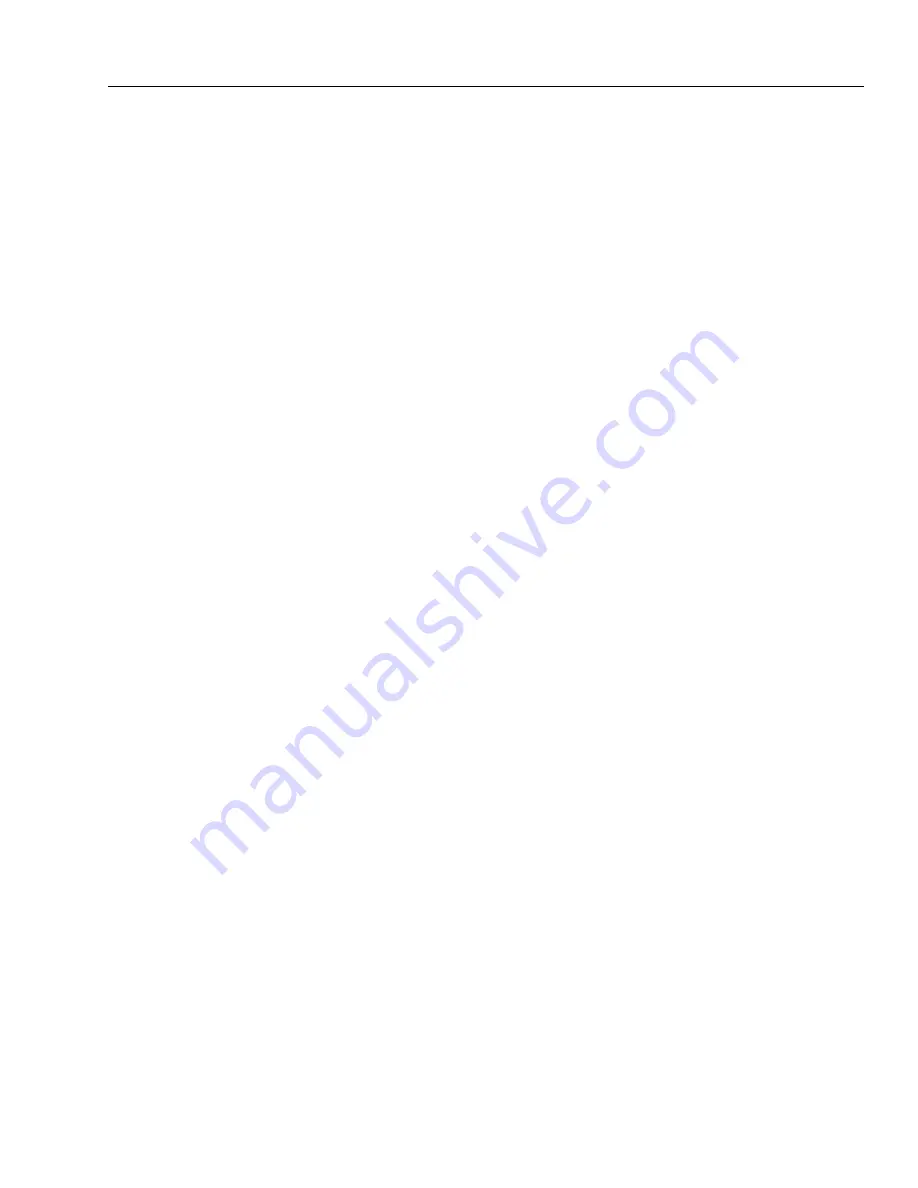
SECTION 3 - CHASSIS & TURNTABLE
3121160
3-73
3.15 SWING DRIVE BRAKE (PRIOR TO SN
0300134352)
Disassembly
1.
Supporting brake: remove the six socket head cap-
screws and washers (13 & 14) in equal increments to
ensure the spring pressure within the brake is reduced
gradually and evenly.
If a press is available, the cylinder housing (8) can be
restrained while removing the six capscrews and wash-
ers (13 & 14).
The brake assembly can now be fully dismantled and
the parts examined.
2.
Remove cylinder housing (8) and piston (9) subassembly
and dismantle if required, removing O-ring seals (15 &
17) and backing rings (16 & 18) as necessary.
3.
Remove gasket (7) from housing (2).
4.
Remove friction plates (3 & 6) and pressure plate (4).
5.
Remove two dowel pins (19).
6.
Remove springs (22 & 23).
7.
Should it be necessary to replace ball bearing (10) or
shaft seal (12), reverse remainder of brake subassembly,
supporting on face C of housing (2).
8.
Remove internal retaining ring (11).
9.
Using arbor press or similar to break Loctite seal, remove
brake shaft (1) from housing (2) and lay aside.
10.
Reverse housing (2) and press out ball bearing (10).
