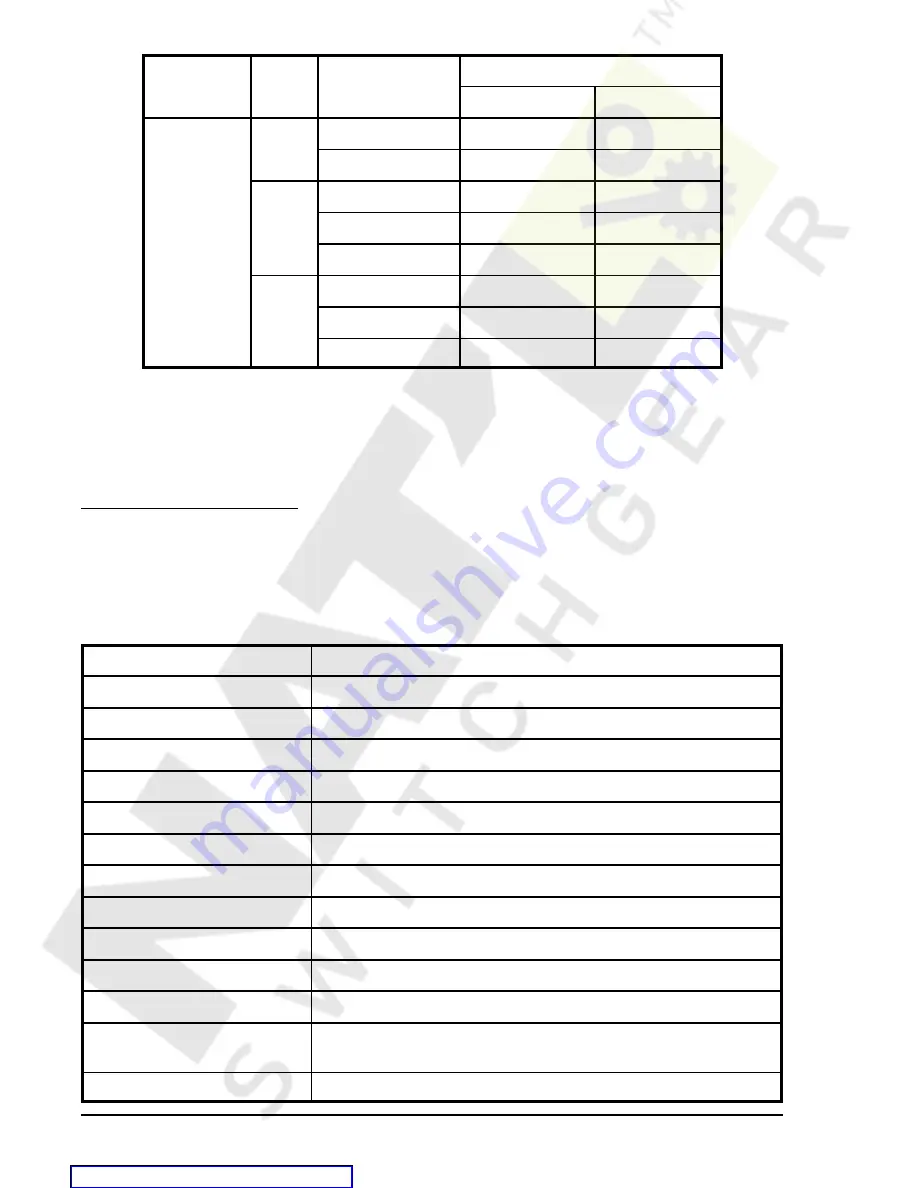
13-26
Testing and Maintenance
BE1-951
Sensing
Type
Time
Dial
Applied Current
Relay Trip Limits
Lower Limit
Higher Limit
5A
0.5
2.5 A
0.19 seconds
0.24 seconds
12.5 A
0.1 seconds
0.15 seconds
5.0
0.75 A
7.244 seconds
8.007 seconds
2.5 A
1.798 seconds
1.988 seconds
12.5 A
0.944 seconds
1.044 seconds
9.9
0.75 A
14.318 seconds
15.825 seconds
2.5 A
3.535 seconds
3.907 seconds
12.5 A
1.844 seconds
2.038 seconds
Step 4 Repeat Steps 2 and 3 for all of the current and time dial settings for your current sensing type.
Step 5 (Optional) Repeat Steps 2 through 4 for phase B (terminals D3 and D4) and phase C (terminals D5
and D6).
Step 6 (Optional) Repeat Steps 1 through 5 for the 151N element. Using ASCII commands, substitute 151
for any 51 logic or setting commands in each test.
Pickup and Dropout Verification
Purpose: To verify the pickup accuracy of the 51P, 51N, 151N, and 51Q elements.
Reference Commands: SL-51P, SL-51N, SL-51Q, SL-151N, , SL-GROUP, SL-VO
Step 1 Connect a current source to terminals D1 and D2 (A-phase). Refer to Figure 13-1 for terminal
locations. An ohmmeter or continuity tester may be used to monitor output contact status.
Step 2 To prepare the 51P, 51N, and 51Q elements for testing, transmit the commands in Table 13-26 to
the relay. Reset targets.
Table 13-26. 51P, 51N, and 51Q Pickup Test Commands
Command
Purpose
A=
Gain write access
SL-N=NONE
Zero out custom logic settings. Overwrite with logic=none settings.
Y
Confirm overwrite
SL-N=PU51
Sets PU51 as custom logic name
SL-51P=1,0
Enables 51P and disables blocking
SL-51N=1,0
Enables 51N and disables blocking
SL-51Q=1,0
Enables 51Q and disables blocking
SL-VO1=51PT
Enables OUT1 to close for 51PT trip
SL-VO2=51NT
Enables OUT2 to close for 51NT trip
SL-VO3=51QT
Enables OUT3 to close for 51QT trip
SG-CT=1
Sets P, N CT ratio at 1:1
SG-TRIGGER=51PT+51NT+5
1QT,51PPU+51NPU+51QPU,0
Enable 51PT or 51NT or 51QT to log and trigger fault recording
EXIT;Y
Exit and save settings