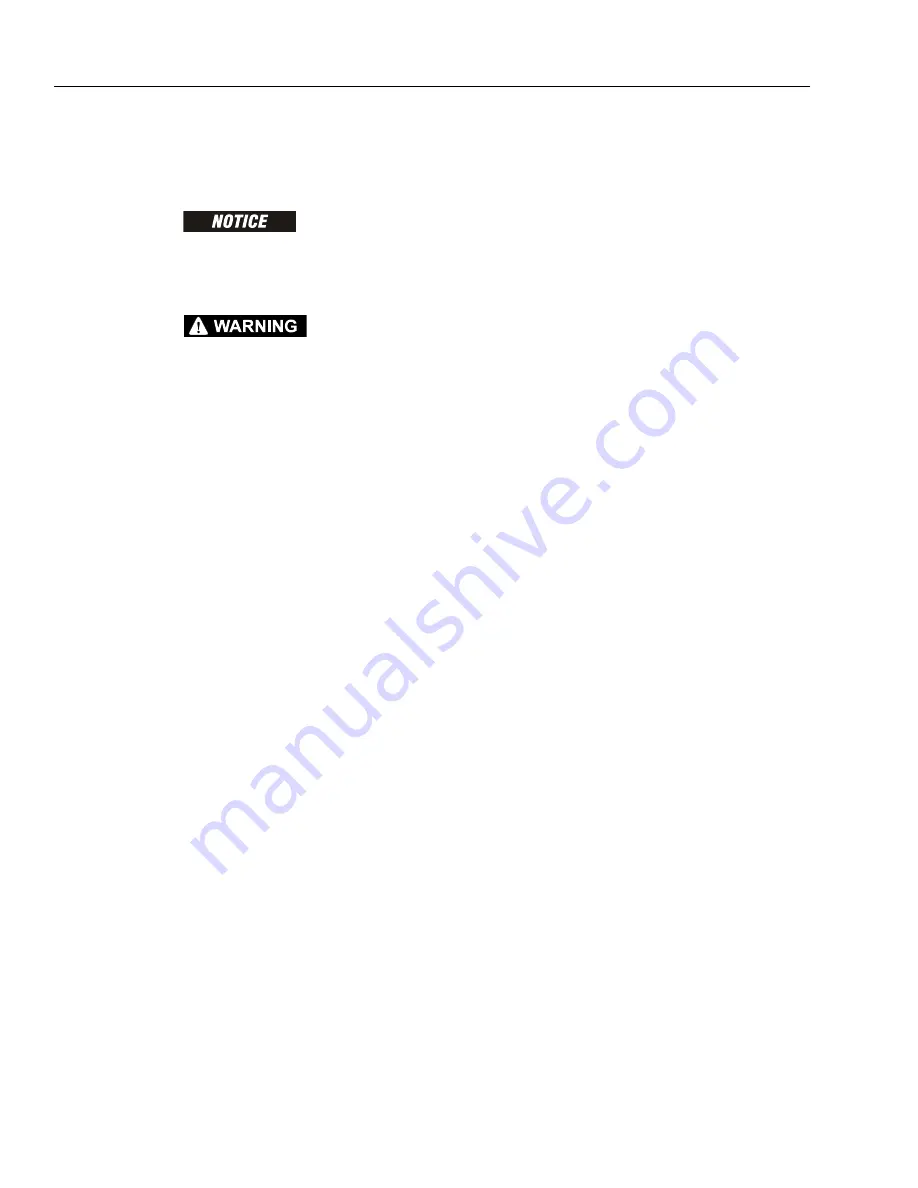
SECTION 5 - BASIC HYDRAULIC INFOR
M
ATION AND SCHE
M
ATICS
5-6
3121160
Cylinders With Dual Counterbalance Valves
Articulating Jib Boom Lift, Slave Level, Tower Lift, Upright level
and Main Telescope.
OPERATE ALL FUNCTIONS FROM GROUND CONTROL STATION ONLY.
1.
Using all applicable safety precautions, activate hydrau-
lic system.
