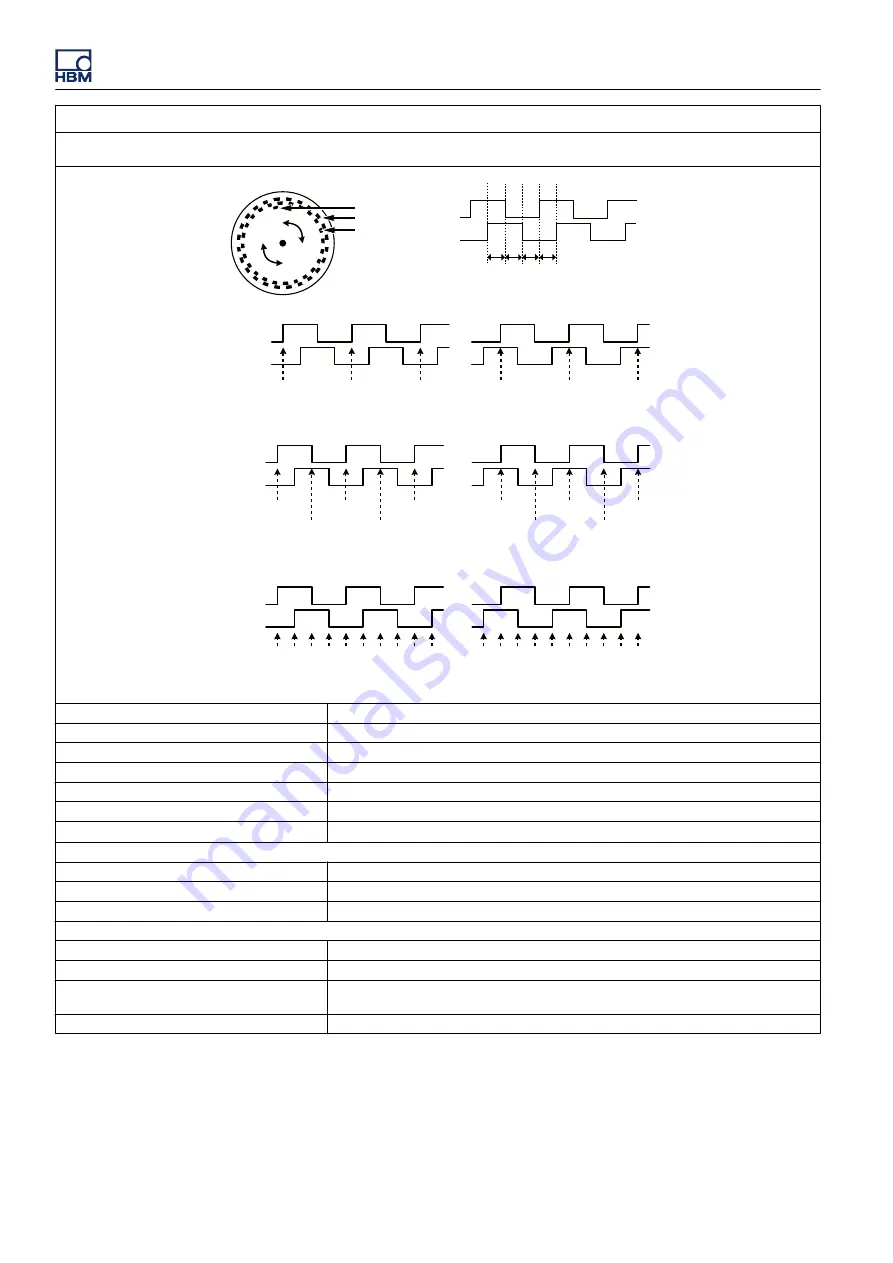
Timer/Counter Mode Bi
-
directional Quadrature Count
Typically used for tracking rotating/moving devices using a decoder with two signals that are always 90 degree phase shifted. E.g. allow for
direct interfacing to HBM torque and speed transducers.
∆t
∆t
∆t
∆t
Signal
Direction
Single precision counting
Count Up
Count Up
Count Up
Count Down
Count Down
Count Down
Signal
Direction
Double precision counting
Count Up
Count Up
Count Up
Count Down
Count Down
Count Down
Count Up
Count Up
Count Down
Count Down
Signal
Direction
Quad precision counting
Count Up
Count Up
Count Up
Count Down
Count Down
Count Down
Wheel rotates clock wise
Wheel rotates counter clock wise
Wheel rotates clock wise
Wheel rotates counter clock wise
Wheel rotates clock wise
Wheel rotates counter clock wise
Signal
Reset
Quadrature disk
Signal
Direction
Direction
∆t: Must be > 100 ns
Figure A.252:
Bi
-
directional quadrature count modes
Inputs
3 pins: signal, direction and reset
Maximum input frequency
2 MHz
Minimum pulse width
200 ns (2 * Δt)
Minimum setup time
100 ns (Δt)
Minimum hold time
100 ns (Δt)
Accuracy
Single, dual or quad precision
Counter range
-
2
31
to +2
31
-
1
Reset input
Level sensitivity
User selectable invert level
Minimum setup time prior to signal edge (Δt)
100 ns
Minimum hold time after signal edge (Δt)
100 ns
Reset options
Manual
Upon user request by software command
Start recording
Count value set to 0 at Start of recording
First reset pulse
After the recording is started, the first reset pulse sets the counter value to 0. The next reset
pulses are ignored.
Each reset pulse
On each external reset pulse, the counter value is reset to 0.
GEN3i
664
I3763-3.1 en HBM: public