mains dropout.
When Flying start is enabled,
and
have no function.
When options
[1]
and
[2]
are enabled,
parameter 1-58 Flying Start Test Pulses Current
and
parameter 1-59 Flying Start Test Pulses
are used to specify conditions for
flying start.
Options
[3]
and
[4]
are set to search for the
motor in the reference direction only, which
allows a faster execution of the motor catch.
[0] Disabled
No function.
[1] Enabled
Enable after coast.
[2] Enabled
Always
Enable at every start.
[3] Enabled
Ref. Dir.
Enable after coast, search in reference direction
only.
[4] Enab.
Always Ref.
Dir.
Enable at every start, search in reference
direction only.
NOTICE
This function is not recommended for hoisting
applications.
For power levels above 55 kW, flux mode must be used
to achieve the best performance.
NOTICE
To obtain the best flying start performance, the
advanced motor data,
parameter 1-30 Stator Resistance
to
parameter 1-35 Main Reactance (Xh)
, must be
correct.
Parameter Descriptions
Programming Guide
MG33MP02
Danfoss A/S © 10/2018 All rights reserved.
59
3
3
Summary of Contents for VLT AutomationDrive FC 302
Page 2: ......