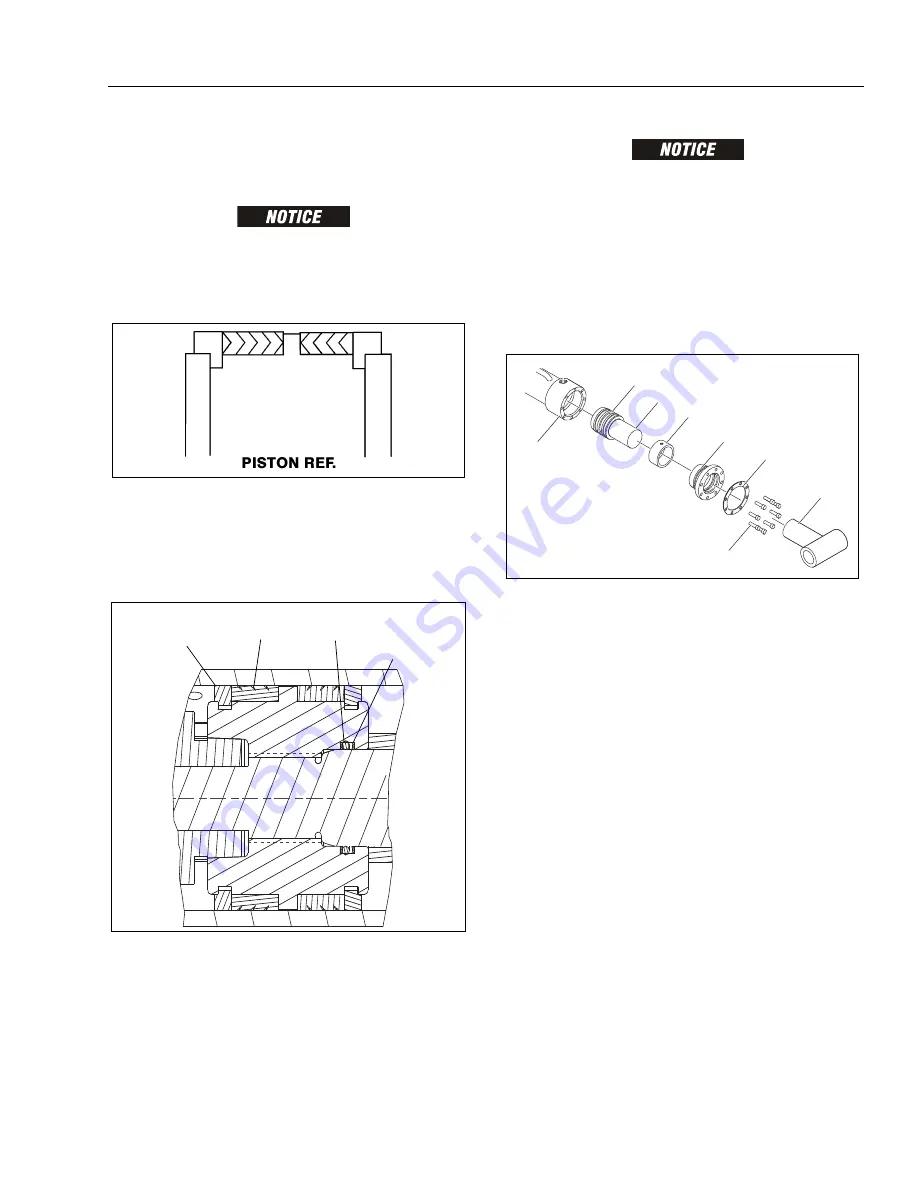
SECTION 5 - BASIC HYDRAULIC INFOR
M
ATION AND SCHE
M
ATICS
3121160
5-43
13.
Rotate the capscrews evenly and progressively in rota-
tion to 9 ft. lbs. (12.2 Nm).
14.
Remove the cylinder rod from the holding fixture.
WHEN INSTALLING HYDROLOCK PISTON SEALS, ENSURE SEALS ARE
INSTALLED PROPERLY. REFER TO HYDROLOCK PISTON SEAL INSTALLATION
FOR CORRECT SEAL ORIENTATION. IMPROPER SEAL INSTALLATION COULD
RESULT IN CYLINDER LEAKAGE AND IMPROPER CYLINDER OPERATION.
15.
