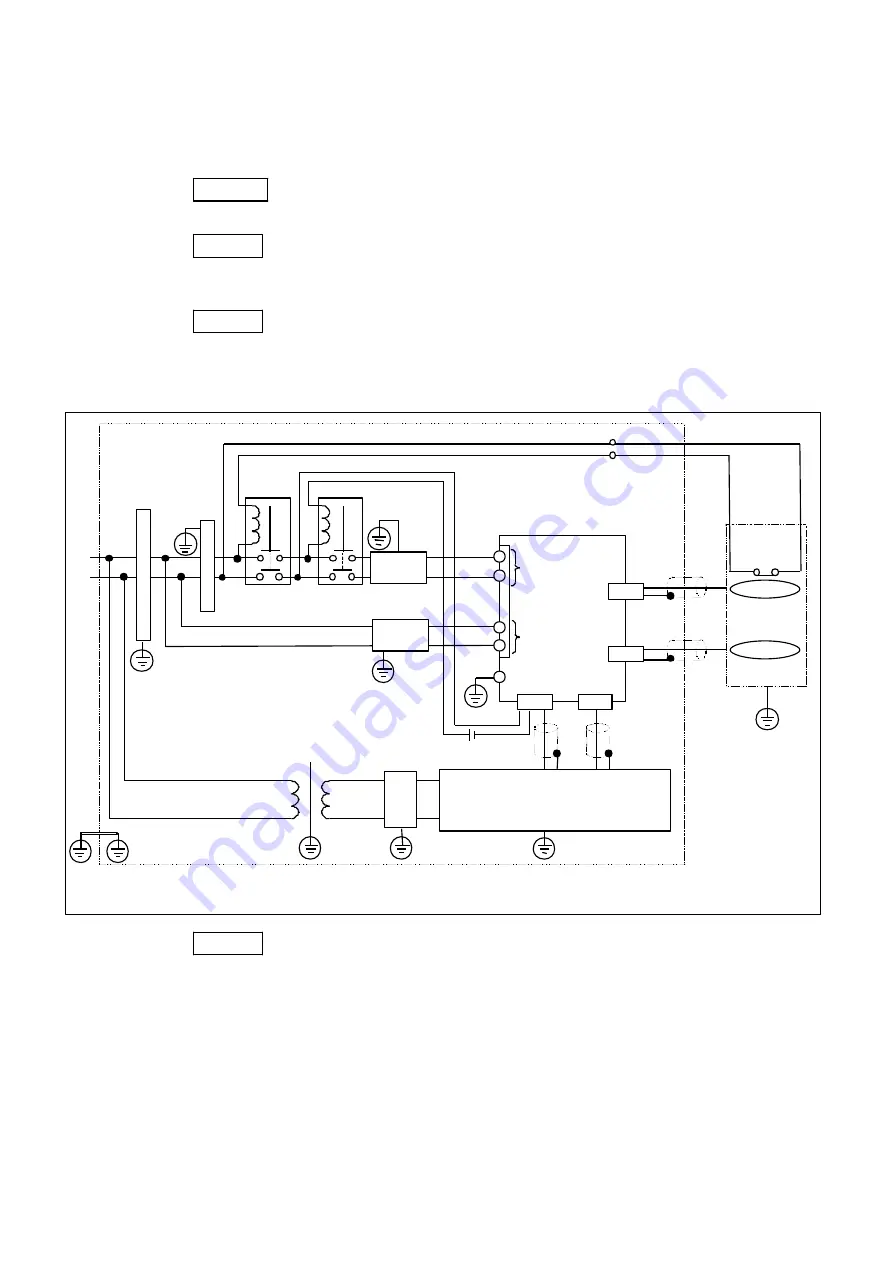
— 6-11 —
6.4.2. Ground Connection and Wiring
l
For grounding Driver Unit, use heavy gage cable as possible, such as a flat braided copper cable or
a wire 3.5mm
2
(AWG 10) or larger.
Warning : All the ground lines must be connected at one point and the grounding
resistance must be under or equal to 100
Ω
.
Caution : Connect the shield of the signal shielded cable (CN2) to the FG terminals (or
SG terminals) of the master controller. If runaways are caused by noise,
connect the shield to the FG terminal of the Driver Unit.
Caution : Make sure to earth the Motor base when it is isolated from the machine base.
l
Figure 6-8 shows the wiring example. (This is provided as an example, not the instruction.)
Figure 6-8 : Wiring Example
Noise
filter
Magnet
switch
Driver Unit
AC
p
ower
Ground earth
(Class 3 or better)
Noise
filter
Noise
filter
Circuit
b
reaker
FG
Ground the Motor
base using bolts.
Control power
Main power
CN4
CN3
200V : 100V
Motor
Motor
Resolver
Isolation
transformer
CN2
User controller
• Position controller (Pulse train output)
• Sequencer
• DC24V power source
Thermal sensor
(Normally closed)
Magnet
switch
S1
S2
DRDY-
DRDY+
DC24V
∗
Connect at one point.
∗
∗
∗
∗
∗
∗
∗
∗
∗
∗
∗
CN5
Caution : • We recommend to use the noise filter listed below as the measures for EMC
Directive.
Single phase 200V : Equivalent to FN2070-10
(Shaffner EMC Ltd.)
Single phase 100V : Equivalent to FN2070-16
(Shaffner EMC Ltd.)
3 phase 200V
: Equivalent to FN358-16
(Shaffner EMC Ltd.)
• The isolation transformer and the circuit breaker shall conform to the
relevant European safety regulations.
Artisan Technology Group - Quality Instrumentation ... Guaranteed | (888) 88-SOURCE | www.artisantg.com