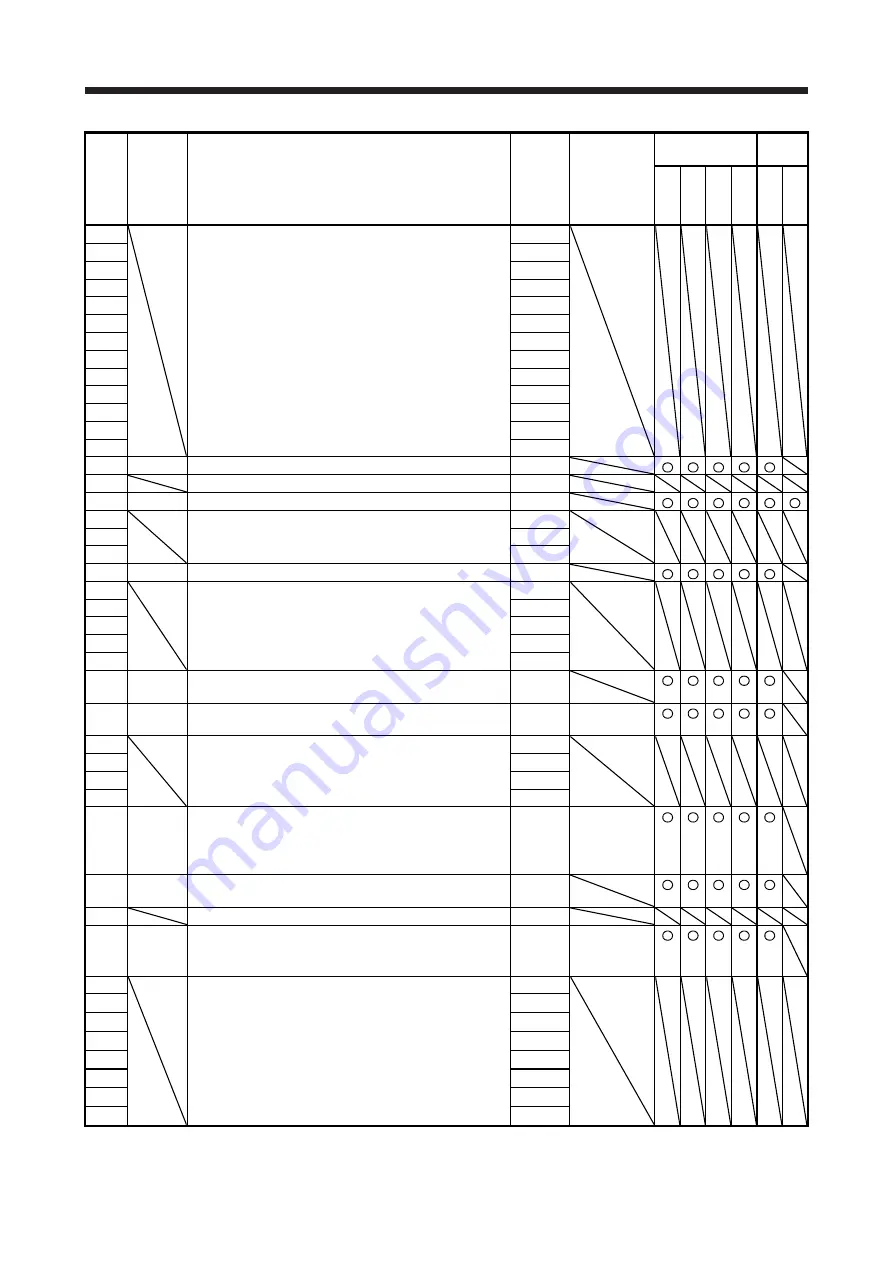
9. MANUFACTURER FUNCTIONS
9 - 18
No. Symbol
Name
Initial
value
Unit
Operation mode
Control
mode
Standard
F
ull.
Lin.
DD
pt
idx
17
For manufacturer setting
0
18
0
19
0
20
0
21
0
22
0
23
0
24
0
25
0
26
0
27
0
28
0
29
0
30
*MAX
Main shaft input axis selection
0
31
For
manufacturer
setting
0
32
MMIX
Main shaft input method
0000h
33
For manufacturer setting
0
34
0
35
0
36
CLTMD Main shaft clutch control setting
0000h
37
For manufacturer setting
0
38
0
39
0
40
0
41
0
42 CLTSMM
(Note)
Main shaft clutch smoothing system
0
43 CLTSMT
(Note)
Main shaft clutch smoothing time constant
0
[ms]
44
For manufacturer setting
0
45
0
46
0000h
47
0
48 CCYL
(Note)
Cam axis length per cycle
0
[µm]/
10
-4
[inch]/
10
-3
[degree]/
[pulse]
49 CNO
(Note)
Cam No.
0
50
For
manufacturer
setting
0
51 CSTK
(Note)
Cam stroke amount
0
[µm]/
10
-4
[inch]/
[pulse]
52
For manufacturer setting
0
53
0
54
0
55
0
56
0
57
0
58
0
59
0
Summary of Contents for MR-J4-_GF
Page 27: ...2 CC Link IE FIELD NETWORK BASIC PROTOCOL 2 4 MEMO ...
Page 185: ...8 TROUBLESHOOTING AT POWER ON 8 2 MEMO ...
Page 227: ...9 MANUFACTURER FUNCTIONS 9 42 MEMO ...
Page 269: ...10 OBJECT DICTIONARY 10 42 MEMO ...
Page 271: ...MEMO ...