Shaft seal (12) can also be removed if necessary.
Inspection
1.
Inspect friction plates (3 & 6) and friction surface on
pressure plate (4) for wear or damage.
2.
Examine friction plates (3) and brake shaft (1) for wear or
damage to the splines.
3.
Examine input and output splines of brake shaft (1) for
wear or damage.
4.
Examine compression springs (22 & 23) for damage or
fatigue.
5.
Check ball bearing (10) for axial float or wear.
6.
Examine o-ring seals (15 & 17) and backing rings (16 &
18) for damage.
Assembly
1.
Lightly lubricate rotary shaft seal (12) and assemble to
housing (2) taking care not to damage seal lip.
2.
Apply ring of Loctite 641 or equivalent adhesive to full
circumference of housing (2) bearing recess adjacent to
shoulder.
Apply complete coverage of Loctite 641 to outside
diameter of bearing (10) and assemble fully In housing
(2), retaining with internal retaining ring (11). Remove
excess adhesive with a clean cloth.
Press shaft (1) through bearing (10), ensuring bearing
inner ring Is adequately supported.
3.
Assemble correct quantity of springs (22 & 23) in orien-
tation required.
4.
Lubricate o-ring seals (15 & 17) with Molykote 55M (or
equivalent) silicon grease and assemble together with
backing rings (16 & 18) to piston (9). To ensure correct
brake operation. It is important that the backing rings
are assembled opposite to the pressurized side of pis-
ton.
5.
Correctly orientate piston (9) aligning spaces with the
two dowel pin holes and, assemble into cylinder hous-
ing (8) taking care not to damage seals and carefully lay
aside.
6.
Locate 2-off pins (19) in housing (2) followed by pressure
plate (4) and friction plates i.e. an inner (3) followed by
an outer (6) in correct sequence.
7.
Position gasket (7) in correct orientation.
8.
Align two holes in cylinder with dowel pins (19) and
assemble piston & cylinder sub-assembly to remainder
of brake securing with 6 capscrews and washers (13 &
14). Torque to 55 ft. lbs. (75 Nm).
NOTE:
The use of a suitable press (hydraulic or arbor) pressing
down on cylinder end face B will ease assembly of the cap-
screws (13).
Summary of Contents for 740AJ
Page 2: ......
Page 55: ...SECTION 3 CHASSIS TURNTABLE 3121160 3 3 This page left blank intentionally...
Page 116: ...SECTION 3 CHASSIS TURNTABLE 3 64 3121160 Figure 3 44 Swing Hub Prior to SN 0300074383...
Page 203: ...SECTION 3 CHASSIS TURNTABLE 3121160 3 151 Figure 3 77 EFI Component Location...
Page 206: ...SECTION 3 CHASSIS TURNTABLE 3 154 3121160 Figure 3 78 ECM EPM Identification ECM EPM...
Page 224: ...SECTION 3 CHASSIS TURNTABLE 3 172 3121160 Figure 3 83 Deutz EMR 2 Troubleshooting Flow Chart...
Page 228: ...SECTION 3 CHASSIS TURNTABLE 3 176 3121160 Figure 3 87 EMR 2 Engine Plug Pin Identification...
Page 229: ...SECTION 3 CHASSIS TURNTABLE 3121160 3 177 Figure 3 88 EMR 2 Vehicle Plug Pin Identification...
Page 230: ...SECTION 3 CHASSIS TURNTABLE 3 178 3121160 Figure 3 89 EMR2 Fault Codes Sheet 1 of 5...
Page 231: ...SECTION 3 CHASSIS TURNTABLE 3121160 3 179 Figure 3 90 EMR2 Fault Codes Sheet 2 of 5...
Page 232: ...SECTION 3 CHASSIS TURNTABLE 3 180 3121160 Figure 3 91 EMR2 Fault Codes Sheet 3 of 5...
Page 233: ...SECTION 3 CHASSIS TURNTABLE 3121160 3 181 Figure 3 92 EMR2 Fault Codes Sheet 4 of 5...
Page 234: ...SECTION 3 CHASSIS TURNTABLE 3 182 3121160 Figure 3 93 EMR2 Fault Codes Sheet 5 of 5...
Page 303: ...SECTION 4 BOOM PLATFORM 3121160 4 31 Figure 4 20 Rotator Assembly HELAC...
Page 460: ...SECTION 5 BASIC HYDRAULIC INFORMATION AND SCHEMATICS 5 116 3121160 NOTES...
Page 467: ...SECTION 6 JLG CONTROL SYSTEM 3121160 6 7 Figure 6 2 ADE Block Diagram...
Page 534: ...SECTION 6 JLG CONTROL SYSTEM 6 74 3121160 NOTES...
Page 580: ...SECTION 7 BASIC ELECTRICAL INFORMATION SCHEMATICS 7 46 3121160 NOTES...
Page 581: ......