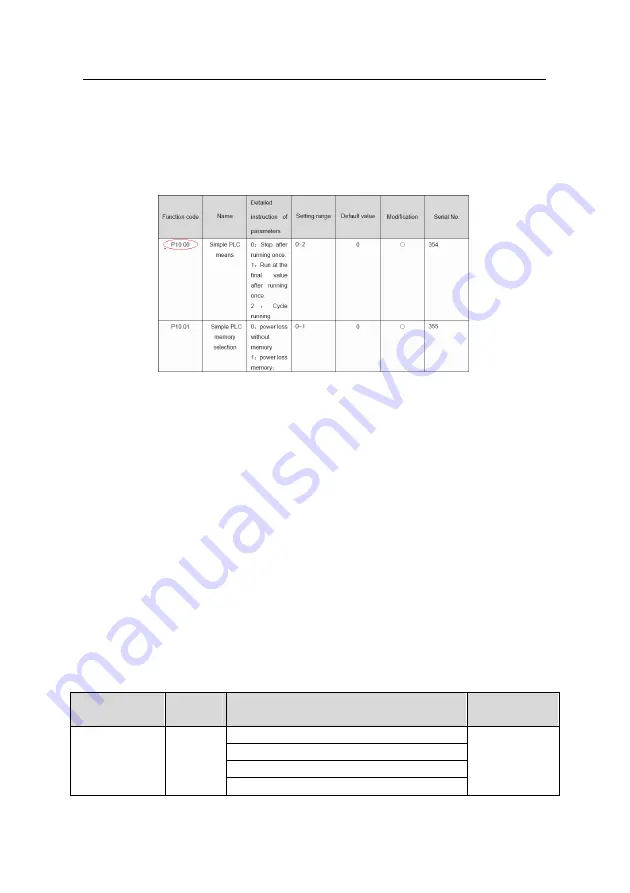
Goodrive300
inverters Communication protocol
248
low byte is the number after the radix point. But both the high byte and the low byte should
be changed into hex. For example P05.06, the group number before the radix point of the
function code is 05, then the high bit of the parameter is 05, the number after the radix point
06, then the low bit of the parameter is 06, then t he function code address is 0506H and the
parameter address of P10.01 is 0A01H.
Note: PE group is the factory parameter which can not be read or changed. Some
parameters can not be changed when the inverter is in the running state and some
parameters can not be changed in any state. The setting range, unit and relative instructions
should be paid attention to when modifying the function code parameters.
Besides, EEPROM is stocked frequently, which may shorten the usage time of EEPROM.
For users, some functions are not necessary to be stocked on the communication mode.
The needs can be met on by changing the value in RAM. Changing the high bit of the
function code form 0 to 1 can also realize the function. For example, the function code
P00.07 is not stocked into EEPROM. Only by changing the value in RAM can set the
address to 8007H. This address can only be used in writing RAM other than reading. If it is
used to read, it is an invalid address.
10.4.1.2 The address instruction of other function in Modbus
The master can operate on the parameters of the inverter as well as control the inverter,
such as running or stopping and monitoring the working state of the inverter.
Below is the parameter list of other functions
Function
instruction
Address
definition
Data meaning instruction
R/W
characteristics
0001H:forward running
0002H:reverse running
0003H:forward jogging
Communication
control command
2000H
0004H:reverse jogging
W/R
Summary of Contents for GD300-004G-4
Page 1: ...3...
Page 148: ...Goodrive300 inverters Basic operation instruction 147...
Page 159: ...Goodrive300 inverters Basic operation instruction 158...
Page 164: ...Goodrive300 inverters Basic operation instruction 163...
Page 173: ...Goodrive300 inverters Basic operation instruction 172...
Page 189: ...Goodrive300 inverters Basic operation instruction 188...
Page 204: ...Goodrive300 inverters Basic operation instruction 203...
Page 227: ...Goodrive300 inverters Fault tracking 226 8 6 2 Motor vibration...
Page 228: ...Goodrive300 inverters Fault tracking 227 8 6 3 Overvoltage 8 6 4 Undervoltage fault...
Page 312: ...1 1 0 0 1 0 0 7 7 9 C E 66001 00035 201303 V1 4...