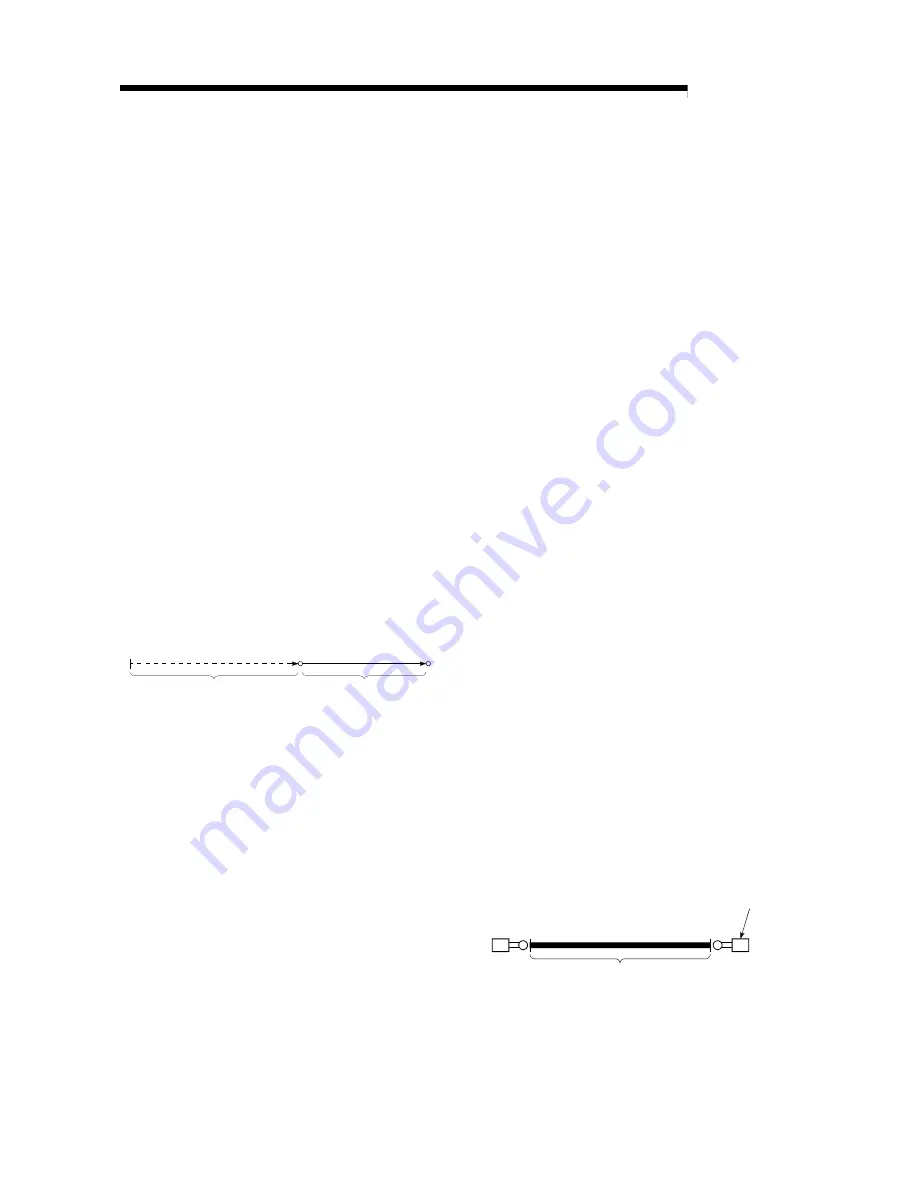
Appendix - 45
MELSEC-A
APPENDICES
SPEED LOOP GAIN
This is one item in the servo parameters of the
positioning data. It expresses the speed of the
control response during speed control. When
the load inertia moment ratio increases, the
control system speed response decreases and
the operation may become unstable. If this
happens, the operation can be improved by
raising this setting value.
The overshoot will become larger if the speed
loop gain is raised too far, and motor vibration
noise will occur during operation and when
stopped.
SPEED LOOP MODE
This is one servo control mode used in
positioning. It is a mode for carrying out speed
control. Refer to "POSITION LOOP MODE".
SPEED/POSITION CONTROL
CHANGEOVER MODE
This is one method used for positioning. It is
an application for operations such as high-
speed movement to a point unrelated to
positioning, then set dimension movement
from the changeover signal activation point.
