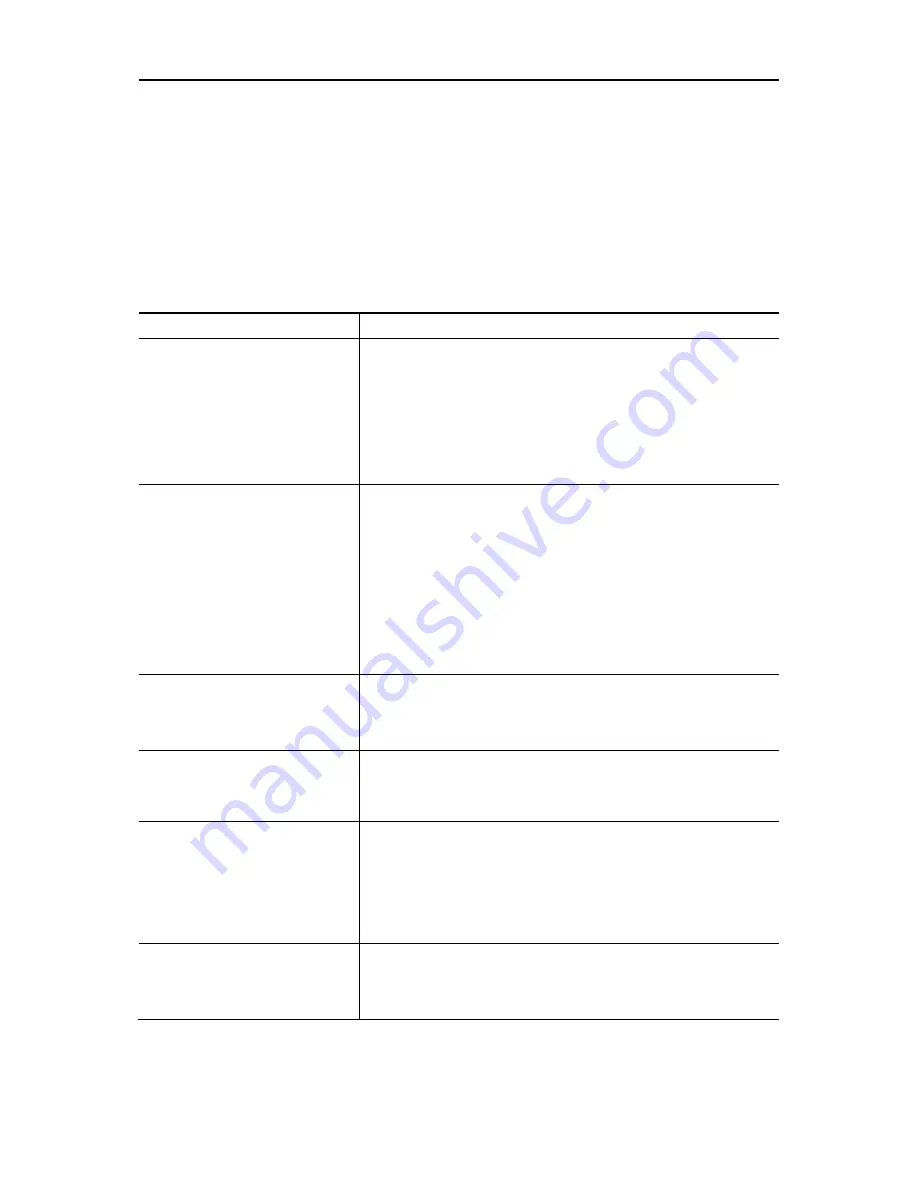
6.5 When Codes Other Than Alarm Codes and Light Alarm Indication (
l-al
) are Displayed
6-24
6.5 When Codes Other Than Alarm Codes and Light Alarm Indication (
l-al
)
are Displayed
This section describes the troubleshooting procedure based on function codes dedicated to motor 1. When motor 2
is used, it is necessary to convert to the corresponding function codes. The function codes that need to be
converted are marked with “*.”
For the function codes to be converted, see Chapter 5 “FUNCTION CODES.”
6.5.1 Abnormal motor operation
[ 1 ] The motor does not rotate
Possible Causes
Check and Measures
(1) No power supplied to the
inverter.
Check the input voltage and interphase voltage unbalance.
Switch on the molded-case circuit breaker, an earth-leakage circuit
breaker (with overcurrent protective function) or a magnetic
contactor.
Check for voltage drop, phase loss, poor connections, or poor
contacts, and fix them if necessary.
If only the auxiliary control power input is supplied, also supply the
main power to the inverter.
(2) No forward/reverse operation
command was inputted, or both
the commands were inputted
simultaneously (external signal
operation).
Check the input status of the forward/reverse command with Menu “I/O
Checking” using the keypad.
Input a run command.
Set either the forward or reverse operation command to OFF.
Correct the run command source. Set F02 data to “1.”
Correct the assignment error of terminals [FWD], [REV]. (E98, E99)
Connect the external circuit wires to control circuit terminals [FWD]
and [REV] correctly.
Make sure that the sink/source slide switch (SW1) on the control
printed circuit board (control PCB) is properly configured.
(3) No rotational direction is
instructed.
(Keypad operation)
Check the input status of the forward/reverse rotation direction
command with Menu “I/O Checking” using the keypad.
Input the rotation direction (F02 = 0), or select the keypad operation
with which the rotation direction is fixed (F02 = 2 or 3).
(4) The inverter could not accept
any run commands from the
keypad since it was in
Programming mode.
Check which operation mode the inverter is in, using the keypad.
Shift the operation mode to Running mode and enter a run
command.
(5) A run command with higher
priority than the one attempted
was active, and the run
command was stopped.
Based on the run command block diagram (See Chapter 8 “BLOCK
DIAGRAMS FOR CONTROL LOGIC”), check a higher priority run
command by function code data check and I/O checking from Menu
using the keypad.
Correct any incorrect function code data settings such as link
function (Mode selection) (H30) and bus link function (Mode
selection) (y98) or cancel the higher priority run command.
(6) No analog frequency command
input.
Check that a reference frequency has been entered correctly, using
Menu “I/O Checking” on the keypad.
Connect external circuit wirings of terminals [13], [12], [11], [C1]
correctly.
Summary of Contents for FRENIC-Ace series
Page 20: ......
Page 32: ......
Page 92: ......
Page 94: ......
Page 452: ......
Page 490: ......
Page 504: ......
Page 508: ...8 2 Frequency Setting Section 8 4 Figure 8 2 3 Frequency Setting Section Block Diagram...
Page 520: ...8 6 Control Section 8 16 6 For PMSM Figure 8 6 9 Vector Control For PMSM Section Block Diagram...
Page 522: ...8 7 FM Output Section 8 18 8 7 FM Output Section Figure 8 7 1 FM Output Section Block Diagram...
Page 582: ......
Page 664: ...11 15 External Cooling Fan Attachments 11 60...
Page 690: ......
Page 692: ......
Page 720: ......
Page 738: ......
Page 787: ......