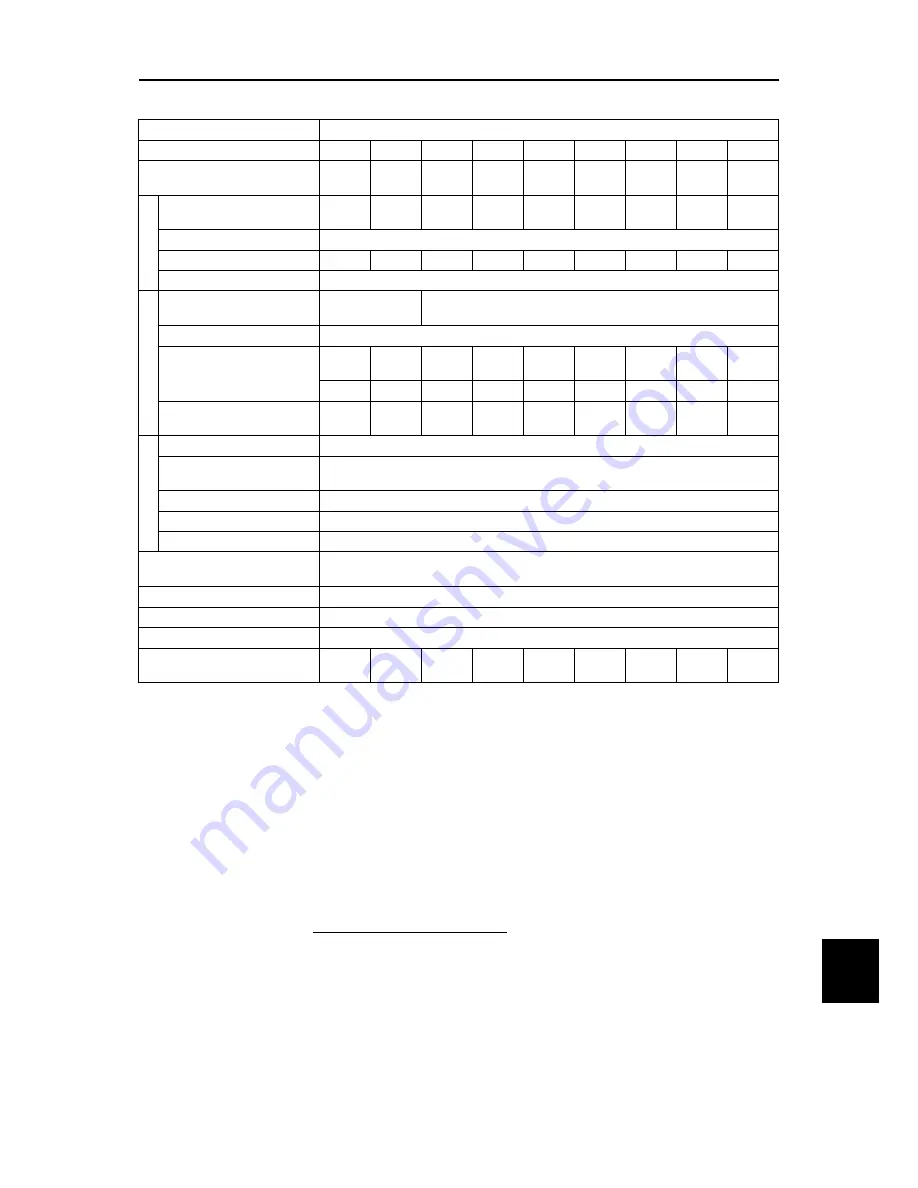
12.1 Standard Model
12-3
SP
EC
IF
IC
AT
IO
N
S
Chap 1
2
■
Standard-model, Three-phase 400 V (460 V) class series (ND-mode: 75 kW to 315 kW)
Item
Specifications
Type (FRN_ _ _ _E2S-4
)
0139
0168
0203
0240
0290
0361
0415
0520
0590
Nominal applied motor (kW) [HP]
(Output rating)
*1
75
[100]
90
[125]
110
[150]
132
[200]
160
[200]
200
[300]
220
[350]
280
[450]
315
[500]
O
utput r
ati
ngs
Rated capacity (kVA)
*2
106
[111]
128
[134]
155
[162]
183
[191]
221
[231]
275
[288]
316
[331]
396
[414]
450
[470]
Rated voltage (V)
*
3
Three-phase 380 to 480 V (with AVR function)
Rated current (A)
*
4
139
168
203
240
290
361
415
520
590
Overload capability
120%-1 min
Input powe
r
Voltage, frequency
Three-phase 380
to 480 V, 50/60 Hz
Three-phase 380 to 440 V, 50 Hz
Three-phase 380 to 480 V, 60 Hz
*5
Allowable voltage/frequency
Voltage: +10 to -15% (Interphase voltage unbalance: 2% or less)
*6
, Frequency: +5 to -5%
Rated input current
*7
(w/o DCR) (A)
–
–
–
–
–
–
–
–
–
(with DCR) (A)
138
164
201
238
286
357
390
500
559
Required capacity
(with DCR) (kVA)
*8
96
114
139
165
199
248
271
347
388
B
rak
ing
Torque (%)
*9
5% to 9%
DC braking
Braking starting frequency: 0.0 to 60.0 Hz, Braking time: 0.0 to 30.0 s,
Braking level: 0 to 60%
Braking transistor
Separately mounted option
Minimum resistance value
(
Ω
) –
Braking resistor
Separately mounted option
DC reactor (DCR)
Must be used. Separately mounted component. Depending on the shipping destination, not
provided with the inverter package.
*11
Applicable safety standards
IEC/EN61800-5-1: 2007
Enclosure (IEC60529)
IP00, UL open type
Cooling method
Fan cooling
Weight / Mass (kg) [lbs]
30
[66]
33
[73]
40
[88]
62
[137]
63
[139]
95
[209]
96
[212]
130
[287]
140
[309]
Note: A box (
) in the above table replaces GA, GB or C depending on the model.
*1 Fuji 4-pole standard motor
*2 Rated capacity is calculated assuming the rated output voltage as 440 V (460 V).
*3 Output voltage cannot exceed the power supply voltage.
