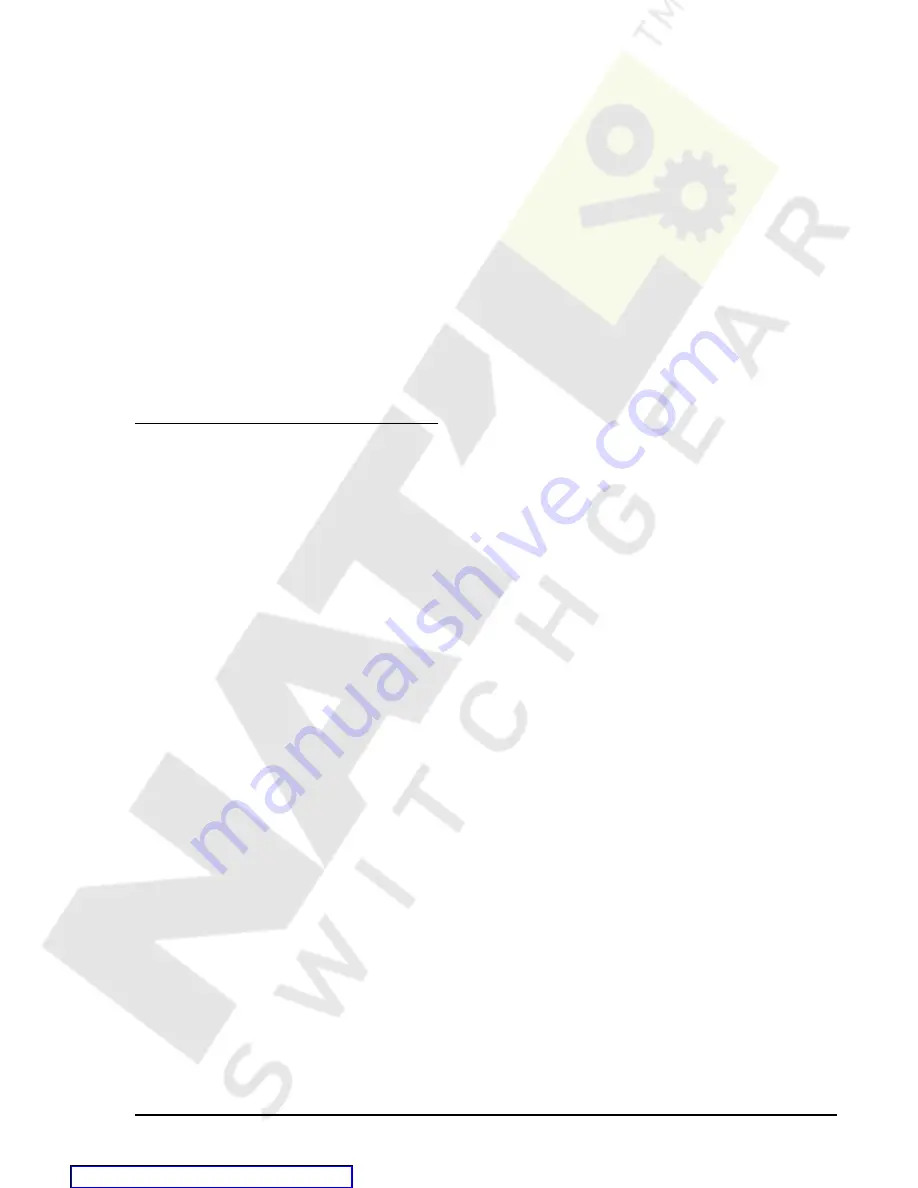
BE1-951
Protection and Control
4-5
alternate setting group that will allow for the large inrush of current the next time the load is energized. After
current had returned to measurable levels for some period of time, the relay returns to the normal settings.
Another application is to prevent the relay from seeing an overload condition as a fault. If the relay sees
sustained high level phase or unbalance currents that are encroaching on normal trip levels (indicative of
an overload or load imbalance rather than a fault), the relay may move to an alternate setting group that may
accommodate the condition. The relay can be set to alarm for this condition using the programmable logic
alarms.).
The relay has the logic to automatically change setting groups based upon the status of the reclose function
(79). This scheme allows the relay to have fast and slow curves, for instance, when the user is applying
automatic reclosing into a fault. On the first trip of a fault the relay may use a setting group with a fast
overcurrent curve and/or a low set instantaneous setting, with the intent of tripping faster than downstream
fuses. On subsequent trips, by monitoring the reclose step, the relay would be in an alternate setting group
with a slower overcurrent response and/or a higher or no instantaneous trip, with the intent of operating
slower than downstream fuses.
The user should also be aware that the 79 function “Sequence Control Block” (79SCB) provides an alternate
method to control relay operation based on the relcose status. See the 79 function description later in this
section for additional details.
Automatic Control by Monitoring Line Current
The operating parameter settings for the setting group control function are provided in Table 4-4. The setting
group 1, 2, and 3
switch to and return settings determine how the function selects the active setting group
when automatic selection is enabled.
Automatic control of the active setting group allows the relay to automatically change configuration for
optimum protection based on the current system conditions. For example, in locations where seasonal
variations can cause large variations in loading, the overcurrent protection can be set with sensitive settings
during the majority of the time and switch to a setting group with lower sensitivity (higher pickups) during the
few days of the year when the loading is at peak.
The relay will switch to a setting group when current rises above the “switch-to threshold” for the “switch-to
time,” and will return from the setting group when current falls below the “return threshold” for the “return
time.” However, if the “switch-to” threshold is 0, and a non-zero switch-to time is entered, then the relay
changes to the indicated setting group and falls below 10% of nominal (0.5A/0.1A for 5A/1A nominal relays)
after the switch-to time. This is used in the example application for cold load pickup, below.
If the monitored element is 791, 792, 793, or 794, the switch-to time, switch-to threshold, return time, and
return threshold are ignored and the setting group is based upon the status for the reclose step. This
method of controlling setting groups will be covered further below.
If a group’s switch-to threshold is zero and the groups the switch-to time delay is 0, and the monitored
element is any overcurrent element (i.e., not 791, 792, 793, or 794), then the relay will never automatically
switch-to that setting group.
There are five settings for each group that are used for automatic control. Each group has a
switch to
threshold and time delay, a
return threshold and time delay, and a monitored element. The switch to and
return thresholds are a percentage of the SG0 pickup setting for the monitored element. The monitored
element can be any of the 51 protective functions. Thus, if you wish to switch settings based upon loading,
you could set it to monitor 51P. If you wish to switch settings based upon unbalance, you could set it to
monitor 51N,151N, or 51Q. When the monitored element is 51P, any one phase must be above the
switch
to threshold for the switch to time delay for the criteria to be met. All phases must be below the return
threshold for the
return time delay for the return criteria to be met.
Figure 4-3 shows an example of using the automatic setting group selection settings to change settings
groups based upon loading. Note that the AUTO input must be at a TRUE logic state in order to allow the
automatic logic to operate. At time = 0, current begins to increase. When current reaches 75 percent of
pickup, setting group two begins timing (30 minutes). When current reaches 90 percent of pickup, setting
group three begins timing (5 minutes). After 5 minutes, at time = 37, with the current still above setting group
three threshold, setting group three becomes active and the setting group change output pulses. At time =