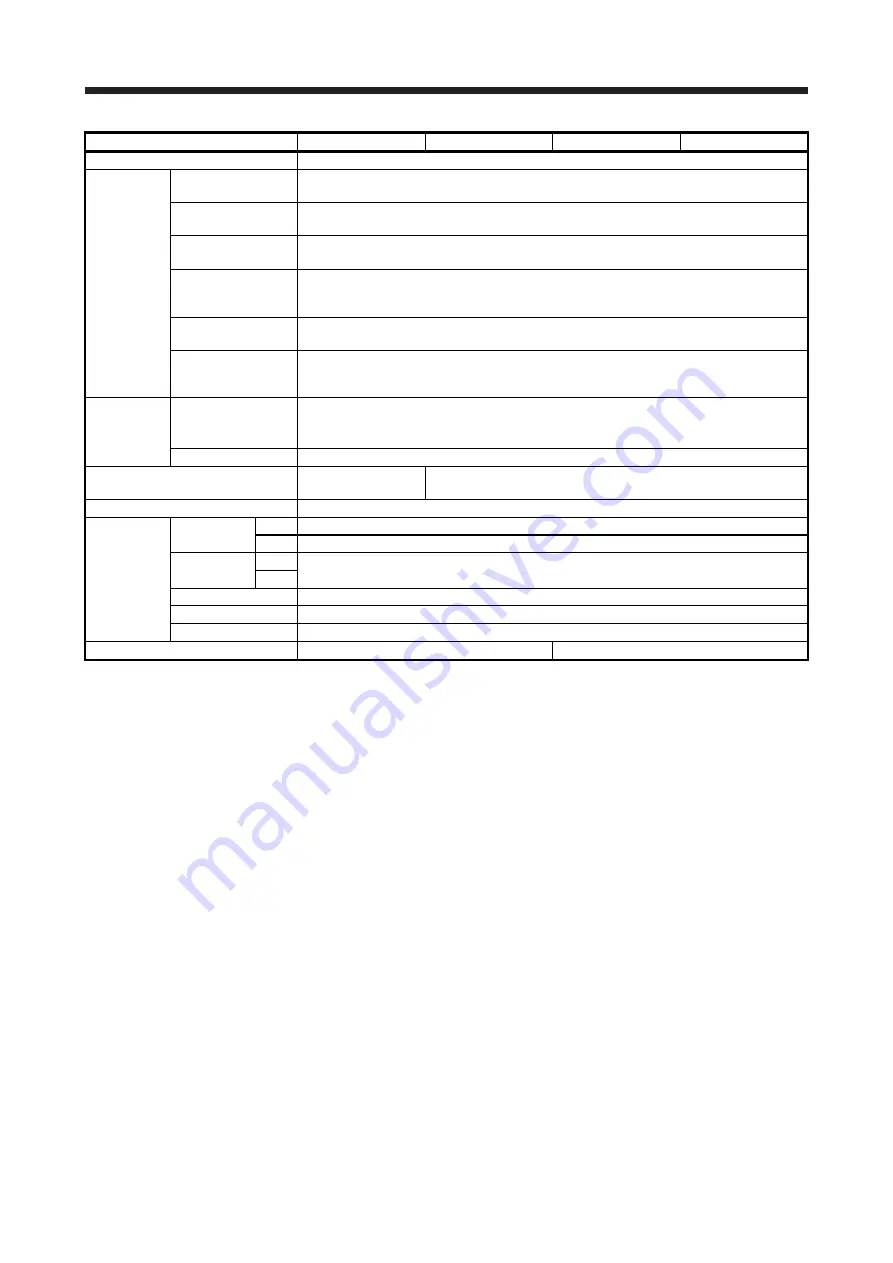
1. FUNCTIONS AND CONFIGURATION
1 - 5
Model MR-J4W2-
22B
44B
77B
1010B
Functional safety
STO (IEC/EN 61800-5-2) (Note 7)
Safety
performance
Standards certified by
CB
EN ISO 13849-1 PL d (category 3), IEC 61508 SIL 2, EN 62061 SIL CL2
Response
performance
8 ms or less (STO input off
→
energy shut off)
(Note 5) Test pulse
input (STO)
Test pulse interval: 1 Hz to 25 Hz
Test pulse off time: Up to 1 ms
Mean time to
dangerous failure
(MTTFd)
100 years or longer
Diagnosis converge
(DC)
Medium (90% to 99%)
Average probability of
dangerous failures
per hour (PFH)
1.68 × 10
-10
[1/h]
Compliance
to standards
CE marking
LVD: EN 61800-5-1
EMC: EN 61800-3
MD: EN ISO 13849-1, EN 61800-5-2, EN 62061
UL standard
UL 508C
Structure (IP rating)
Natural cooling, open
(IP20)
Force cooling, open (IP20)
Close mounting
Possible
Ambient
temperature
Operation
0 °C to 55 °C (non-freezing)
Storage
-20 °C to 65 °C (non-freezing)
Environment
Ambient
humidity
Operation
90% RH or less (non-condensing)
Storage
Ambience
Indoors (no direct sunlight), free from corrosive gas, flammable gas, oil mist, dust, and dirt
Altitude
Max. 1000 m above sea level
Vibration
5.9
m/s
2
or less at 10 Hz to 55 Hz (directions of X, Y and Z axes)
Mass
[kg]
1.5
2.0
Note 1. 0.35 A is the value applicable when all I/O signals are used. The current capacity can be decreased by reducing the number of
I/O points.
2. Reusable regenerative energy corresponds to energy generated under the following conditions.
Rotary servo motor: Regenerative energy is generated when the machine, whose moment of inertia is equivalent to the
permissible charging amount, decelerates from the rated speed to stop.
Linear servo motor: Regenerative energy is generated when the machine, whose mass is equivalent to the permissible
charging amount, decelerates from the maximum speed to stop.
Direct drive motor: Regenerative energy is generated when the machine, whose moment of inertia is equivalent to the
permissible charging amount, decelerates from the rated speed to stop.
