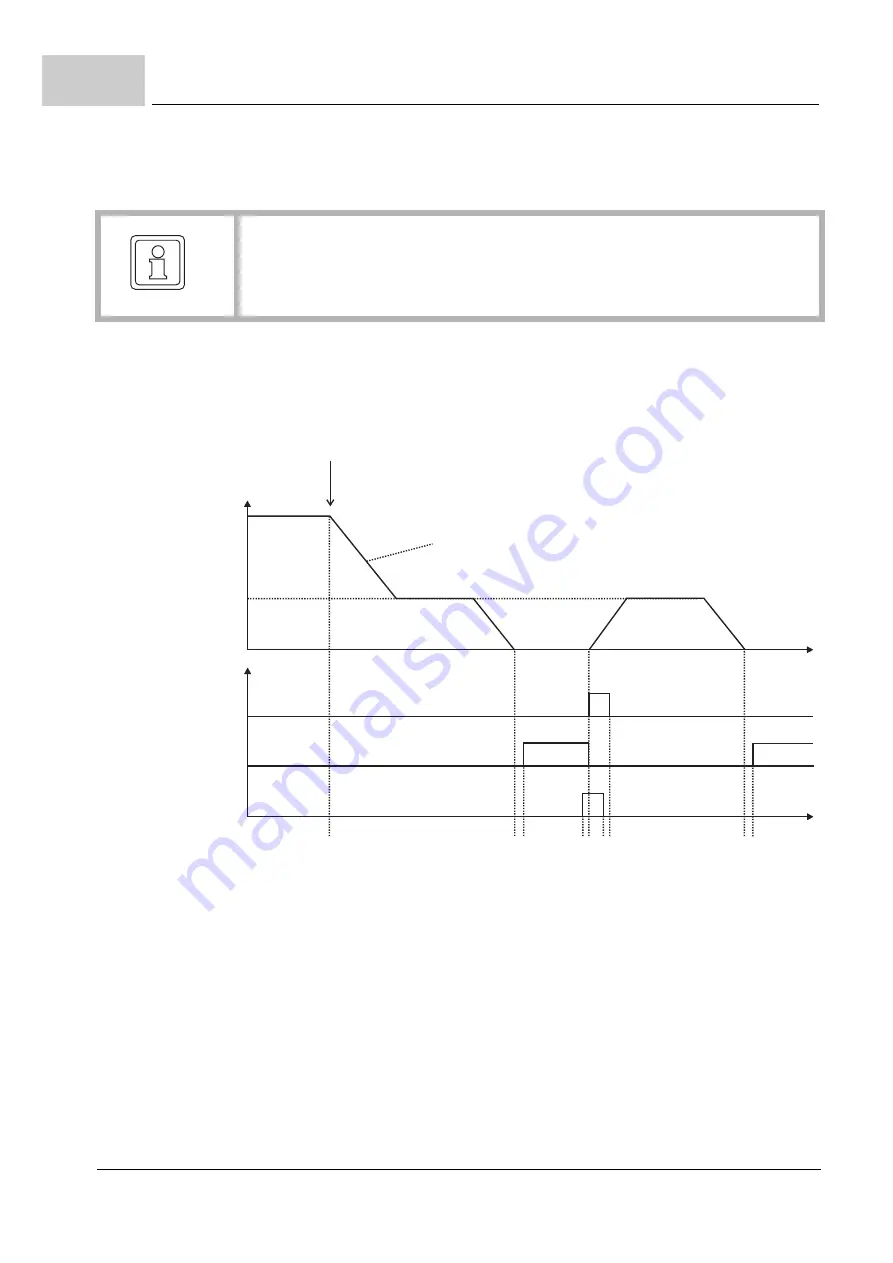
Operating Modes
Parameter manual
b maXX
BM3000
Document no.: 5.12001.07
Baumüller Nürnberg GmbH
610
4.8
deleted. Bit 12 „In position“ in
spindle positioning status is a copy of bit 10 "Set
value reached" in
status word 1.
Operating sequence of a spindle positioning with a subsequent sequential
positioning
Figure 205:
Spindle positioning with sequential positioning
Instant of time 1: Switching to operating mode spindle positioning; deceleration to spin-
dle positioning speed.
Instant of time 2: Position set value has reached active target position
Instant of time 3: Position actual value is in positioning window and positioning window
time is up
Controller sets "set value reached".
Instant of time 4: „Start sequential positioning“ is set.
Instant of time 5: Controller has recognized a start command, resets „set value reached“,
sets the „Start-Command-Acknowledge“ and begins with sequential positioning.
Instant of time 6: „Start sequential positioning“ is deleted.
Instant of time 7: Controller deletes „Start-Command-Acknowledge“.
Instant of time 8: Position set value has reached active target position.
Instant of time 9: The position actual value is in positioning window and positioning win-
dow time is up
Controller sets "set value reached".
NOTE!
Bit 11 of the control word is only used for the sequential positioning. The first posi-
tioning after switching to operating mode spindle positioning is always executed im-
mediately independent of the status of bit 11!
t
n
1
2 3
4 5 67
8 9
Spindle
positioning speed
Status word Bit 12
„Start-Command-
Acknowledge“
Status word Bit 10
„Setpoint reached“
Control word Bit 11
„Start sequential
positioning“
Switched to
operating mode -6 spindle positioning
Slow down with spindle acceleration bipolar
Содержание b maXX BM2500
Страница 740: ...Monitoring Parameter manual b maXX BM3000 Document no 5 12001 07 Baumüller Nürnberg GmbH 740 of 820 4 11 ...
Страница 814: ...Parameter manual b maXX BM3000 Document no 5 12001 07 Baumüller Nürnberg GmbH 814 of 820 ...
Страница 820: ...Parameter manual b maXX BM3000 Document no 5 12001 07 Baumüller Nürnberg GmbH 820 of 820 Notizen ...
Страница 821: ......