*4 Setting the carrier frequency (F26) to the following value or above requires current derating.
ND spec. of all types : 4 kHz
If the ambient temperature is 40°C (104°F) or above, derating of 2%/°C (2%/1.8°F) relative to the rated
current given in this manual is required. For details, refer to Figure 10.4-1 in Chapter 10 “10.4.2 Guideline for
selecting inverter drive mode and capacity.”
*5
Inverters of FRN0203E2■
-4
or above (400 V class series) are equipped with a power switching connector.
Use the connector depending upon the applied voltage. For details, refer to Chapter 2 “2.2.7 Switching
Connector.”
*6
67
×
(V)
voltage
average
phase
-
Three
(V)
voltage
Min.
-
(V)
voltage
Max.
=
(%)
unbalance
Voltage
(IEC 61800-3)
If the unbalance ratio is 2% to 3%, use an optional AC reactor (ACR).
*7 This specification is an estimated value to be applied when the power supply capacity is 500 kVA (Inverter
capacity × 10 when the capacity exceeds 50 kVA) and the power supply with %X = 5% is connected. When
applying with motors of 75 kW (100 HP) or above, a DC reactor (DCR) should be used.
*8 This specification applies when a DC reactor (DCR) is used.
*9 Average braking torque for the motor running alone. It depends on the efficiency of the motor.
*11 Please consult your Fuji Electric sales representative.
Summary of Contents for FRENIC-Ace series
Page 20: ......
Page 32: ......
Page 92: ......
Page 94: ......
Page 452: ......
Page 490: ......
Page 504: ......
Page 508: ...8 2 Frequency Setting Section 8 4 Figure 8 2 3 Frequency Setting Section Block Diagram...
Page 520: ...8 6 Control Section 8 16 6 For PMSM Figure 8 6 9 Vector Control For PMSM Section Block Diagram...
Page 522: ...8 7 FM Output Section 8 18 8 7 FM Output Section Figure 8 7 1 FM Output Section Block Diagram...
Page 582: ......
Page 664: ...11 15 External Cooling Fan Attachments 11 60...
Page 690: ......
Page 692: ......
Page 720: ......
Page 738: ......
Page 787: ......