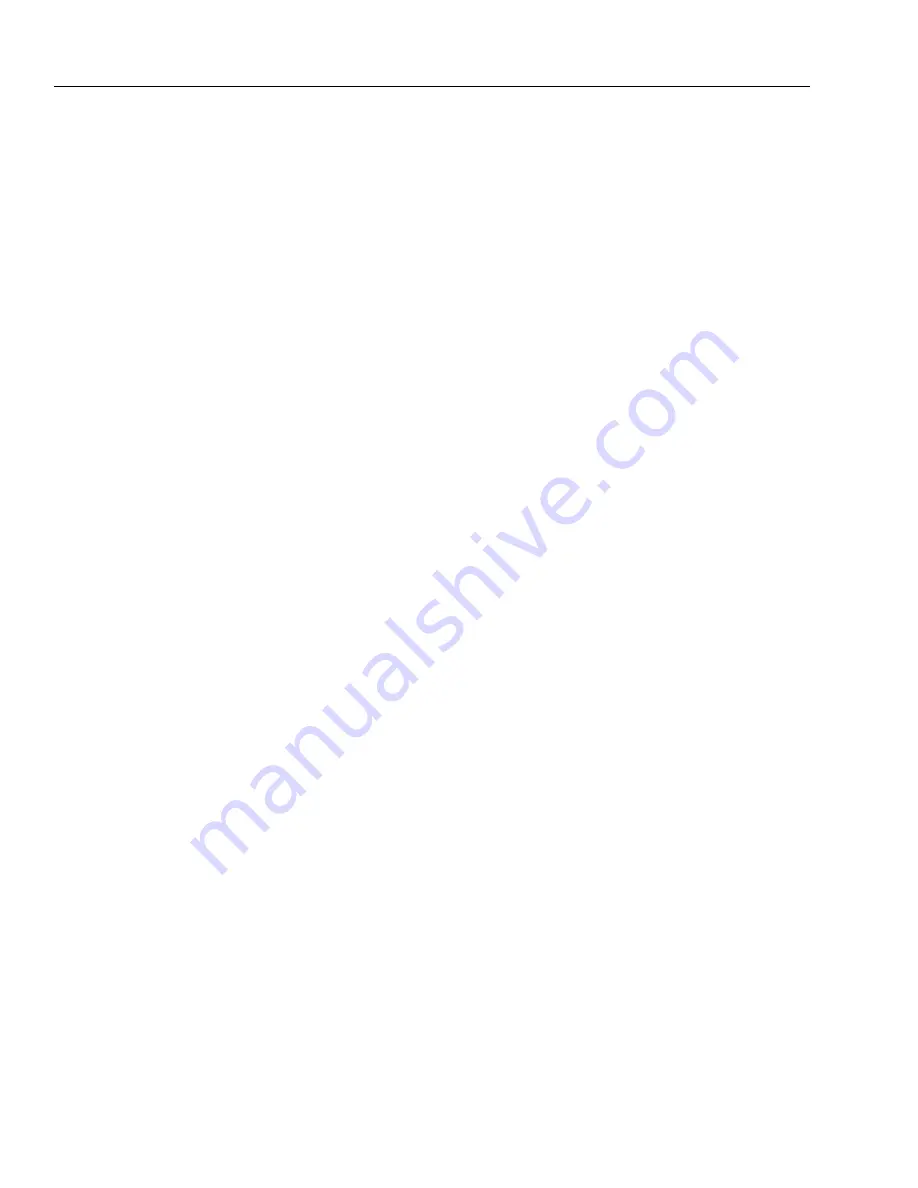
SECTION 5 - BASIC HYDRAULIC INFOR
M
ATION AND SCHE
M
ATICS
5-4
3121160
5.
Check the Tower lift up holding valve function as fol-
lows:
a.
Fully retract and fully lower the main boom and
tower boom assemblies.
b.
Install a 5000 psi (345 bar) pressure gauge to the
pressure tap connection installed on port #7 or port
MX7 of the main control valve block. This pressure
test connection was installed in earlier steps.
c.
Hold the tower boom lift up function between 2
and 5 seconds, and then release the function.
d.
Verify that the gauge reads, and maintains, pressure
above 1000 psi (68.95 bar) for one minute.
