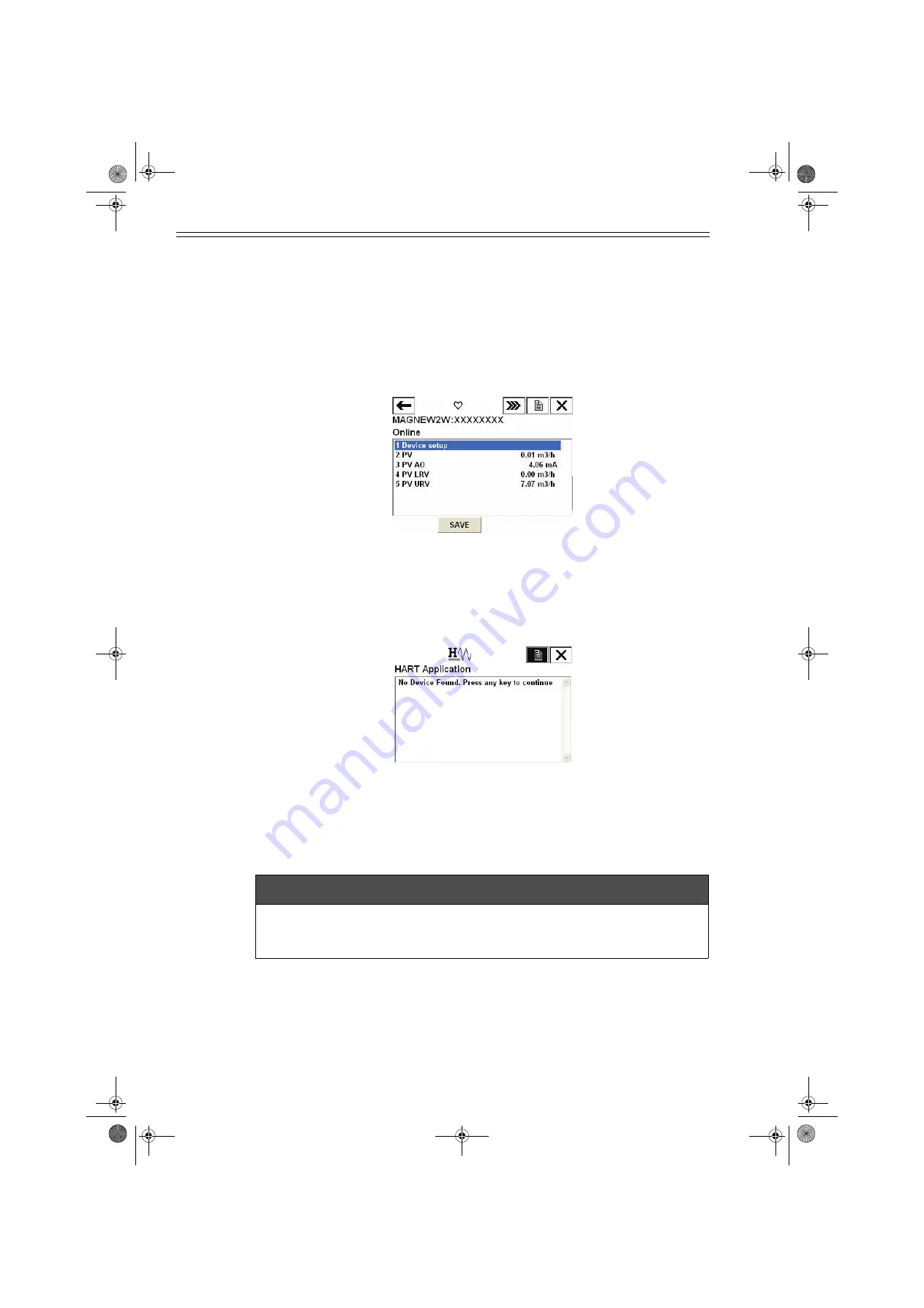
Operation using HART communicator
Azbil Corporation
7-4
Model MTG11A/18A, MTG11B/18B, MTG14C
7-1-3 : Verifying communication
After the HART Communicator has been properly interconnected, turn the device's
power on. For the external power supply model, turn on the external power supply
before turning the device power on.
Once the setting and wiring connections are correct, the HART Communicator's
display shows an online menu as shown below and a HART mark will flicker in the
upper right hand corner of the display.
Figure 7-2 Online menu
If the display is not as shown in Figure 7-2 but as shown in Figure 7-3 below, no
communications are being made. Recheck the HART Communicator connections and
the setting of converter. (The setting of the converter is described page 7-2.)
Figure 7-3 Communication not available
7-1-4 : Cautions
m
CAUTION
Do not remove the HART Communicator cable from the converter while executing
communication. If the cable is disconnected during data setting transmission there
will be no data transfer to the converter.
CM2-MTG300-2001.book 4 ページ 2015年9月29日 火曜日 午前10時14分
Summary of Contents for MagneW Neo PLUS
Page 16: ...List of Figures Tables CM2 MTG300 2001 book 4...
Page 92: ...MEMO CM2 MTG300 2001 book 38...
Page 106: ...MEMO CM2 MTG300 2001 book 4...
Page 266: ...MEMO CM2 MTG300 2001 book 82...
Page 312: ...MEMO CM2 MTG300 2001 book 46...
Page 336: ...MEMO CM2 MTG300 2001 book 22...
Page 338: ...CM2 MTG300 2001 book 2...