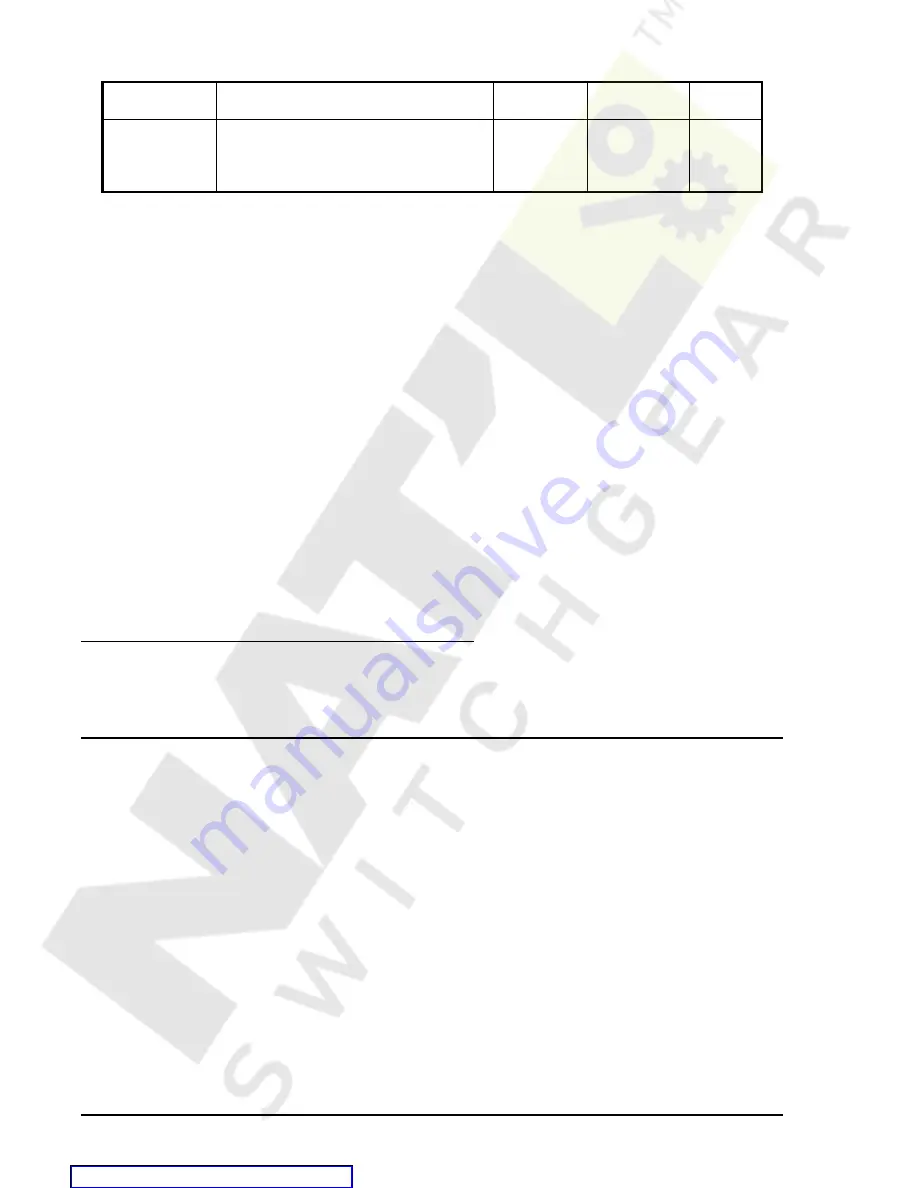
4-54
Protection and Control
BE1-951
Table 4-42. BF Breaker Failure Element Operating Settings
Setting
Range
Increment
Unit of
measure
Default
Time Delay
0 = disabled
50 to 999 ms
0.05 to 0.999 sec.
0 to 59.96 (60 Hz) or 0 to 49.97 (50 Hz)
1 m
0.1 sec
9
milliseconds
seconds
cycles
0
9
Time delays less than 10 cycles can be entered to the nearest 0.1 cycle from the front panel
HMI. All time delays can be entered to the nearest 0.01 cycle from the ASCII command interface.
Time delays entered in cycles are converted to milliseconds or seconds. Increment precision after
conversion is limited to that appropriate for each of those units of measure.
Breaker failure settings may be entered at HMI screen 5.5.1, or from the ASCII command interface using
the SP-BF (settings protection-breaker failure) command.
SP-BF Command
Purpose:
Read/Set the breaker failure timer setting
Syntax:
SP-BF[=<Time Delay>]
Comments: Time delay can be given in milliseconds(m), seconds(s), or cycles(c). Add the desired units
of measure behind the time delay value. See Table 4-42 for SP-BF settings information.
SP-BF Command Example
1.
Set BF time delay to 10 cycles
>SP-BF=10c
2.
Read the breaker failure time delay setting after setting it in example 1. (Nominal frequency is set to 60
hertz.)
>SP-BF
167m
Retrieving Logic Output Status Information From the Relay
The status of each logic variable can be determined from the ASCII command interface using the RG-STAT
(report general-status) or the RL (report logic) commands. See Section 6,
Reporting and Alarm Functions,
General Status Reporting for more information.
VIRTUAL SWITCHES
43 Virtual Selector Switches
BE1-951 Generator Protection Systems have four virtual selector switches that can provide manual control,
locally and remotely, without using physical switches and/or interposing relays. Each virtual switch can be
set for one of three modes of operation to emulate virtually any type of binary (two position) switch. An
example would be an application that requires a ground cutoff switch. The traditional approach might be to
install a switch on the panel and wire the output to a contact sensing input on the relay or in series with the
ground trip output of the relay. Instead, a virtual switch can be used to reduce costs with the added benefit
of being able to operate the switch both locally through the HMI and remotely from a substation computer
or through a modem connection to a remote operator’s console.
The state of the switches can be controlled from the optional HMI or ASCII command interface. Control
actions can be set by the BESTlogic mode setting. When set for Mode 1, each switch can be controlled to
open (logic 0), close (logic 1), or pulse such that the output toggles from its current state to the opposite state
and then returns. Additional modes allow the switch operation to be restricted. In Mode 2 (ON/OFF), the
switch emulates a two position selector switch, and only open and close commands are accepted. In Mode
3 (OFF/Momentary ON), a momentary close, spring return switch is emulated and only the pulse command