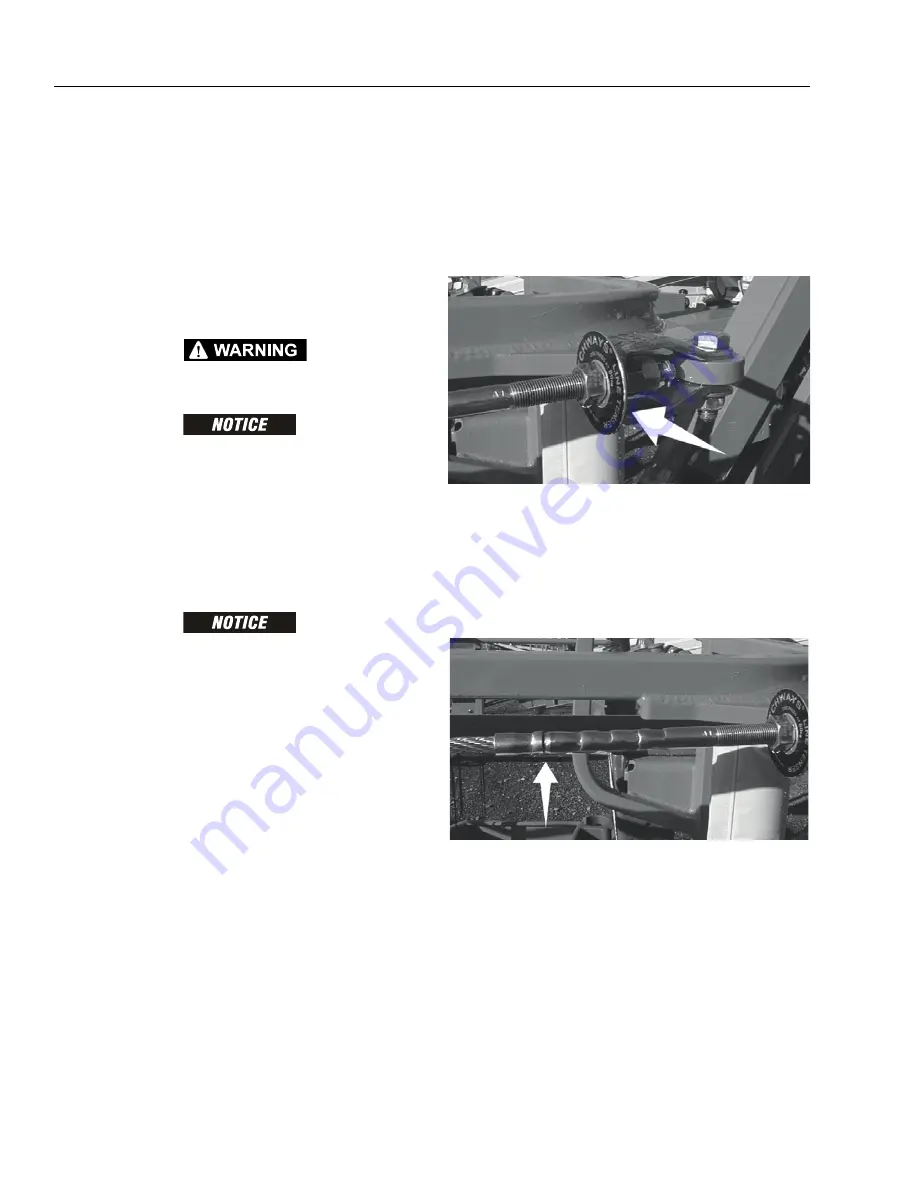
SECTION
4
- BOO
M
& PLATFOR
M
4-70
3121160
4.20 USE AND CARE OF FALL ARREST SYSTEM
The external fall arrest system is designed to provide a lanyard
attach point while allowing the operator to access areas of an
aircraft for inspection and maintenance purposes. Exit/Enter
the platform through the gate area only. The system is
designed for use by one person.
Personnel must use fall protection at all times. A full body har-
ness and shock absorbing lanyard, not to exceed 6 feet (1.8 m)
in length, is required when using the external fall arrest sys-
tem.
DO NOT OPERATE ANY MACHINE FUNCTIONS WHILE OUTSIDE OF THE PLAT-
FORM. BE CAREFUL WHEN ENTERING/EXITING THE PLATFORM AT ELEVATION.
