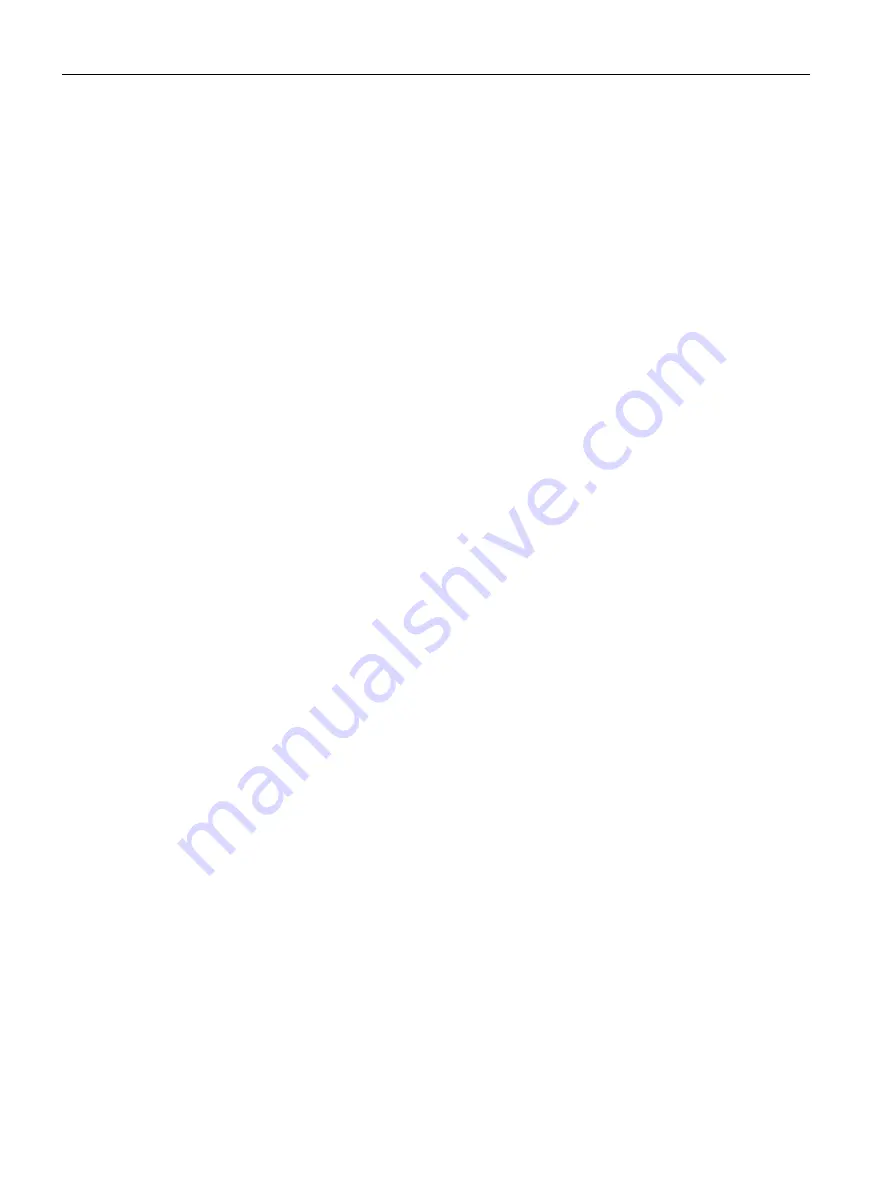
Functions, monitoring and protective functions
9.4 Extended functions
Enclosed Drives
622
Operating Instructions, 12/2018, A5E36652151A
Example 1: Starting against a closed brake
When the device is switched on, the setpoint is enabled immediately (if other enable signals
are issued), even if the brake has not yet been released (p1152 = 1). The factory setting
p1152 = r0899.15 must be separated here. The drive first establishes a torque against the
applied brake. The brake is not released until the motor torque or current (p1220) has
exceeded braking threshold 1 (p1221).
Depending on the type and design of the brake, the time required to completely release the
brake differs. It must be taken into consideration that, once the braking threshold torque has
been exceeded, the operation enable signal (p0899.2) is interrupted for the time interval that
the brake is being released (p1216) to ensure that the motor current does not exceed the
permissible limit values during this period and the motor torque generated does not damage
the brake. Time interval p1216 must be set depending on the time the brake actually
requires to release.
This configuration is used, for example, when the drive is connected to a belt that is under
tension (loop accumulator in the steel industry).
Example 2: Emergency brake
If emergency braking is required, electrical and mechanical braking is to take place
simultaneously. This can be achieved if OFF3 is used as a tripping signal for emergency
braking:
p1219[0] = r0898.2 and p1275.00 = 1 (OFF3 to "apply brake immediately" and invert signal).
To prevent the converter working in opposition to the brake, the OFF3 ramp (p1135) should
be set to 0 seconds. Regenerative energy may accumulate, and this must be either fed back
into the supply system or converted into heat using a braking resistor.
Typical applications include calenders, cutting tools, travel units and presses, for example.
Example 3: Service brake on crane drives
For cranes with manual control, it is important that the drive responds immediately when the
control lever is moved (master switch). To this end, the drive is powered up using the on
command (p0840) (the pulses are enabled). Speed setpoint (p1142) and speed controller
(p0856) are inhibited. The motor is magnetized. As a consequence, the magnetization time
generally applicable for three-phase motors (1 - 2s) is eliminated.
Now, only the brake opening time will delay the motor starting to rotate following activation of
the master switch. Movement of the master switch generates a "setpoint enable from the
control" (bit interconnected with p1142, p1229.2, p1224.0). The speed controller is enabled
immediately and the speed setpoint is enabled once the brake opening time (p1216) has
elapsed. When the master switch is in the zero position, the speed setpoint is inhibited and
the drive ramps down along the ramp-function generator's ramp-down ramp. The brake
closes once the standstill limit (p1226) is undershot. Once the brake closing time (p1217)
has elapsed, the speed controller is inhibited (the motor is no longer generating any force).
Extended braking control is used with the modifications described below.
Summary of Contents for SINAMICS S150 NEMA
Page 1: ......
Page 2: ......
Page 20: ...Table of contents Enclosed Drives 18 Operating Instructions 12 2018 A5E36652151A ...
Page 861: ......
Page 862: ......