3. Moment of inertia when the motor decelerates from the rated speed to stop
Moment of inertia for two axes when two motors decelerate simultaneously
Moment of inertia for each axis when multiple motors do not decelerate simultaneously
The values also apply to the direct drive motor.
4. Mass when the machine decelerates from the maximum speed to stop
The primary-side (coil) mass is included.
Mass for two axes when two motors decelerate simultaneously
Mass for each axis when multiple motors do not decelerate simultaneously
5. Test pulse is a signal which instantaneously turns off a signal to the servo amplifier at a constant period for external circuit to
self-diagnose.
6. The load-side encoder is compatible only with two-wire type communication method. Not compatible with pulse train interface
(A/B/Z-phase differential output type).
7. STO is common for all axes.
8. Fully closed loop control is compatible with the servo amplifiers with software version A3 or later.
Check the software version of the servo amplifier using MR Configurator2.
9. The command communication cycle depends on the controller specifications and the number of axes connected.
10. The scale measurement function is available for the MR-J4W2-_B servo amplifiers of software version A8 or later. Check the
software version of the servo amplifier using MR Configurator2.
11. This value is applicable when a 3-phase power supply is used.
Summary of Contents for MR-J4W2
Page 9: ...A 8 MEMO ...
Page 17: ...8 MEMO ...
Page 31: ...1 FUNCTIONS AND CONFIGURATION 1 14 MEMO ...
Page 95: ...4 STARTUP 4 20 MEMO ...
Page 169: ...6 NORMAL GAIN ADJUSTMENT 6 20 MEMO ...
Page 201: ...7 SPECIAL ADJUSTMENT FUNCTIONS 7 32 MEMO ...
Page 213: ...8 TROUBLESHOOTING 8 12 MEMO ...
Page 219: ...9 OUTLINE DRAWINGS 9 6 MEMO ...
Page 229: ...10 CHARACTERISTICS 10 10 MEMO ...
Page 295: ...13 USING STO FUNCTION 13 14 MEMO ...
Page 327: ...14 USING A LINEAR SERVO MOTOR 14 32 MEMO ...
Page 371: ...16 FULLY CLOSED LOOP SYSTEM 16 24 MEMO ...
Page 521: ...APPENDIX App 38 ...
Page 537: ...MEMO ...
Page 541: ......