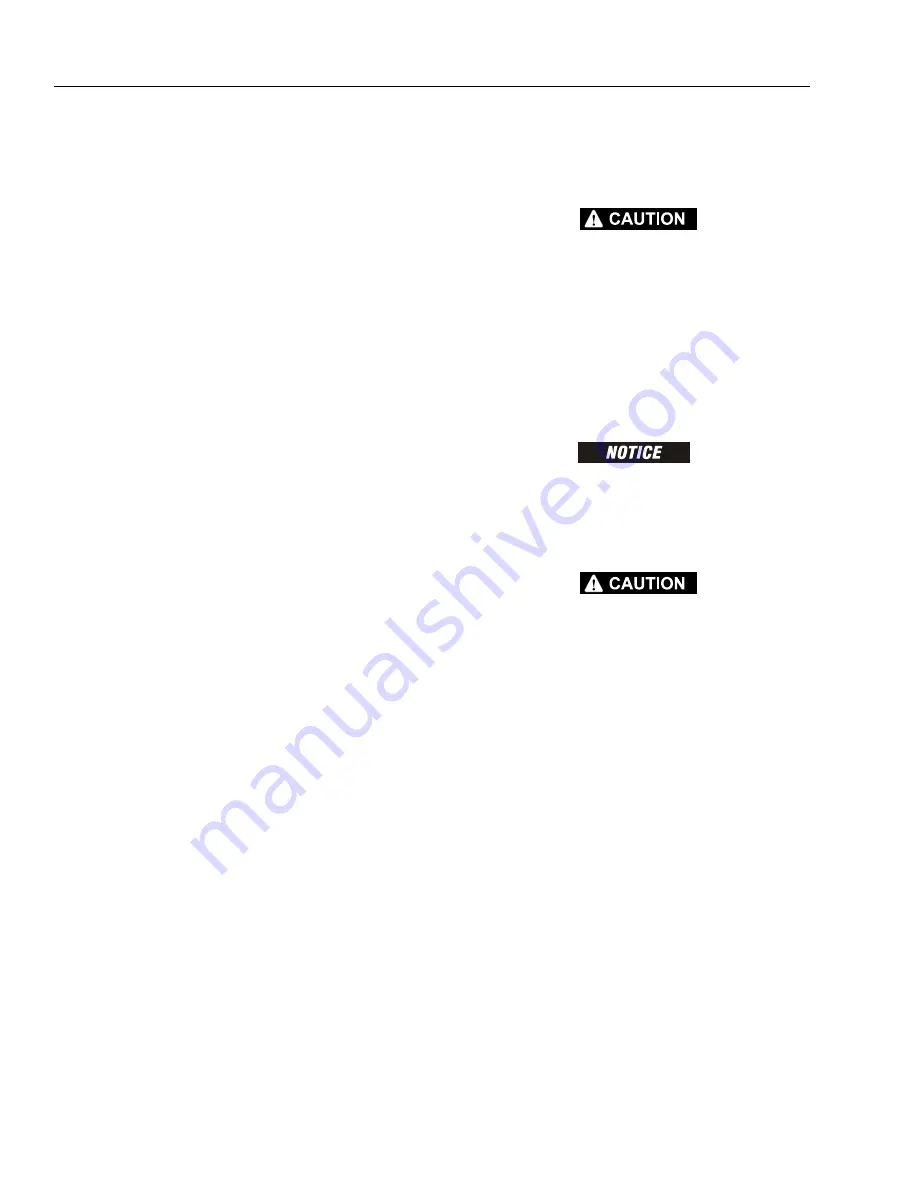
SECTION 3 - CHASSIS & TURNTABLE
3-190
3121160
Fuel Filter
After the fuel is drawn into the fuel pump, the fuel flows
through the gasoline fuel filter. The fuel filter will trap small
particles as the fuel passes through the filter to remove debris
and prevents the fuel pressure and temperature manifold and
fuel injectors from becoming damaged. Maintenance of the
fuel filter is required as indicated in Section 1.
Fuel Injector Rail
Fuel flows from the fuel pressure and temperature manifold
assembly to the fuel rails where the fuel is delivered to the fuel
injectors. The fuel rail also contains a Schrader valve which is
utilized to test the regulated pressure of the fuel system.
