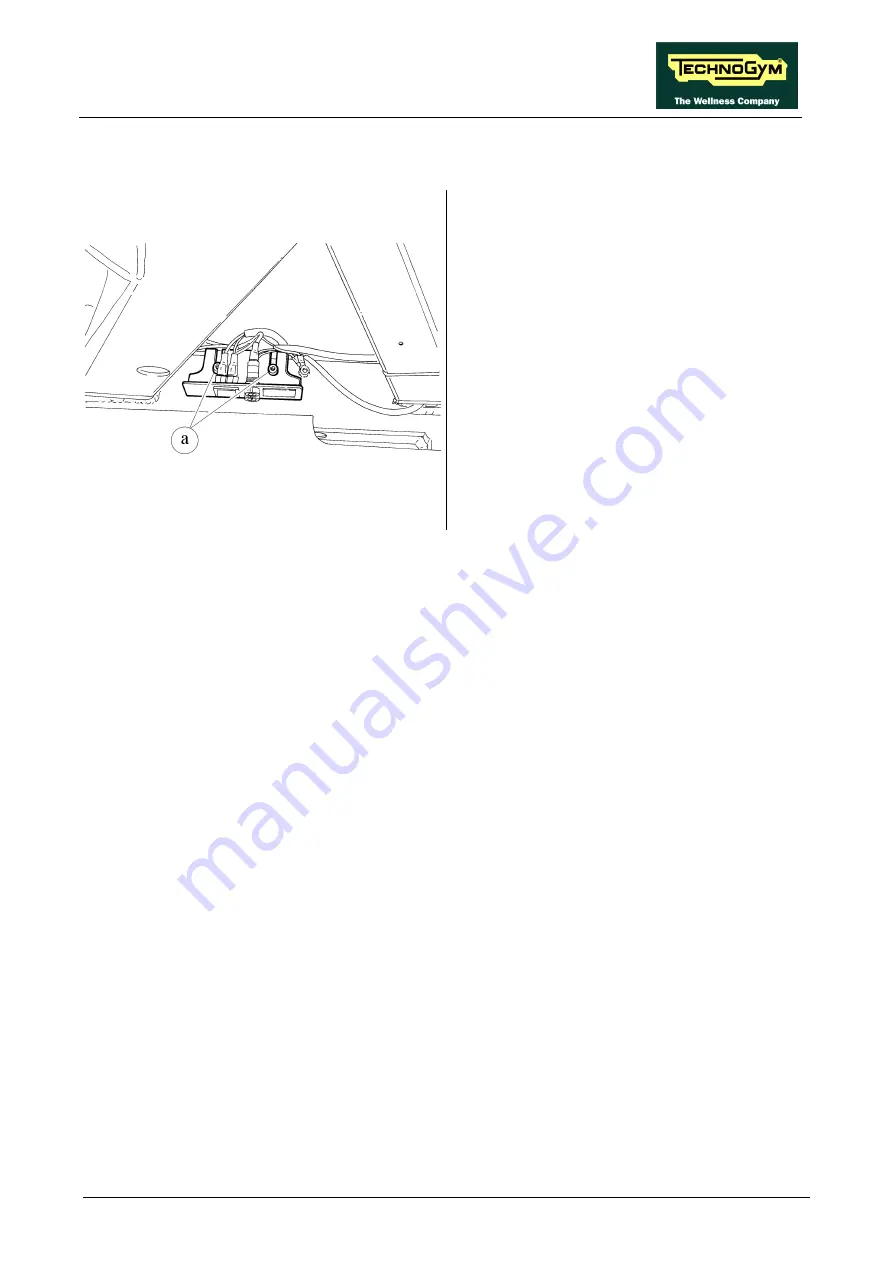
BIOSTRENGTH LINE: Service & Maintenance manual - rev. 2.1
Page 7.211
7.5.39. D
ISASSEMBLING THE STARTER PLATE AND FUSES
Figure 7.5.39-1
Follow the steps described in paragraphs 7.5.7.
“Removing the seat”, 7.5.8. “Disassembling the
front guard” and 7.5.11. “Disassembling the
upright guard”.
1. Loosen the 2 screws
a
using a 5-gauge
hexagonal T-wrench.
2. Remove the STARTING PLATE AND
FUSES, being careful not to tear the cables.
3. The PLATE is thus available for any
necessary operations.
To replace the STARTING PLATE AND
FUSES, follow the above steps in reverse order.
Summary of Contents for BIOSTRENGTH LINE
Page 1: ...SERVICE MAINTENANCE MANUAL REV 2 1...
Page 2: ......
Page 4: ......
Page 16: ...BIOSTRENGTH LINE Service Maintenance manual rev 2 1 Page xii Page intentionally left blank...
Page 88: ...BIOSTRENGTH LINE Service Maintenance manual rev 2 1 Page 2 70 Page intentionally left blank...
Page 99: ...BIOSTRENGTH LINE Service Maintenance manual rev 2 1 Page 3 11 Figure 3 2 5...
Page 122: ...BIOSTRENGTH LINE Service Maintenance manual rev 2 1 Page 4 2 Page intentionally left blank...
Page 634: ...BIOSTRENGTH LINE Service Maintenance manual rev 2 1 Page 9 26 Page intentionally left blank...
Page 645: ......