Start
Changeover signal
High speed
Increment positioning
START COMPLETE
This signal gives an immediate response
notifying the user that the AD75 that was
started is now in a normal state and can start
positioning.
STARTING AXIS
One of the AD75 axis system axes (axis 1,
axis 2, or axis 3) or the reference axis for the
interpolation operation is designated as the
starting axis.
STATUS
Data showing the state of the machine.
Collectively refers to signals that turn ON when
the battery voltage drops, during zero point
requests, during dwell time, etc.
STEP FUNCTION
When the operation is designed so that
several positioning data Nos. are
consecutively run, this function can be used to
carry out a test operation for 1 data item at a
time.
STOP SETTLING TIME
Refer to the term "DWELL TIME".
STOP SIGNAL
In positioning control, this is the input signal X
that directly stops the operation from an
external source.
The operation stops when the external STOP
signal (a contact) turns ON (continuity), and X
turns ON.
STROKE
The stroke is the variation in the operation by
the distance from a stopped state to the next
stopped state after a movement.
STROKE LIMIT
This is the range in which a positioning
operation is possible, or the range in which the
machine can be moved without damage
occurring.
For operations using a worm gear, the stroke
limit is determined by the length of the screw.
For operations using a fixed-dimension feed, it
is determined by the max. dimension to be cut.
The upper and lower limits are set in the
parameters, but a separate limit switch should
be established and an emergency stop circuit
outside the PLC should be created. Refer to
the term "LIMIT SWITCH".
Lower limit
0
Upper limit
3m
Limit switch
for emergency
stop
Positioning possible in a 3m range
Содержание A1SD75M1
Страница 2: ......
Страница 20: ...A 18 MEMO...
Страница 22: ...MEMO...
Страница 27: ...1 5 MELSEC A 1 PRODUCT OUTLINE MEMO...
Страница 42: ...1 20 MELSEC A 1 PRODUCT OUTLINE MEMO...
Страница 52: ...2 10 MELSEC A 2 SYSTEM CONFIGURATION MEMO...
Страница 111: ...5 21 MELSEC A 5 DATA USED FOR POSITIONING CONTROL MEMO...
Страница 115: ...5 25 MELSEC A 5 DATA USED FOR POSITIONING CONTROL MEMO...
Страница 123: ...5 33 MELSEC A 5 DATA USED FOR POSITIONING CONTROL MEMO...
Страница 127: ...5 37 MELSEC A 5 DATA USED FOR POSITIONING CONTROL MEMO...
Страница 167: ...5 77 MELSEC A 5 DATA USED FOR POSITIONING CONTROL MEMO...
Страница 193: ...5 103 MELSEC A 5 DATA USED FOR POSITIONING CONTROL MEMO...
Страница 276: ...5 186 MELSEC A 5 DATA USED FOR POSITIONING CONTROL MEMO...
Страница 332: ...7 18 MELSEC A 7 MEMORY CONFIGURATION AND DATA PROCESS MEMO...
Страница 334: ...MEMO...
Страница 422: ...9 64 MELSEC A 9 MAIN POSITIONING CONTROL MEMO...
Страница 446: ...10 24 MELSEC A 10 ADVANCED POSITIONING CONTROL MEMO...
Страница 472: ...11 26 MELSEC A 11 MANUAL CONTROL MEMO...
Страница 576: ...12 104 MELSEC A 12 CONTROL AUXILIARY FUNCTIONS MEMO...
Страница 673: ...Appendix 5 MELSEC A APPENDICES Axis address mm inch degree pulse Axis address mm inch degree pulse...
Страница 679: ...Appendix 11 MELSEC A APPENDICES Initial value Axis 1 Axis 2 Axis 3 Remarks 0 0 0 1 1 0 0 0 0 0 300 0 0 0...
Страница 683: ...Appendix 15 MELSEC A APPENDICES Initial value Axis 1 Axis 2 Axis 3 Remarks 0 0 1 0 0 50 80 0 0 980...
Страница 691: ...Appendix 23 MELSEC A APPENDICES Initial value Axis 1 Axis 2 Axis 3 Remarks 0 0 0 0 0 50 80 0 0 0 0 0 980 4000 0...
Страница 745: ......