IF WORKING ON THE TOWER BOOM LIFT C YLINDER, RAISE TOWER BOOM
HALFWAY, FULLY ELEVATE MAIN BOOM WITH TELESCOPE CYLINDER FULLY
RETRACTED AND ATTACH AN OVERHEAD CRANE TO THE UPRIGHT FOR SUP-
PORT, LEAVING APPROXIMATELY 1 INCH (2.54 CM) OF SLACK IN CHAIN OR
SLING FOR TEST PURPOSES. IF WORKING ON THE UPRIGHT LEVEL, RAISE THE
TOWER BOOM HALFWAY, THEN RAISE MAIN BOOM TO HORIZONTAL, AND SUP-
PORT WITH A CRANE OR SUITABLE LIFTING DEVICE, APPROXIMATELY 1 INCH
(2.54 CM) BELOW MAIN BOOM. IF WORKING ON THE PLATFORM LEVEL CYLIN-
DER, STROKE PLATFORM LEVEL CYLINDER FORWARD UNTIL PLATFORM SITS
AT A 45 DEGREES ANGLE.
2.
Shut down hydraulic system and allow machine to sit for
10-15 minutes. If machine is equipped with bang-bang
or proportional control valves, turn IGNITION SWITCH to
ON, move control switch or lever for applicable cylinder
in each direction, then turn IGNITION SWITCH to OFF. If
machine is equipped with hydraulic control valves,
move control lever for applicable cylinder in each direc-
tion. This is done to relieve pressure in the hydraulic
lines. Carefully remove hydraulic hoses from appropriate
cylinder port block.
3.
There will be initial weeping of hydraulic fluid, which
can be caught in a suitable container. After the initial
discharge, there should be no further leakage from the
ports. If leakage continues at a rate of 6-8 drops per min-
ute or more, the counterbalance valve is defective and
must be replaced.
4.
To check piston seals, carefully remove the counterbal-
ance valve from the retract port. After initial discharge,
there should be no further leakage from the ports. If
leakage occurs at a rate of 6-8 drops per minute or more,
the piston seals are defective and must be replaced.
5.
If no repairs are necessary or when repairs have been
made, replace counterbalance valve and carefully con-
nect hydraulic hoses to cylinder port block.
6.
If used, remove lifting device from upright or remove
prop from below main boom, activate hydraulic system
and run cylinder through one complete cycle to check
for leaks.
Summary of Contents for 740AJ
Page 2: ......
Page 55: ...SECTION 3 CHASSIS TURNTABLE 3121160 3 3 This page left blank intentionally...
Page 116: ...SECTION 3 CHASSIS TURNTABLE 3 64 3121160 Figure 3 44 Swing Hub Prior to SN 0300074383...
Page 203: ...SECTION 3 CHASSIS TURNTABLE 3121160 3 151 Figure 3 77 EFI Component Location...
Page 206: ...SECTION 3 CHASSIS TURNTABLE 3 154 3121160 Figure 3 78 ECM EPM Identification ECM EPM...
Page 224: ...SECTION 3 CHASSIS TURNTABLE 3 172 3121160 Figure 3 83 Deutz EMR 2 Troubleshooting Flow Chart...
Page 228: ...SECTION 3 CHASSIS TURNTABLE 3 176 3121160 Figure 3 87 EMR 2 Engine Plug Pin Identification...
Page 229: ...SECTION 3 CHASSIS TURNTABLE 3121160 3 177 Figure 3 88 EMR 2 Vehicle Plug Pin Identification...
Page 230: ...SECTION 3 CHASSIS TURNTABLE 3 178 3121160 Figure 3 89 EMR2 Fault Codes Sheet 1 of 5...
Page 231: ...SECTION 3 CHASSIS TURNTABLE 3121160 3 179 Figure 3 90 EMR2 Fault Codes Sheet 2 of 5...
Page 232: ...SECTION 3 CHASSIS TURNTABLE 3 180 3121160 Figure 3 91 EMR2 Fault Codes Sheet 3 of 5...
Page 233: ...SECTION 3 CHASSIS TURNTABLE 3121160 3 181 Figure 3 92 EMR2 Fault Codes Sheet 4 of 5...
Page 234: ...SECTION 3 CHASSIS TURNTABLE 3 182 3121160 Figure 3 93 EMR2 Fault Codes Sheet 5 of 5...
Page 303: ...SECTION 4 BOOM PLATFORM 3121160 4 31 Figure 4 20 Rotator Assembly HELAC...
Page 460: ...SECTION 5 BASIC HYDRAULIC INFORMATION AND SCHEMATICS 5 116 3121160 NOTES...
Page 467: ...SECTION 6 JLG CONTROL SYSTEM 3121160 6 7 Figure 6 2 ADE Block Diagram...
Page 534: ...SECTION 6 JLG CONTROL SYSTEM 6 74 3121160 NOTES...
Page 580: ...SECTION 7 BASIC ELECTRICAL INFORMATION SCHEMATICS 7 46 3121160 NOTES...
Page 581: ......