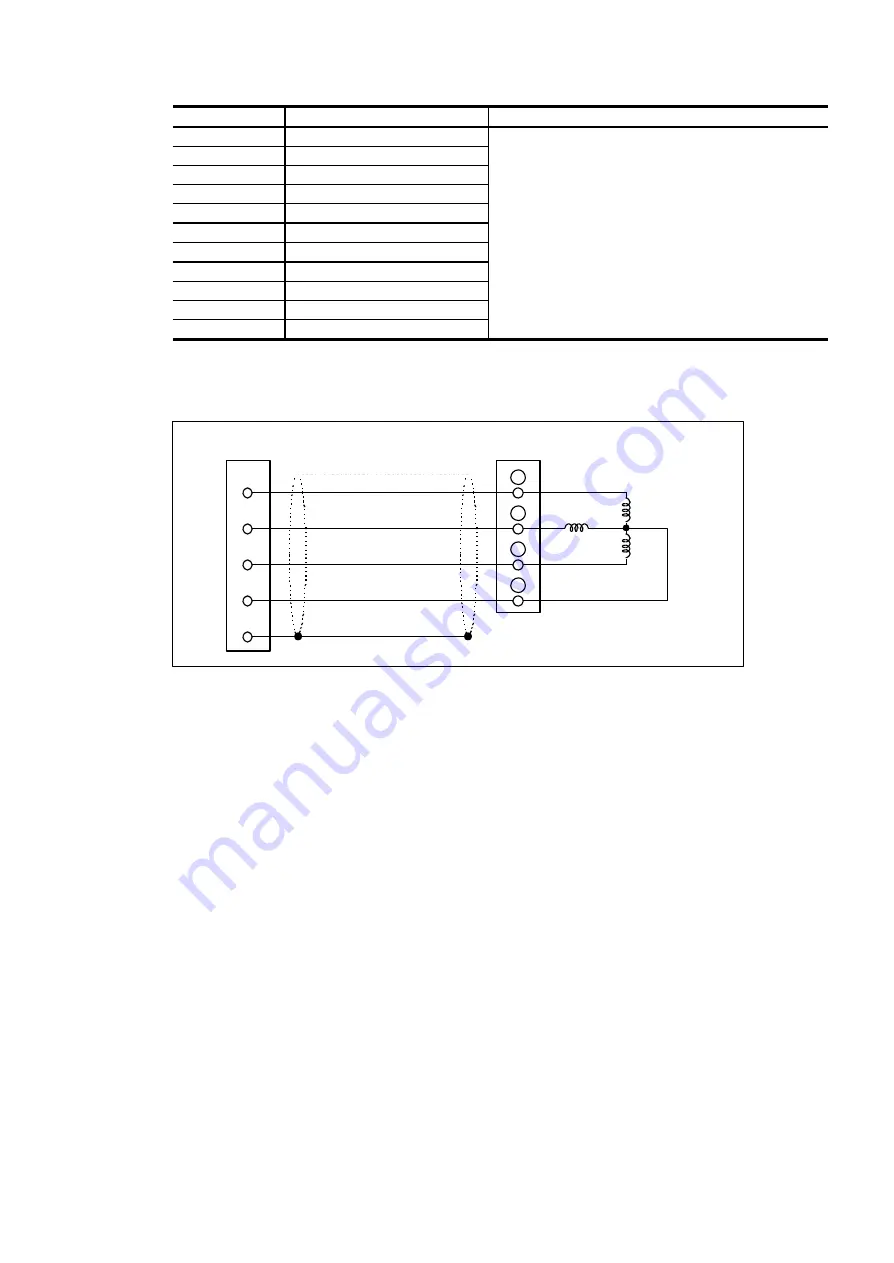
— A-7 —
Table A-6: Specifications of resolver resistance
Motor number
Motor winding resistance (
Ω
)
Specification
YS2005
3.8
YS2020
3.8
YS3008
3.7
YS3040
3.7
YS4080
2.8
YS5120
2.6
YS5240
2.6
JS0002
2.3
JS1003
2.6
JS2006
3.9
JS2014
3.8
1. Allowance
: ±30%
2. Variations between each phase
: 1.0
Ω
or less
(øA, øB, øC)
l
For special Motor windings or long cable (over 4m), contact NSK for specification.
Figure A-9: Resolver wiring (For your reference)
REA (Red)
REB (White)
REC (Black)
Common (Green)
FG (Shielded)
8
7
15
4
10
D-Sub Connector
Phase C
Phase B
Phase A
Common
Motor Connector
1
2
6
11
Artisan Technology Group - Quality Instrumentation ... Guaranteed | (888) 88-SOURCE | www.artisantg.com