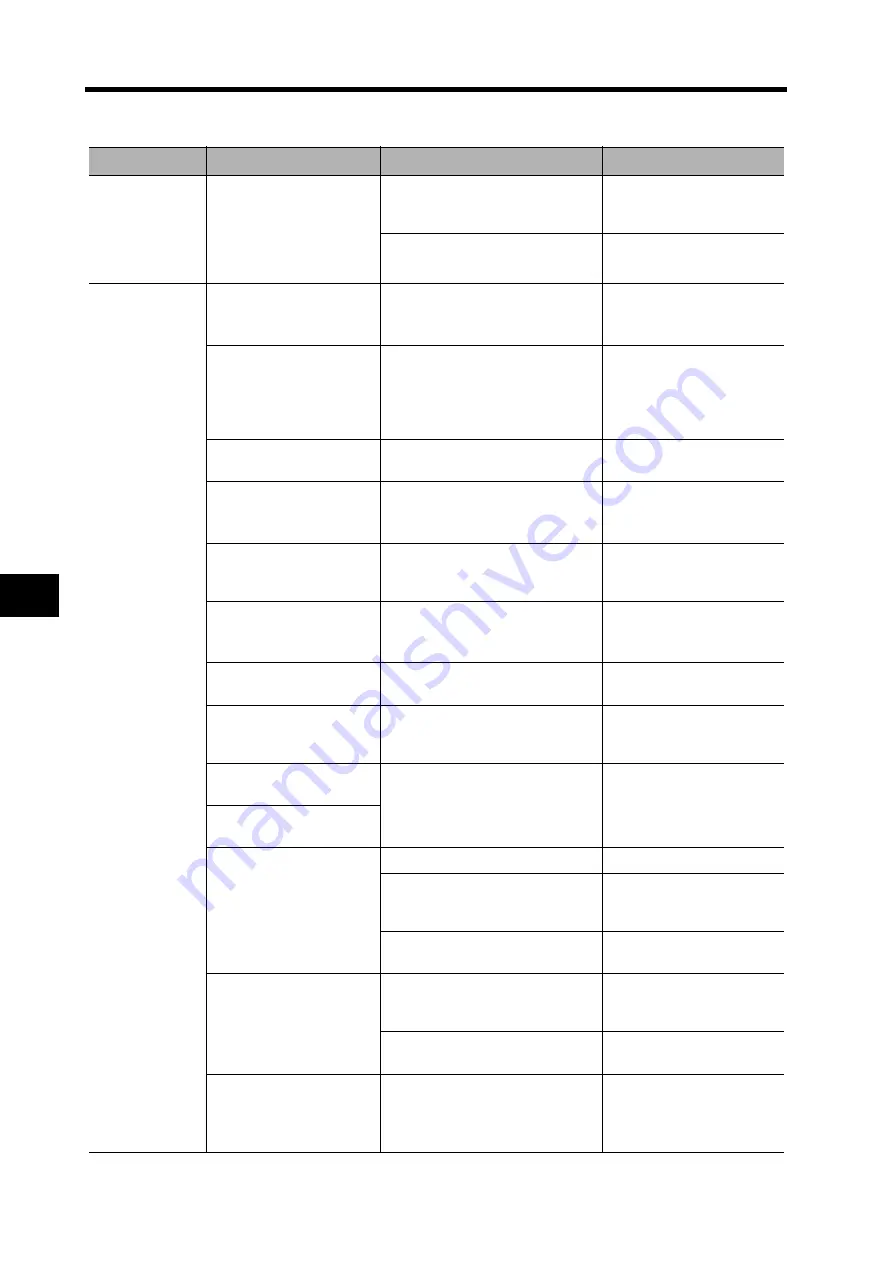
8-15
8-3 Troubleshooting
8
Troubleshooting
Error Diagnosis Using the Operating Status
Symptom
Probable cause
Items to check
Countermeasures
The power LED
indicator (PWR)
does not light
when the power
supply is turned
ON.
The power supply cable is
wired incorrectly.
Check whether the power supply
input is within the allowed voltage
range.
Supply the correct voltage.
Check whether the power supply
input is wired correctly.
Correct the wiring.
The Servomotor
does not rotate
even if
commands are
input from the
Controller.
(Continued on
next page.)
The RUN Command Input
is OFF.
In monitor mode, check whether the
RUN signal is ON or OFF.
•
Turn ON the RUN
Command Input.
•
Correct the wiring.
The Forward Drive Prohibit
Input (POT) and Reverse
Drive Prohibit Input (NOT)
are OFF.
In monitor mode, check whether the
POT input and NOT input are ON or
OFF.
•
Turn ON the POT and
NOT inputs.
•
If the POT and NOT
inputs are not used,
disabled them.
The control mode is not
correct.
Check the Control Mode Selection
(Pn02).
Set the control mode to
match the command type.
The Deviation Counter
Reset Input (ECRST) is
ON.
In monitor mode, check whether the
ECRST Input is ON or OFF.
•
Turn the ECRST Input
OFF.
•
Correct the wiring.
The Command Pulse Mode
(Pn42) is incorrect.
Check the Controller’s command
pulse type and the Servo Drive’s
command pulse type.
Set the Servo Drive’s pulse
type to match the Control-
ler’s command pulse type.
The Zero Speed Designa-
tion Input (VZERO) is OFF.
In monitor mode, check whether the
VZERO Input is ON or OFF.
•
Turn ON the VZERO
Input.
•
Correct the wiring.
The internally set speeds
are not set.
Check the settings for Pn53 to
Pn56 or Pn74 to Pn77.
Set the desired speeds.
No. 1 Torque Limit (Pn5E)
or No. 2 Torque Limit
(Pn5F) is set to 0.
Check the setting for Pn5E or
Pn5F.
Return the setting to the
default.
The Servomotor Power
Cable is wired incorrectly.
Check the wiring.
Correct the wiring.
The Encoder Cable is wired
incorrectly.
The Control I/O Connector
CN1) is wired incorrectly.
Check the command pulse’s wiring. Correct the wiring.
Check the command pulse type.
Set the Servo Drive’s pulse
type to match the Control-
ler’s command pulse type.
Check the command pulse’s
voltage.
Connect a resistor that
matches the voltage.
The power supply is not
ON.
Check whether the power supply is
ON and check the PWR LED
indicator.
Turn ON the power supply.
Check the voltage across the power
supply terminals.
Wire the power supply’s ON
circuit correctly.
The speed command is
disabled.
Check if the speed command
procedure is correct.
•
Correctly set the external
analog command.
•
Correctly set the internal
speed.
Summary of Contents for R88D-GT series
Page 20: ...18 Table of Contents ...
Page 234: ...3 133 3 8 Reactor Specifications 3 Specifications ...
Page 448: ...7 37 7 5 Manual Tuning 7 Adjustment Functions ...
Page 474: ...8 25 8 5 Periodic Maintenance 8 Troubleshooting ...
Page 475: ...Chapter 9 Appendix 9 1 Connection Examples 9 1 9 2 Parameter Tables 9 11 ...
Page 509: ......