NOTE:
If pressure does not remain above the stated pressure for
one minute, replace the tower lift check valve (#7017474).
e.
Activate tower lift down to release any trapped
pressure and remove pressure gauge from the test
port.
6.
Load the platform with the rated capacity and cycle all
functions a minimum of five times to confirm safe and
proper operational characteristics.
7.
The machine may be returned to service once proper
operation is confirmed.
5.4
CYLINDERS - THEORY OF OPERATION
Systems Incorporating Double Acting Cylinders
Cylinders are of the double acting type. Systems incorporating
double acting cylinders are as follows: - Tower Lift, Slave Level/
Main Level, Main Lift, Main Telescope, Master Level/Upright
Level, Articulating Jib Boom Lift, Steer and Axle lockout. A
double acting cylinder is one that requires oil flow to operate
the cylinder rod in both directions. Directing oil (by actuating
the corresponding control valve to the piston side of the cylin-
der) forces the piston to travel toward the rod end of the bar-
rel, extending the cylinder rod (piston attached to rod). When
the oil flow is stopped, movement of rod will stop. By directing
oil to the rod side of the cylinder, the piston will be forced in
the opposite direction and the cylinder rod will retract.
Systems Incorporating Holding Valves
Holding valves are used in the - Tower lift, Tower Telescope,
Upright Level, Lockout, Articulating Jib Boom Lift, Main Lift/
Slave Level and Main Telescope circuits to prevent retraction
of the cylinder rod should a hydraulic line rupture or a leak
develop between the cylinder and its related control valve.
Summary of Contents for 740AJ
Page 2: ......
Page 55: ...SECTION 3 CHASSIS TURNTABLE 3121160 3 3 This page left blank intentionally...
Page 116: ...SECTION 3 CHASSIS TURNTABLE 3 64 3121160 Figure 3 44 Swing Hub Prior to SN 0300074383...
Page 203: ...SECTION 3 CHASSIS TURNTABLE 3121160 3 151 Figure 3 77 EFI Component Location...
Page 206: ...SECTION 3 CHASSIS TURNTABLE 3 154 3121160 Figure 3 78 ECM EPM Identification ECM EPM...
Page 224: ...SECTION 3 CHASSIS TURNTABLE 3 172 3121160 Figure 3 83 Deutz EMR 2 Troubleshooting Flow Chart...
Page 228: ...SECTION 3 CHASSIS TURNTABLE 3 176 3121160 Figure 3 87 EMR 2 Engine Plug Pin Identification...
Page 229: ...SECTION 3 CHASSIS TURNTABLE 3121160 3 177 Figure 3 88 EMR 2 Vehicle Plug Pin Identification...
Page 230: ...SECTION 3 CHASSIS TURNTABLE 3 178 3121160 Figure 3 89 EMR2 Fault Codes Sheet 1 of 5...
Page 231: ...SECTION 3 CHASSIS TURNTABLE 3121160 3 179 Figure 3 90 EMR2 Fault Codes Sheet 2 of 5...
Page 232: ...SECTION 3 CHASSIS TURNTABLE 3 180 3121160 Figure 3 91 EMR2 Fault Codes Sheet 3 of 5...
Page 233: ...SECTION 3 CHASSIS TURNTABLE 3121160 3 181 Figure 3 92 EMR2 Fault Codes Sheet 4 of 5...
Page 234: ...SECTION 3 CHASSIS TURNTABLE 3 182 3121160 Figure 3 93 EMR2 Fault Codes Sheet 5 of 5...
Page 303: ...SECTION 4 BOOM PLATFORM 3121160 4 31 Figure 4 20 Rotator Assembly HELAC...
Page 460: ...SECTION 5 BASIC HYDRAULIC INFORMATION AND SCHEMATICS 5 116 3121160 NOTES...
Page 467: ...SECTION 6 JLG CONTROL SYSTEM 3121160 6 7 Figure 6 2 ADE Block Diagram...
Page 534: ...SECTION 6 JLG CONTROL SYSTEM 6 74 3121160 NOTES...
Page 580: ...SECTION 7 BASIC ELECTRICAL INFORMATION SCHEMATICS 7 46 3121160 NOTES...
Page 581: ......