Fuel Injector
The fuel supply is maintained on the top of the injector from
the injector rail. The injector is fed a "pulse" signal through the
wire harness which causes the injector to open. During regular
operating conditions the ECM controls the opening and dura-
tion of opening of the injector. During lower RPM operation
the injector signals or "pulses" are less frequent then when the
engine is operating at higher RPMs. The engine has been cali-
brated to deliver the precise amount of fuel for optimum per-
formance and emission control.
3.34 GM ENGINE FUEL SYSTEM REPAIR
Propane Fuel System Pressure Relief
THE PROPANE FUEL SYSTEM OPERATES AT PRESSURES UP TO 312 PSI (21.5
BAR). TO MINIMIZE THE RISK OF FIRE AND PERSONAL INJURY, RELIEVE THE
PROPANE FUEL SYSTEM PRESSURE (WHERE APPLICABLE) BEFORE SERVICING
THE PROPANE FUEL SYSTEM COMPONENTS.
To relieve propane fuel system pressure:
1.
Close the manual shut-off valve on the propane fuel
tank.
2.
Start and run the vehicle until the engine stalls.
3.
Turn the ignition switch OFF.
RESIDUAL VAPOR PRESSURE WILL BE PRESENT IN THE FUEL SYSTEM. ENSURE
THE WORK AREA IS WELL VENTILATED BEFORE DISCONNECTING ANY FUEL
LINE.
Propane Fuel System Leak Test
NEVER USE AN OPEN FLAME OF ANY TYPE TO CHECK FOR PROPANE FUEL SYS-
TEM LEAKS.
Always inspect the propane fuel system for leaks after per-
forming service. Check for leaks at the fittings of the serviced
or replaced component. Use a commercially available liquid
leak detector or an electronic leak detector. When using both
methods, use the electronic leak detector first to avoid con-
tamination by the liquid leak detector.
Summary of Contents for 740AJ
Page 2: ......
Page 55: ...SECTION 3 CHASSIS TURNTABLE 3121160 3 3 This page left blank intentionally...
Page 116: ...SECTION 3 CHASSIS TURNTABLE 3 64 3121160 Figure 3 44 Swing Hub Prior to SN 0300074383...
Page 203: ...SECTION 3 CHASSIS TURNTABLE 3121160 3 151 Figure 3 77 EFI Component Location...
Page 206: ...SECTION 3 CHASSIS TURNTABLE 3 154 3121160 Figure 3 78 ECM EPM Identification ECM EPM...
Page 224: ...SECTION 3 CHASSIS TURNTABLE 3 172 3121160 Figure 3 83 Deutz EMR 2 Troubleshooting Flow Chart...
Page 228: ...SECTION 3 CHASSIS TURNTABLE 3 176 3121160 Figure 3 87 EMR 2 Engine Plug Pin Identification...
Page 229: ...SECTION 3 CHASSIS TURNTABLE 3121160 3 177 Figure 3 88 EMR 2 Vehicle Plug Pin Identification...
Page 230: ...SECTION 3 CHASSIS TURNTABLE 3 178 3121160 Figure 3 89 EMR2 Fault Codes Sheet 1 of 5...
Page 231: ...SECTION 3 CHASSIS TURNTABLE 3121160 3 179 Figure 3 90 EMR2 Fault Codes Sheet 2 of 5...
Page 232: ...SECTION 3 CHASSIS TURNTABLE 3 180 3121160 Figure 3 91 EMR2 Fault Codes Sheet 3 of 5...
Page 233: ...SECTION 3 CHASSIS TURNTABLE 3121160 3 181 Figure 3 92 EMR2 Fault Codes Sheet 4 of 5...
Page 234: ...SECTION 3 CHASSIS TURNTABLE 3 182 3121160 Figure 3 93 EMR2 Fault Codes Sheet 5 of 5...
Page 303: ...SECTION 4 BOOM PLATFORM 3121160 4 31 Figure 4 20 Rotator Assembly HELAC...
Page 460: ...SECTION 5 BASIC HYDRAULIC INFORMATION AND SCHEMATICS 5 116 3121160 NOTES...
Page 467: ...SECTION 6 JLG CONTROL SYSTEM 3121160 6 7 Figure 6 2 ADE Block Diagram...
Page 534: ...SECTION 6 JLG CONTROL SYSTEM 6 74 3121160 NOTES...
Page 580: ...SECTION 7 BASIC ELECTRICAL INFORMATION SCHEMATICS 7 46 3121160 NOTES...
Page 581: ......