THE EXTERNAL FALL ARREST SYSTEM REQUIRES AN ANNUAL INSPECTION AND
CERTIFICATION. THE ANNUAL INSPECTION AND CERTIFICATION MUST BE PER-
FORMED BY A COMPETENT PERSON.
If inspection services are required, contact:
Flexible Lifeline Systems
14325 West Hardy Rd.
Houston, TX 77060
Phone: 281-448-8821
IF THE FALL ARREST SYSTEM IS USED TO ARREST A FALL OR IS OTHERWISE
DAMAGED, THE ENTIRE SYSTEM MUST BE REPLACED AND THE PLATFORM
FULLY INSPECTED. REFER TO THE SERVICE MANUAL.
Prior to Use Inspection
Fall arrest systems must be inspected prior to each use.
Replace if there are any signs of wear or damage to any of the
components.
Prior to use inspection should include a visual inspection of
the following items:
Cable: Proper tension, broken strands, corrosion.
Fittings: Loose fittings and fractures, damage to
hanger.
Transfastener: Damage, free and proper sliding
Attaching Hardware: Loose, missing, properly
tightened.
Inspecting Cable Tension and Slip Indicator
Cable tension is adjusted using the Line Tenser. The Line
Tenser is the disc at the end of the cable (shown below). When
proper tension is achieved, the disc will spin by hand. When
less than proper tension is present the disc will not turn by
hand. The cable will stretch normally over time. To tension the
cable, rotate the turnbuckle until proper tension is achieved.
The slip indicator is the short tube crimped beside the end
connection of the cable. If the cable slips from the end con-
nection a gap will be present between the slip indicator and
the end connection. No gap is acceptable. A cable that is
slipped should be taken out of service and the system
replaced.
Shown below is the slip indicator as it should appear.
Summary of Contents for 740AJ
Page 2: ......
Page 55: ...SECTION 3 CHASSIS TURNTABLE 3121160 3 3 This page left blank intentionally...
Page 116: ...SECTION 3 CHASSIS TURNTABLE 3 64 3121160 Figure 3 44 Swing Hub Prior to SN 0300074383...
Page 203: ...SECTION 3 CHASSIS TURNTABLE 3121160 3 151 Figure 3 77 EFI Component Location...
Page 206: ...SECTION 3 CHASSIS TURNTABLE 3 154 3121160 Figure 3 78 ECM EPM Identification ECM EPM...
Page 224: ...SECTION 3 CHASSIS TURNTABLE 3 172 3121160 Figure 3 83 Deutz EMR 2 Troubleshooting Flow Chart...
Page 228: ...SECTION 3 CHASSIS TURNTABLE 3 176 3121160 Figure 3 87 EMR 2 Engine Plug Pin Identification...
Page 229: ...SECTION 3 CHASSIS TURNTABLE 3121160 3 177 Figure 3 88 EMR 2 Vehicle Plug Pin Identification...
Page 230: ...SECTION 3 CHASSIS TURNTABLE 3 178 3121160 Figure 3 89 EMR2 Fault Codes Sheet 1 of 5...
Page 231: ...SECTION 3 CHASSIS TURNTABLE 3121160 3 179 Figure 3 90 EMR2 Fault Codes Sheet 2 of 5...
Page 232: ...SECTION 3 CHASSIS TURNTABLE 3 180 3121160 Figure 3 91 EMR2 Fault Codes Sheet 3 of 5...
Page 233: ...SECTION 3 CHASSIS TURNTABLE 3121160 3 181 Figure 3 92 EMR2 Fault Codes Sheet 4 of 5...
Page 234: ...SECTION 3 CHASSIS TURNTABLE 3 182 3121160 Figure 3 93 EMR2 Fault Codes Sheet 5 of 5...
Page 303: ...SECTION 4 BOOM PLATFORM 3121160 4 31 Figure 4 20 Rotator Assembly HELAC...
Page 460: ...SECTION 5 BASIC HYDRAULIC INFORMATION AND SCHEMATICS 5 116 3121160 NOTES...
Page 467: ...SECTION 6 JLG CONTROL SYSTEM 3121160 6 7 Figure 6 2 ADE Block Diagram...
Page 534: ...SECTION 6 JLG CONTROL SYSTEM 6 74 3121160 NOTES...
Page 580: ...SECTION 7 BASIC ELECTRICAL INFORMATION SCHEMATICS 7 46 3121160 NOTES...
Page 581: ......