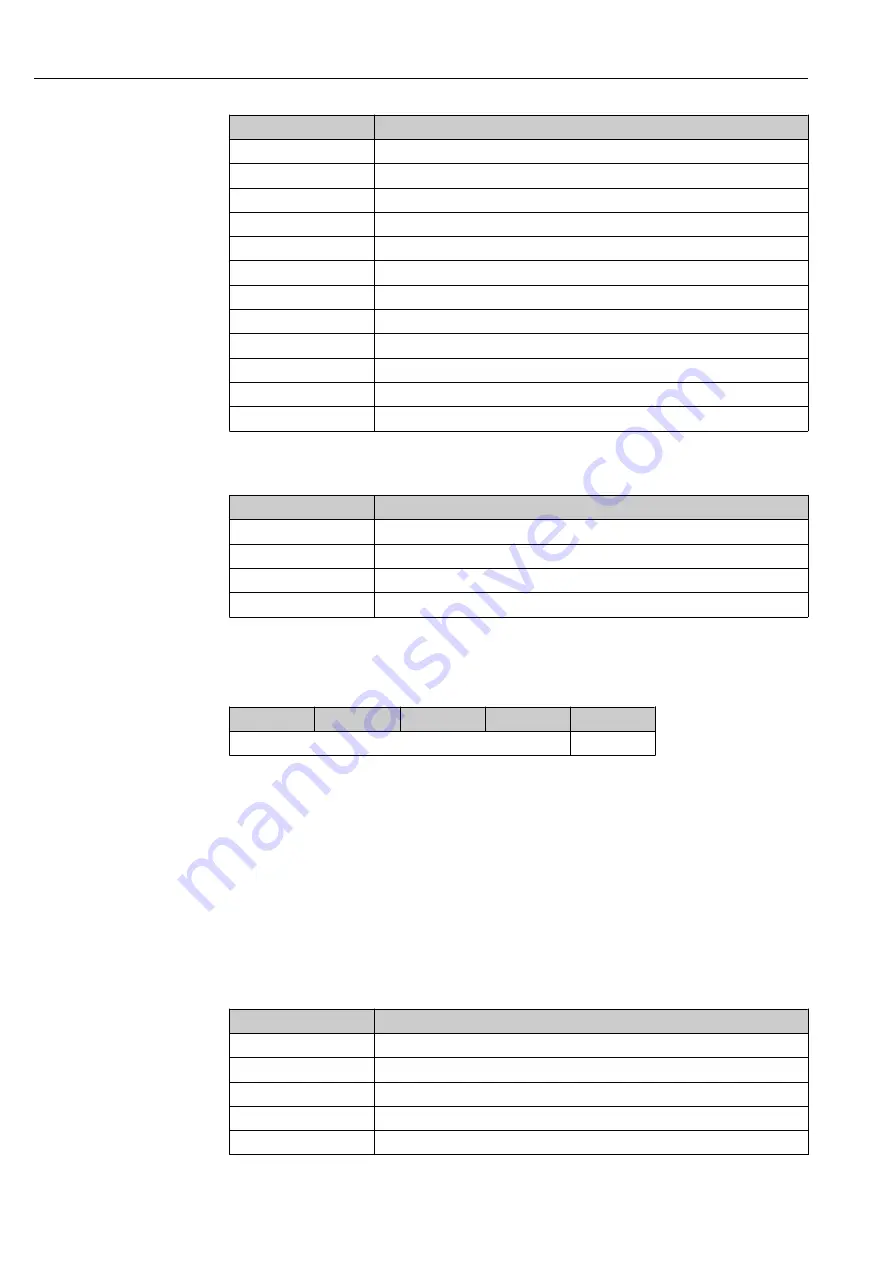
System integration
Proline Prowirl F 200 PROFIBUS PA
64
Hauser
Channel
Input variable
13
Corrected volume flow
14
Density
22
Pressure
37
Flow velocity
38
Energy flow
45
Calculated saturated steam pressure
46
Total mass flow
48
Steam quality
49
Heat flow difference
50
Reynolds number
51
Specific volume
52
Degree of overheating
Factory setting
Function block
Factory setting
AI 1
Volume flow
AI 2
Mass flow
AI 3
Corrected volume flow
AI 4
Density
Data structure
Input data of Analog Input
Byte 1
Byte 2
Byte 3
Byte 4
Byte 5
Measured value: floating point number (IEEE 754)
Status
TOTAL module
Transmit a totalizer value from the measuring device to the PROFIBUS master (Class 1).
A selected totalizer value, along with the status, is cyclically transmitted to a PROFIBUS
Master (Class 1) via the TOTAL module. The totalizer value is depicted in the first four
bytes in the form of a floating point number as per the IEEE 754 standard. The fifth byte
contains standardized status information pertaining to the totalizer value.
Three Totalizer blocks are available (slot 5 to 7).
Selection: totalizer value
The totalizer value can be specified using the CHANNEL parameter.
Channel
Input variable
9
Volume flow
11
Mass flow
13
Corrected volume flow
38
Energy flow
46
Total mass flow
Summary of Contents for Proline Prowirl F 200
Page 224: ...www addresses endress com...