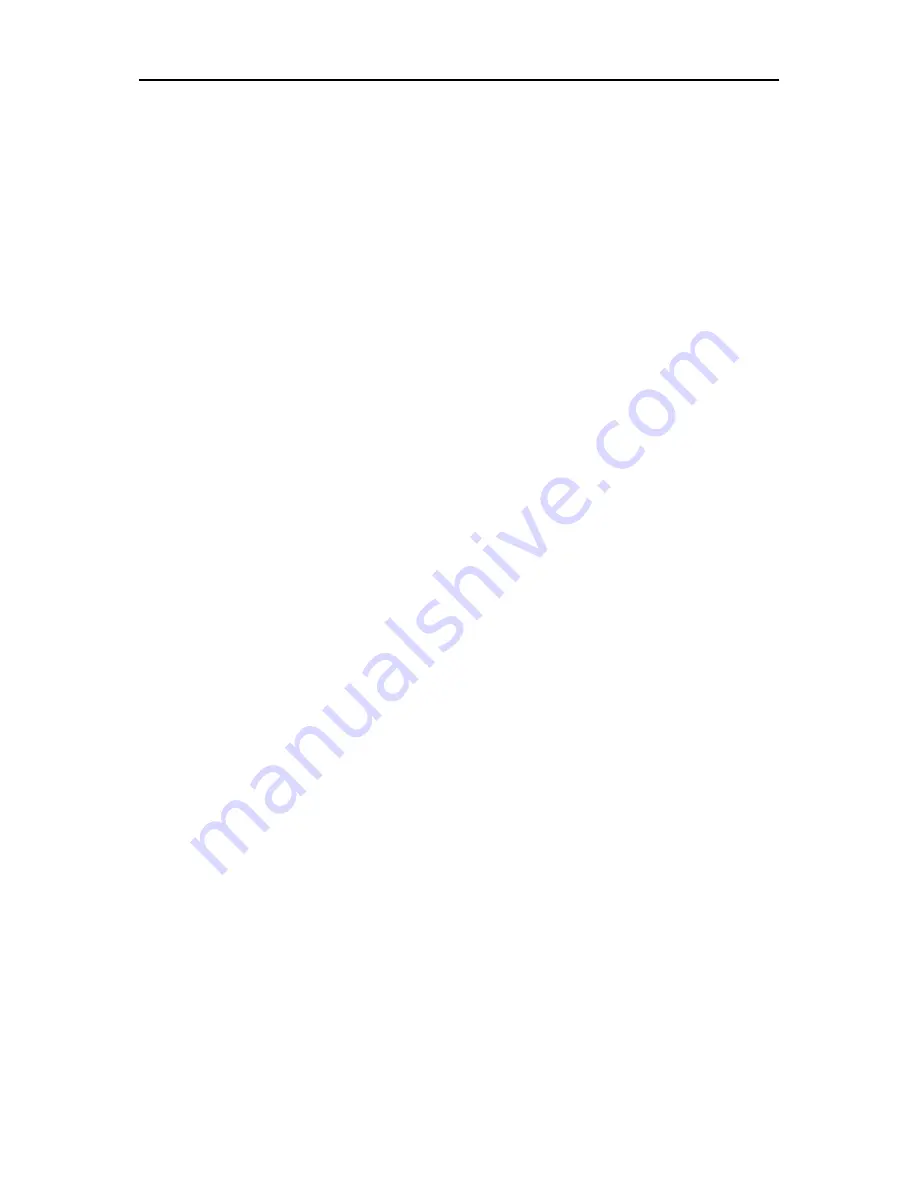
10.1 Motor Output Torque Characteristics
10-2
(1) Continuous allowable driving torque
Standard motor (Curve (a1) in Figure 10.1-1 and Figure 10.1-2)
Curve (a1) shows the torque characteristic that can be obtained in the range of the inverter continuous rated
current, where the standard motor's cooling characteristic is taken into consideration. When the motor runs at
the base frequency of 60 Hz, 100 % output torque can be obtained; at 50 Hz, the output torque is somewhat
lower than that in commercial power, and it further lowers at lower frequencies. The reduction of the output
torque at 50 Hz is due to increased loss by inverter driving, and that at lower frequencies is mainly due to heat
generation caused by the decreased ventilation performance of the motor cooling fan.
Motor exclusively designed for vector control (Curve (a2) in Figure 10.1-1 and Figure 10.1-2)
Curve (a2) shows the torque characteristic that can be obtained in the range of the inverter continuous rated
current, where the motor exclusively designed for vector control is connected. In the motor exclusively designed
for vector control, the attached forced-cooling fan reduces heat generation from the motor, so that the torque
does not drop in the low-speed range, compared to the standard motor.
(2) Maximum driving torque in a short time
(Curves (b) and (c) in Figure 10.1-1 and Figure 10.1-2)
Curve (b) shows the torque characteristic that can be obtained in the range of the inverter overload capability in a
short time (ND/HND mode: 120% for 1 minute, HD mode: 150% for 1 minute, HHD mode: 150% for 1 minute and
200% for 0.5 seconds) when torque-vector control is enabled. At that time, the motor cooling characteristics have
little effect on the output torque.
Curve (c) shows an example of the torque characteristic when one class higher capacity inverter is used to
increase the short-time maximum torque. In this case, the short-time torque is 20 to 30% greater than that when the
standard capacity inverter is used.
(3) Starting torque
(around the output frequency 0 Hz in Figure 10.1-1 and Figure 10.1-2)
The maximum torque in a short time applies to the starting torque as it is.
(4) Braking torque
(Curves (d), (e), and (f) in Figure 10.1-1 and Figure 10.1-2)
In braking the motor, kinetic energy is converted to electrical energy and regenerated to the DC link bus capacitor
(reservoir capacitor) of the inverter. Discharging this electrical energy to the braking resistor produces a large
braking torque as shown in curve (e). If no braking resistor is provided, however, only the motor and inverter losses
consume the regenerated braking energy so that the torque becomes smaller as shown in curve (d).
When an optional braking resistor is used, the braking torque is allowable only for a short time. Its time ratings are
mainly determined by the braking resistor ratings. This manual and associated catalogs list the allowable values
(kW) obtained from the average discharging loss and allowable values (kWs) obtained from the discharging
capability that can be discharged at one time.
Note that the torque % value varies according to the inverter capacity.
Selecting an optimal brake unit enables a braking torque value to be selected comparatively freely in the range
below the short-time maximum torque in the driving mode, as shown in curve (f).
For braking-related values when the inverter and braking resistor are normally combined, refer to Chapter 11
“11.8 Braking Resistors (DBRs) and Braking Units.”
Summary of Contents for FRENIC-Ace series
Page 20: ......
Page 32: ......
Page 92: ......
Page 94: ......
Page 452: ......
Page 490: ......
Page 504: ......
Page 508: ...8 2 Frequency Setting Section 8 4 Figure 8 2 3 Frequency Setting Section Block Diagram...
Page 520: ...8 6 Control Section 8 16 6 For PMSM Figure 8 6 9 Vector Control For PMSM Section Block Diagram...
Page 522: ...8 7 FM Output Section 8 18 8 7 FM Output Section Figure 8 7 1 FM Output Section Block Diagram...
Page 582: ......
Page 664: ...11 15 External Cooling Fan Attachments 11 60...
Page 690: ......
Page 692: ......
Page 720: ......
Page 738: ......
Page 787: ......