Place new hydrolock seals and guidelock rings in the
outer piston diameter groove. (A tube, with I.D. slightly
larger than the O.D. of the piston is recommended to
install the solid seal).
16.
Position the cylinder barrel in a suitable holding fixture.
EXTREME CARE SHOULD BE TAKEN WHEN INSTALLING THE CYLINDER ROD,
HEAD, AND PISTON. AVOID PULLING THE ROD OFF-CENTER, WHICH COULD
CAUSE DAMAGE TO THE PISTON AND CYLINDER BARREL SURFACES.
17.
With barrel clamped securely, and while adequately sup-
porting the rod, insert the piston end into the barrel cyl-
inder. Ensure that the piston loading hydrolock seals and
guidelock rings are not damaged or dislodged.
18.
Continue pushing the rod into the barrel until the cylin-
der head gland can be inserted into the barrel cylinder.
19.
Apply JLG Threadlocker (P/N 0100011) to the socket
head bolts and secure the cylinder head gland using the
washer ring and bolts. Torque bolts to 35 ft. lbs.
(47.5 Nm).
20.
After the cylinder has been reassembled, the rod should
be pushed all the way in (fully retracted) prior to the
reinstallation of any holding valve or valves.
21.
Install the counterbalance valves and fittings in the rod
port block, using new o-rings as applicable. Torque to
counterbalance valves as shown in Figure 5-79., Slave
Cylinder.
Figure 5-88. Hydrolock Piston Seal Installation
Figure 5-89. Piston Seal Kit Installation
HYDROLOCK
SEAL
GUIDELOCK
RING
O-RING
BACKUP
RING
BARREL
PISTON
ROD
HEAD
SPACER
WASHER RING
CA
1
SCREW
ROD
Figure 5-90. Rod Assembly Installation
Summary of Contents for 740AJ
Page 2: ......
Page 55: ...SECTION 3 CHASSIS TURNTABLE 3121160 3 3 This page left blank intentionally...
Page 116: ...SECTION 3 CHASSIS TURNTABLE 3 64 3121160 Figure 3 44 Swing Hub Prior to SN 0300074383...
Page 203: ...SECTION 3 CHASSIS TURNTABLE 3121160 3 151 Figure 3 77 EFI Component Location...
Page 206: ...SECTION 3 CHASSIS TURNTABLE 3 154 3121160 Figure 3 78 ECM EPM Identification ECM EPM...
Page 224: ...SECTION 3 CHASSIS TURNTABLE 3 172 3121160 Figure 3 83 Deutz EMR 2 Troubleshooting Flow Chart...
Page 228: ...SECTION 3 CHASSIS TURNTABLE 3 176 3121160 Figure 3 87 EMR 2 Engine Plug Pin Identification...
Page 229: ...SECTION 3 CHASSIS TURNTABLE 3121160 3 177 Figure 3 88 EMR 2 Vehicle Plug Pin Identification...
Page 230: ...SECTION 3 CHASSIS TURNTABLE 3 178 3121160 Figure 3 89 EMR2 Fault Codes Sheet 1 of 5...
Page 231: ...SECTION 3 CHASSIS TURNTABLE 3121160 3 179 Figure 3 90 EMR2 Fault Codes Sheet 2 of 5...
Page 232: ...SECTION 3 CHASSIS TURNTABLE 3 180 3121160 Figure 3 91 EMR2 Fault Codes Sheet 3 of 5...
Page 233: ...SECTION 3 CHASSIS TURNTABLE 3121160 3 181 Figure 3 92 EMR2 Fault Codes Sheet 4 of 5...
Page 234: ...SECTION 3 CHASSIS TURNTABLE 3 182 3121160 Figure 3 93 EMR2 Fault Codes Sheet 5 of 5...
Page 303: ...SECTION 4 BOOM PLATFORM 3121160 4 31 Figure 4 20 Rotator Assembly HELAC...
Page 460: ...SECTION 5 BASIC HYDRAULIC INFORMATION AND SCHEMATICS 5 116 3121160 NOTES...
Page 467: ...SECTION 6 JLG CONTROL SYSTEM 3121160 6 7 Figure 6 2 ADE Block Diagram...
Page 534: ...SECTION 6 JLG CONTROL SYSTEM 6 74 3121160 NOTES...
Page 580: ...SECTION 7 BASIC ELECTRICAL INFORMATION SCHEMATICS 7 46 3121160 NOTES...
Page 581: ......