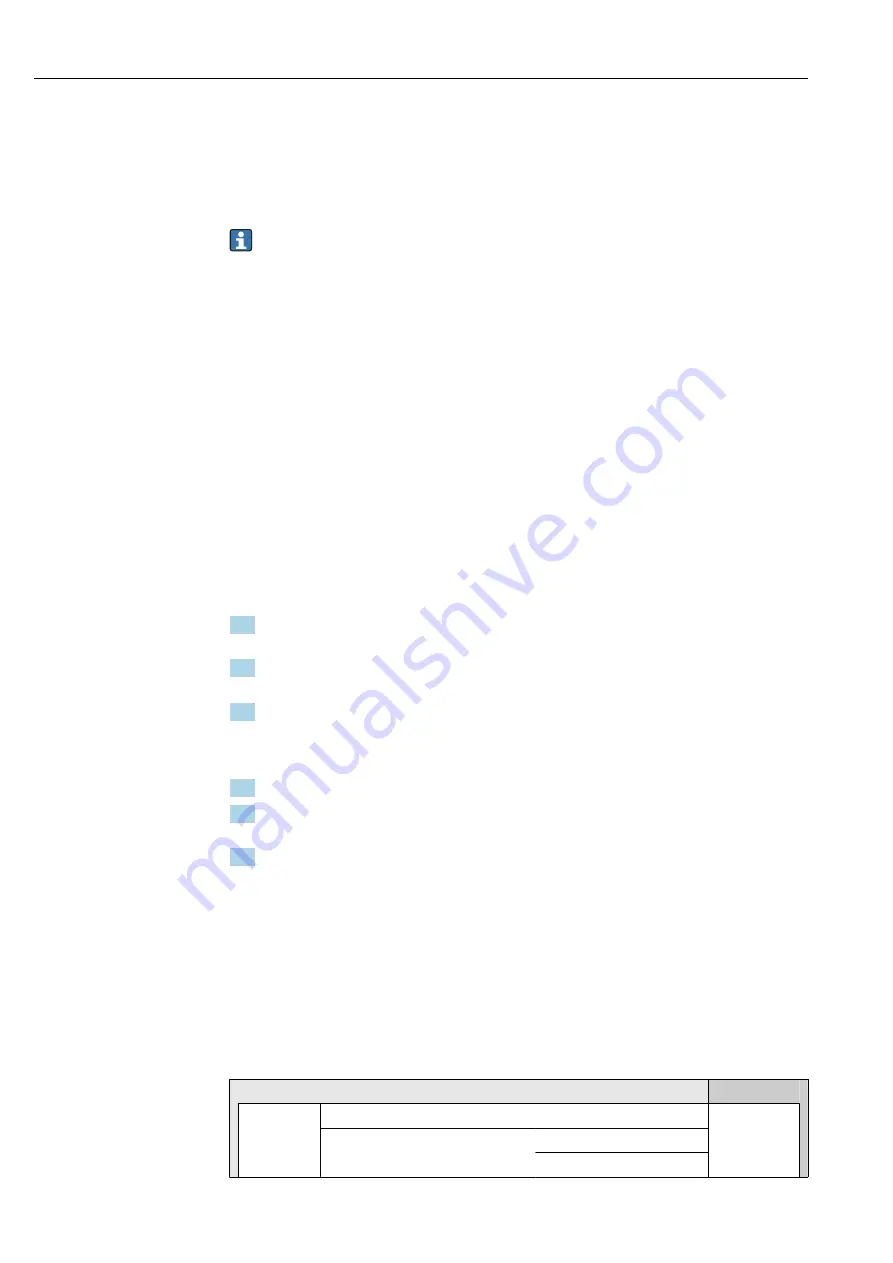
System integration
Proline Prowirl F 200 PROFIBUS PA
62
Hauser
Manual setting
The manual setting is made in the
Ident number selector
parameter via the option
Prowirl 72 (0x153B) or Prowirl 73 (0x153C).
Afterwards, the Prowirl 200 PROFIBUS PA makes the same input and output data and
measured status information available for cyclic data exchange.
• If the Prowirl 200 PROFIBUS PA is acyclically configured via an operating program
(Class 2 master), access is directly via the block structure or the parameters of the
measuring device.
• If parameters have been changed in the device to be replaced (Prowirl 72 PROFIBUS
PA or Prowirl 73 PROFIBUS PA) (parameter setting no longer corresponds to the
original factory setting), these parameters must be changed accordingly in the new
replacement Prowirl 200 PROFIBUS PA via an operating program (Class 2 master).
Example
The setting for low flow cut off has been changed from mass flow (factory setting)
to corrected volume flow in a Prowirl 72 PROFIBUS PA currently in operation. This
device is now replaced by a Prowirl 200 PROFIBUS PA device. After replacing the
device, the assignment for the low flow cut off must be changed manually in the
Prowirl 200 PROFIBUS, i.e. to corrected volume flow, to ensure the measuring
device behaves identically.
Replacing the measuring devices without changing the GSD file or restarting the
controller
In the procedure described below, the device can be replaced without interrupting ongoing
operation or restarting the controller. However with this procedure the measuring device is
not fully integrated!
1. Replace the measuring device Prowirl 72 or 73 PROFIBUS PA by a Prowirl 200
PROFIBUS PA device.
2. Set the device address: The same device address that was set for the Prowirl 72,
Prowirl 73 or PROFIBUS PA Profile GSD must be used.
3. Connect the Prowirl 200 PROFIBUS PA.
If the factory setting had been changed on the replaced device (Prowirl 72 or Prowirl 73),
the following settings may need to be changed:
1. Configuration of the application-specific parameters.
2. Choice of process variables to be transmitted via the CHANNEL parameter in the
Analog Input or Totalizer function block.
3. Setting of the units for the process variables.
9.3
Cyclic data transmission
Cyclic data transmission when using the device master file (GSD).
9.3.1
Block model
The block model shows which input and output data the measuring device makes available
for cyclic data exchange. Cyclic data exchange takes place with a PROFIBUS master (Class
1), e.g. a control system.
Measuring device
Control system
Transducer
Block
Analog Input block 1 to 4 → 63
Output value AI
→
PROFIBUS PA
Totalizer block 1 to 3
Output value TOTAL
→
Controller SETTOT
←
Summary of Contents for Proline Prowirl F 200
Page 224: ...www addresses endress com...