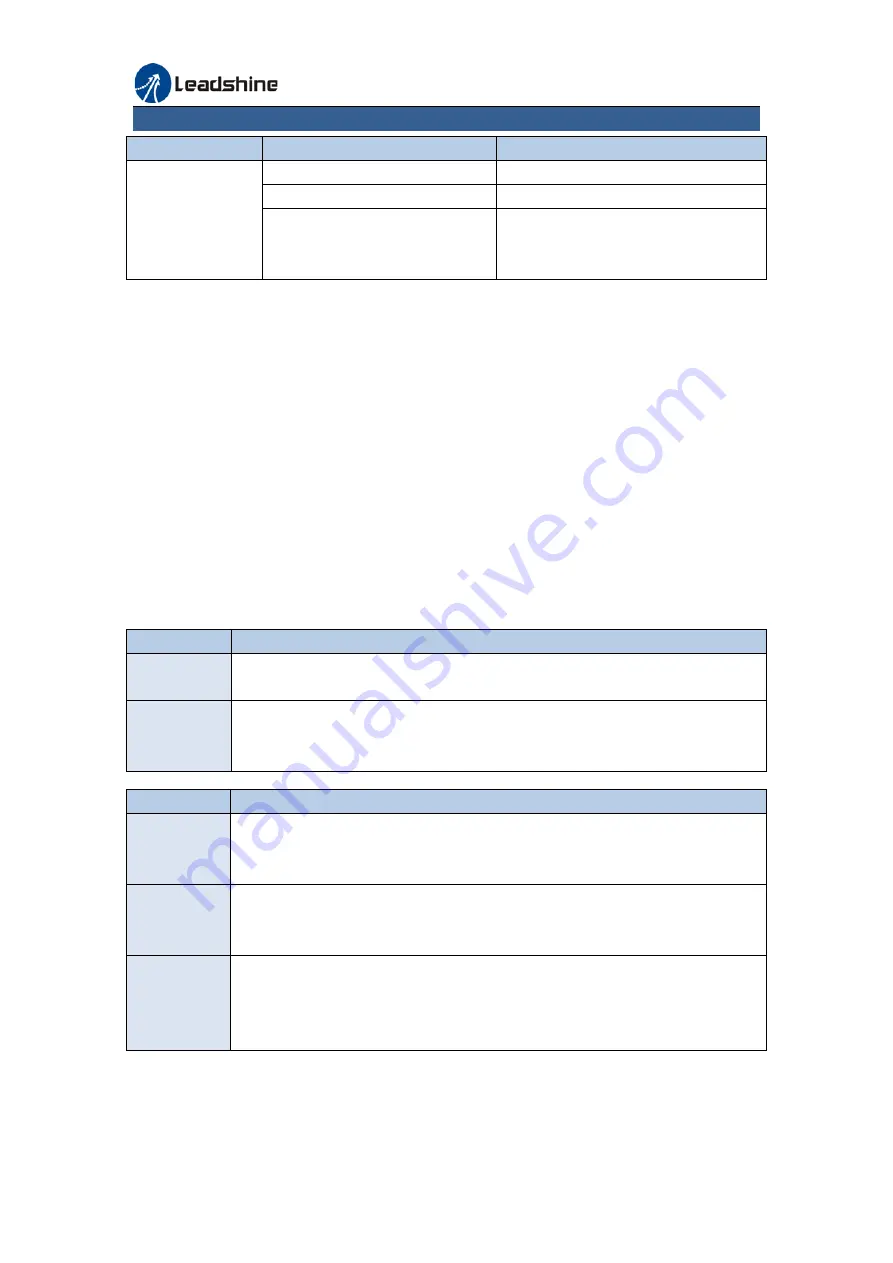
User manual of EL8-EC***F AC Servo
232
Common issues
Error
Cause
Solution
Inertia ratio
identification
failure
Loose load connection
Check for mechanical failure
Measuring distance is too short
Increase measuring distance
Belt load
Please pre-set an inertia ratio when
using a belt to prevent jolt due to low
inertia.
6.3 Easy Tuning
6.3.1 Single Parameter Tuning
Set a mechanical stiffness level and the driver will automatically tune the parameters
accordingly, including inertia measuring and vibration suppression to fulfill responsiveness and
stability needs. At same time, more advanced functions can be applied, for example:
Command pulse filter, low frequency vibration suppression, etc.
Recommended for applications where inertia changes is minute. Single parameter tuning is
more complicated to set up compared to one-click tuning. Use single parameter tuning when
one-click tuning doesn’t fulfill the needs.
Recommended application scenarios
Control
mode
Suitable in position mode or EtherCAT mode (Not applicable in other modes)
Others
Servo ON (SRV-ON) status
Set suitable position/torque limit so that motor can run normally
Use trial run or any external controller to make sure no clash of axes
Factors affecting single parameter tuning
Load inertia
External load smaller or 30 times larger than rotor inertia
Inertia measuring might fail upon changes in load inertia
Load torque changes drastically
Load
Mechanical stiffness is too low
Existence of gear backlash or any other non-linear factors
Complicated mechanical load structure
Motion
Low speed, no more than 300[r/min].
Acceleration/deceleration time too long, more than = 600ms
Speed > 300r/min, acceleration/deceleration time < 600ms but travelling
time duration < 50ms.