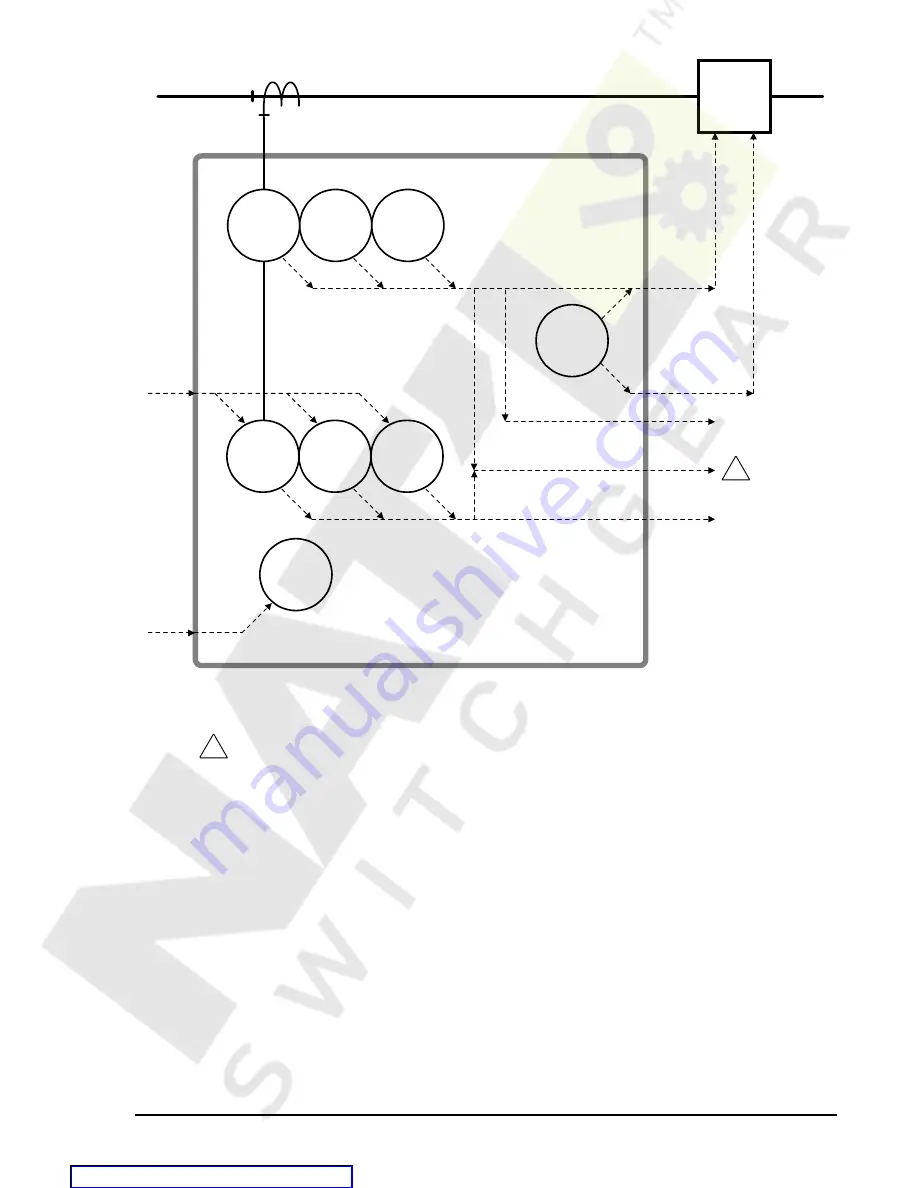
BE1-951
Application
8-41
BE1-951
D 2 8 4 9 - 0 3
01-05-00
52
OUT1
TRIP
51P
51N
51Q
OUT5
50TQ
50TN
50TP
101
IN2
INST
BLOCK
GROUP
CONTROL
T
C
CLOSE
OUT2
OUT3
OUT4
IN3
2
Relay is shown in Normal mode (not in Test mode).
If the feeder relay is out of service, the 50T and 51 elements are diverted from
OUT1 and OUT4 to OUT5 for feeder protection.
2
1
Figure 8-11. BUS One-Line Drawing
BUS Logic Settings and Equations
SL-N:BUS
SL-50TP:1,IN2; SL-50TN:1,IN2; SL-50TQ:1,IN2
SL-150TP:0,0; SL-150TN:0,0; SL-150TQ:0,0
SL-51P:1,0
SL-51N:1,0
SL-51Q:1,0
SL-151N:0,0
SL-27P:0,0
SL-59P:0,0; SL-59X:0,0
SL-47:0,0