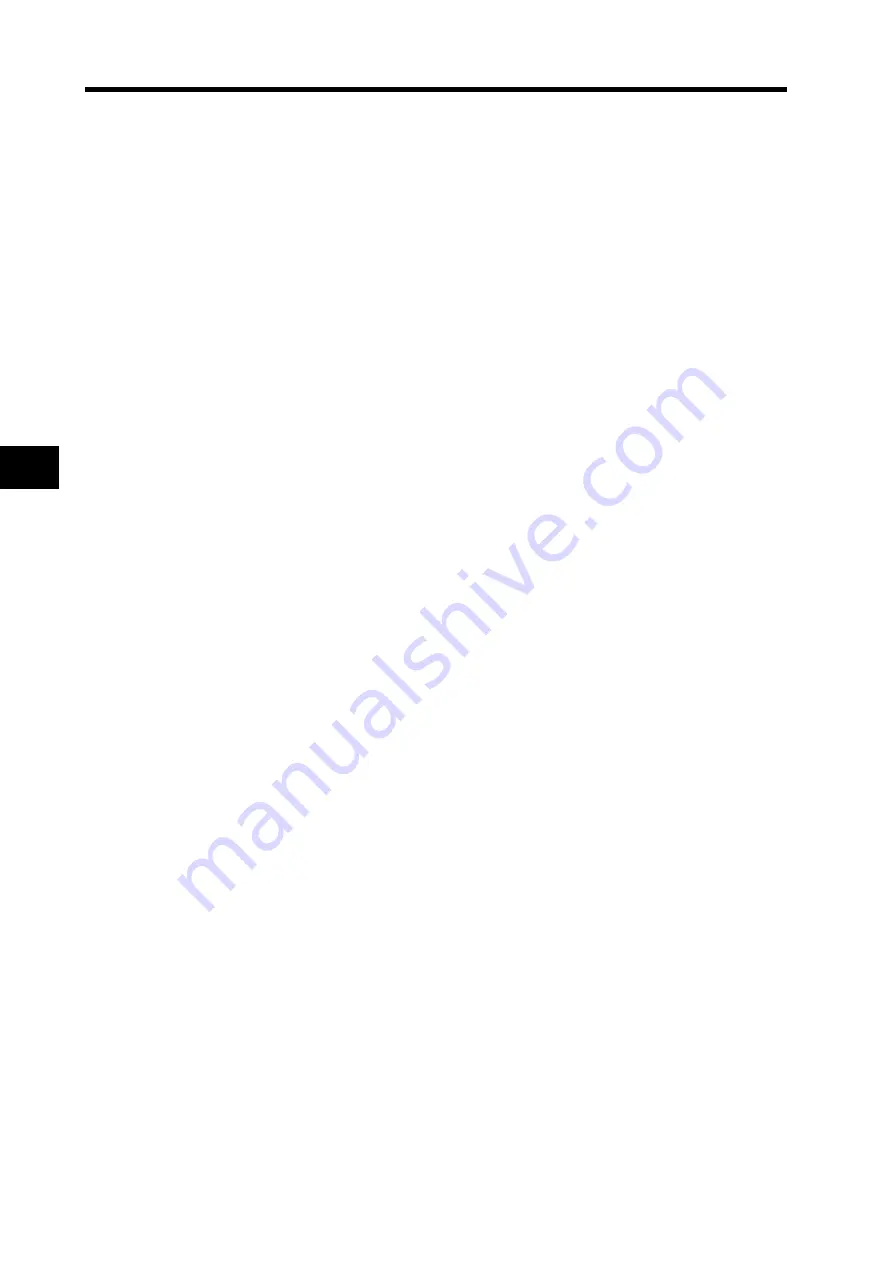
6-29
6-5 Trial Operation
6
Opera
tion
Trial Operation in Speed Control Mode
1. Connect connector CN1.
2. Input power (12 to 24 VDC) for the control signals (+24VIN, COM).
3. Turn ON the power supply to the Servo Drive.
4. Confirm that the parameters are set to the standard settings.
5. Connect the RUN Command Input (RUN: CN1 pin 29) to COM (CN1 pin 41). Servo ON
status will be entered and the Servomotor will be activated.
6. Close the Zero-speed Designation Input (VZERO) and gradually increase the DC
voltage across the Speed Command Input (REF: CN1 pin 14) and AGND (CN1 pin 15)
from 0 V. Check to see if the Servomotor rotates.
7. Check the Servomotor rotation speed in Monitor Mode.
Check to see if the Servomotor is rotating at the specified speed and to see if the Servomotor stops
when the command pulses are stopped. Use the following parameters to change the Servomotor
rotation speed or direction.
• Pn50: Speed Command Scale
• Pn51: Command Speed Rotation Direction Switch
Trial Operation in Torque Control Mode
1. Connect connector CN1.
2. Input power (12 to 24 VDC) for the control signals (+24VIN, COM).
3. Turn ON the power supply to the Servo Drive.
4. Confirm that the parameters are set to the standard settings.
5. Set a low speed in the No. 4 Internally Set Speed (Pn56).
6. Connect the RUN Command Input (RUN: CN1 pin 29) to COM (CN1 pin 41). Servo ON
status will be entered and the Servomotor will be activated.
7. Apply a positive or negative DC voltage across the Torque Command Input (TREF1:
CN1 pin 14) and AGND (CN1 pin 15). Check to see if the Servomotor rotates
according to the direction (forward/reverse) set in Pn56.
Use the following parameters to change the amount of the torque, direction of the torque, or speed
limit for the command voltage.
• Pn56: No. 4 Internally Set Speed (default value: 50 r/min)
• Pn5C: Torque Command Scale
• Pn5D: Torque Output Direction Switch
Summary of Contents for R88D-GT series
Page 20: ...18 Table of Contents ...
Page 234: ...3 133 3 8 Reactor Specifications 3 Specifications ...
Page 448: ...7 37 7 5 Manual Tuning 7 Adjustment Functions ...
Page 474: ...8 25 8 5 Periodic Maintenance 8 Troubleshooting ...
Page 475: ...Chapter 9 Appendix 9 1 Connection Examples 9 1 9 2 Parameter Tables 9 11 ...
Page 509: ......