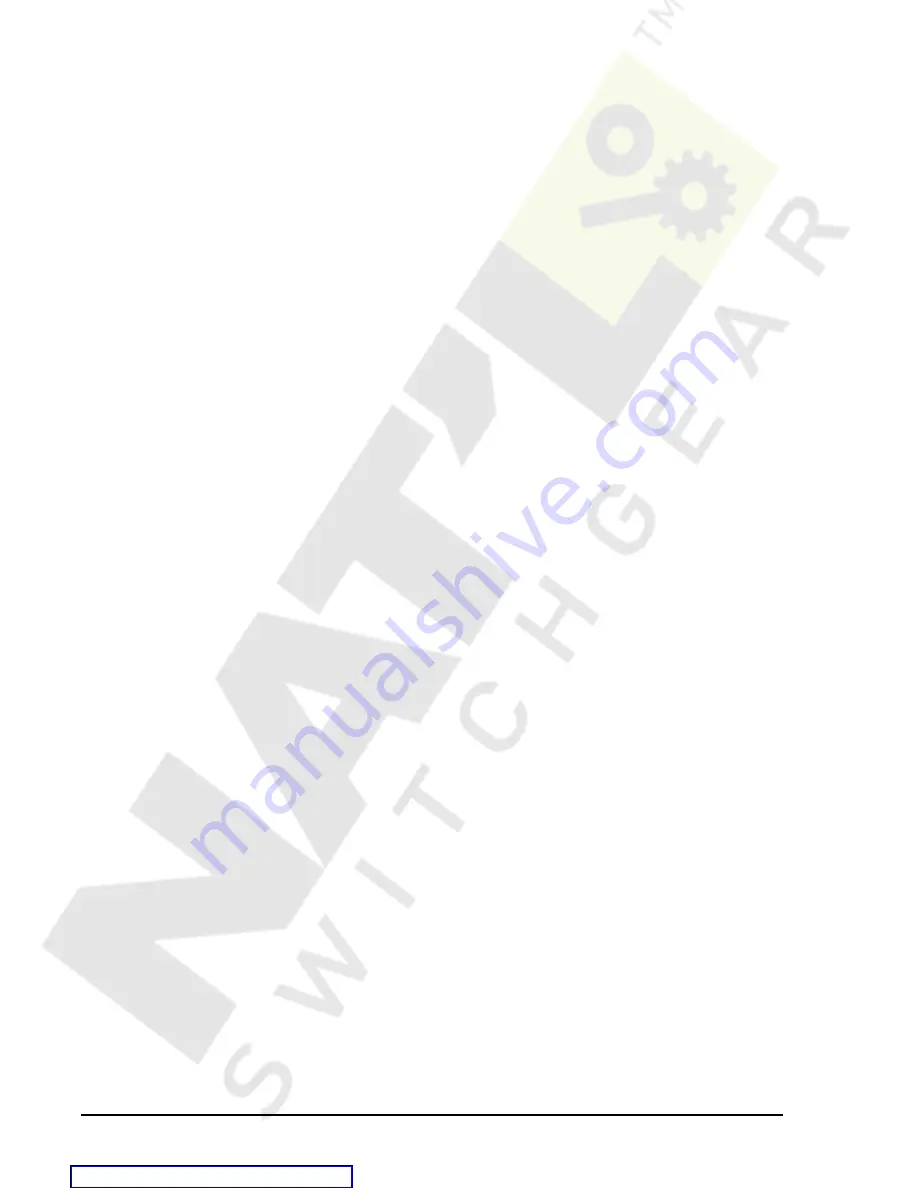
8-34
Application
BE1-951
Normal Operation - Control
The virtual breaker control switch (101) is programmed to provide manual trip and close control of the
breaker. Manual breaker control can be achieved by using the front panel HMI or by entering ASCII
commands through the communication ports. Control functions of this logic scheme use both traditional
contact sensing inputs and virtual switches. Virtual switches that are not needed may simply go unused. The
contact sensing inputs can be freed up for other uses by utilizing the virtual switches for other control
functions.
Normal Operation - Bus Protection
During normal operation, the primary task of the BUS relay is to provide high-speed fault protection (2 to 4
cycles coordination interval) and timed overload or high unbalanced load protection. The primary task of the
BACKUP relay is to provide the BUS relay with backup support for bus faults with an 18 to 20 cycle
coordination interval.
When any feeder relay overcurrent element is picked up and timing, OUT4 of the feeder relay closes. OUT4
is intended to be connected to IN2 of the upstream (primary) bus relay that is using BUS logic. When IN2
is energized, the bus relay 50T elements (2 to 4 cycle time delay) are blocked. If a fault occurs that is not
on a feeder, then the bus relay 50T elements are not blocked. The bus relay 50T function blocks are set up
close OUT4 which will trip the bus breaker by an external bus lockout relay (86B). Because the BACKUP
relay isn’t blocked when a feeder relay picks up, its 50T elements are set with a time delay long enough to
allow the feeder breaker to interrupt a fault. The BACKUP 50T elements are set up to trip the 86B relay via
OUTA. If a bus-fault lockout relay isn’t used, OUT4 can be wired in parallel with OUT1 to directly trip the bus
breaker. The BUS and BACKUP 50T functions should be set with a higher pickup than the highest feeder
instantaneous elements to ensure that they won’t pickup before any feeder relay.
If there is a contingency problem such as a relay removed from service, 51 protection is still provided. The
BUS and BACKUP 51 functions are enabled for tripping via OUT1. The 51 functions aren’t blocked to allow
clearing of a bus fault with a traditional coordination interval. When used to provide high-speed overcurrent
protection for the substation bus, it is recommended that all 51 function timing curves be set for
instantaneous reset.
Normal Operation - Setting Group Selection
For normal operation, the BUS and BACKUP relays use setting group 0. In setting group 0, the two relays
will only trip the bus breaker. IN2 of the BACKUP relay identifies when a feeder relay is out of service. the
BACKUP relay will close OUT3 which is connected to IN3 of the BUS relay. Both relays then switch to setting
group 1. Binary coded setting group selection (mode 2) is used to recognize the group setting state. When
input D0 of the setting group selection function block is a logic 1 (TRUE), it is interpreted as a binary 1 and
causes the logic to switch to group 1.
When in setting group 1, the relays are operating in feeder relay backup mode. This expression is
programmed to VO13 of the BUS relay which drives alarm bit 21 in the programmable alarm mask. Alarm
bit 21 can be masked to drive an alarm LED and alarm display screen to indicate when the BUS relay is in
feeder backup mode. It can also be used to trip a feeder breaker instead of the bus breaker.
More information about setting group operation is provided in the
Setting Group subsection of Section 4,
Protection and Control.
Normal Operation - Alarms
If the continuous self-test diagnostics of the relay detect an error, failsafe output contact OUTA will close and
the Relay Trouble LED of the HMI will light. OUTA will also close if relay operating power is lost. More
information about alarms is provided in Section 6,
Reporting and Alarm Functions.
Contingency Operation - Test Mode
The test mode is intended to increase the security of the protection and control system if external test
switches are not installed on all outputs.