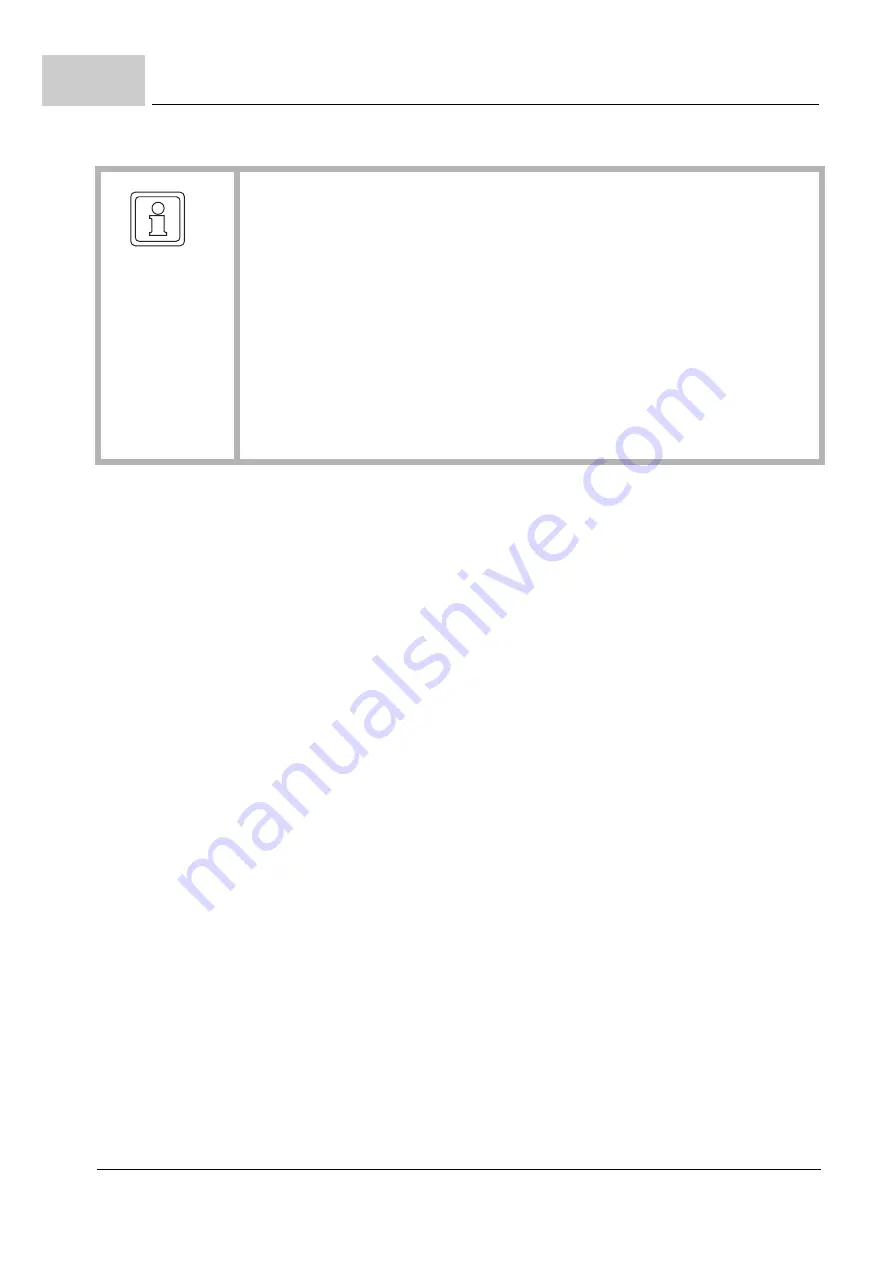
Configuration
Parameter manual
b maXX
BM3000
Document no.: 5.12001.07
Baumüller Nürnberg GmbH
164
4.4
Monitoring of the position actual value
This monitoring is available at Sine-Cosine encoders with digital interface. The absolute
position, which the encoder calculates, is read out at the digital interface (Hiperface,
EnDat, SSI). This value is compared with the position calculated from sine and cosine
traces and is written in parameter
Position monitoring error. If this value ex-
ceeds the set error threshold
, error 428 is initiated:
428 Encoder monitoring: difference between analog and digital position too high
The response time is max. 5 s. Please consider the setting notes for parameter
.
Restrictions:
– Monitoring of Hiperface encoder and EnDat 2.1 is possible from firmware version
1.08.
– Monitoring of SSI encoder is currently not possible.
Field Angle Monitoring on Synchronous Machines
The controller determines the pole wheel direction of the rotor with the aid of the motor
model. This is then compared with the pole wheel direction which is calculated from the
encoder used for motor control. When the monitoring is enabled (i.e. the field angle speed
threshhold
is not equal to 0), if there is an angle error greater than 45° (electri-
cal), Bit 8 of Parameter
is set and the error message
211 Error While Monitoring the Field Angle
is initiated. The pulse enabling is blocked as a result.
Additionally, the field angle monitoring can be switched on and off by setting the field an-
gle speed threshhold (
) as a function of the speed set value. If the speed is less
than the field angle speed threshhold (
), the monitoring remains disabled.
Field angle monitoring only functions for the encoder which is set for motor control.
NOTE!
m
The amplitude monitoring does not monitor for cable breaks and is only in a limited
position to detect any cable breaks that might be present.
It is not guaranteed that an individual break in one of the sin+/sin- or cos+/cos-
lines will be detected by the form of amplitude monitoring implemented.
m
It is not possible, if the machine is stationary, to detect a cable break using the in-
direct method of amplitude monitoring. If might be possible to detect that a cable
break is present using amplitude monitoring, but the machine must first be started
up.
m
The amplitude monitoring and the display in the encoder diagnosis of ProDrive is
only possible up to approximately 18 kHz signal frequency (is equivalent to
n [min
-1
] = 18 kHz * 60 / number of pulses) at a square-wave incremental encod-
er. Above this frequency only the special square-wave incremental encoder mon-
itoring is effective.
Содержание b maXX BM2500
Страница 740: ...Monitoring Parameter manual b maXX BM3000 Document no 5 12001 07 Baumüller Nürnberg GmbH 740 of 820 4 11 ...
Страница 814: ...Parameter manual b maXX BM3000 Document no 5 12001 07 Baumüller Nürnberg GmbH 814 of 820 ...
Страница 820: ...Parameter manual b maXX BM3000 Document no 5 12001 07 Baumüller Nürnberg GmbH 820 of 820 Notizen ...
Страница 821: ......