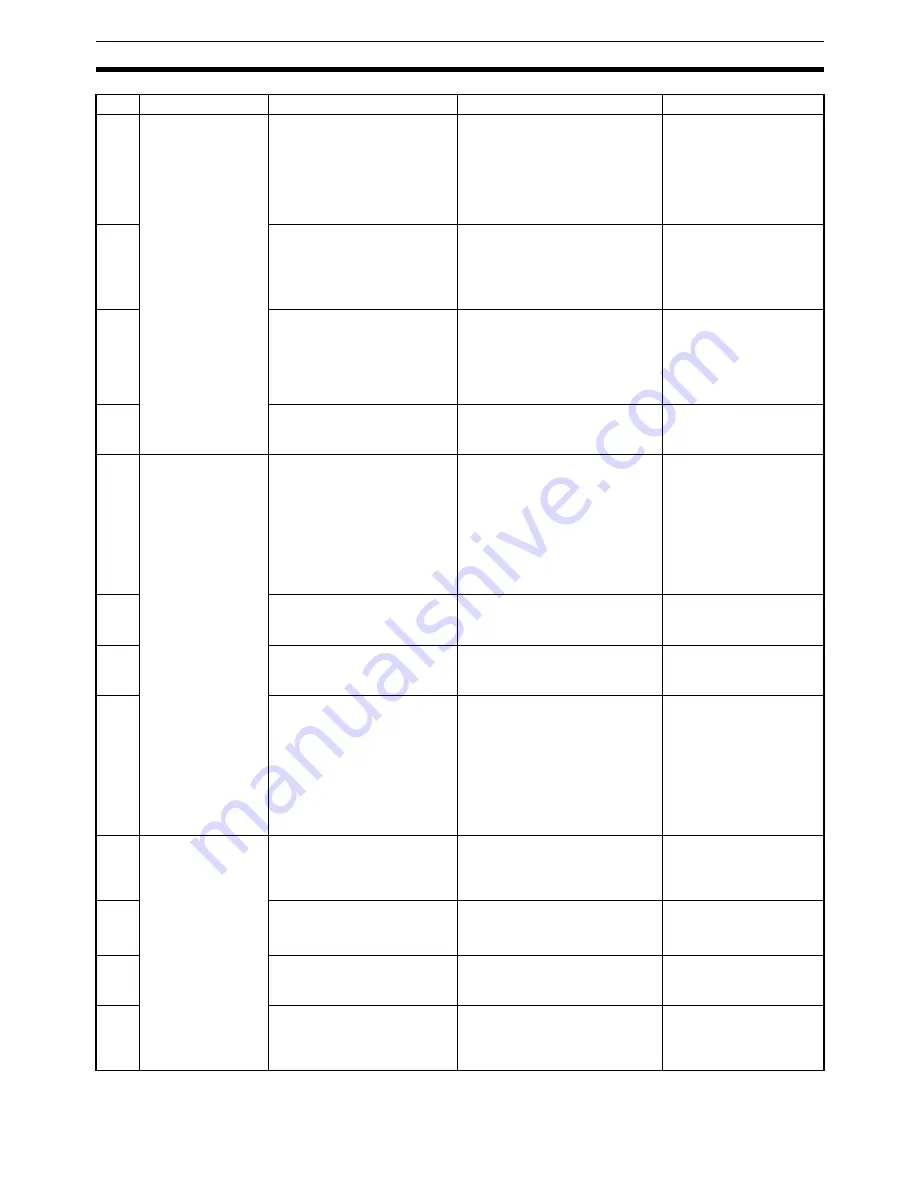
527
Troubleshooting Tables
Section 12-1
41
Rotation is
reversed.
The Servo Driver is set for
reverse rotation.
If the LED indicator on the front
panel matches the jogging
direction during jogging
operations, and if the direction of
rotation is reversed, check
whether the Servo Driver is set
for reverse rotation.
Correct the setting for the
direction of Servo Driver
rotation.
42
The feedback signal (phase A/
B) is reversed and the param-
eter is set for reverse rotation.
Check whether the feedback
signal (phase A/B) is reversed
and whether the parameter is set
for reverse rotation.
Correct the feedback
signal (phase A/B) wiring.
Correct the reverse
rotation setting at the MC
Unit parameters.
43
During an origin search the
origin proximity sensor
polarity does not match the
parameter setting (in the MC
Unit) for the origin proximity
input polarity.
Check the parameter setting and
the sensor polarity.
Correct the parameter
setting.
44
During an origin search, the
origin proximity input wiring is
faulty.
With the Teaching Box, check
whether the origin proximity input
status is correct.
Correct the origin
proximity input wiring.
45
The positioning
completed signal is
not output or is
delayed. (The next
operation cannot be
started.)
The in-position width set in
the MC Unit parameters is too
narrow, and the axis is not in
the in-position range. (If it is
not in the in-position range,
the next operation cannot be
started because the
preceding operation is not
completed.)
---
Increase the in-position
width set in the MC Unit
parameters.
46
The Servo Driver gain is too
low.
---
Adjust the Servo Driver
gain and increase the MC
Unit position loop gain.
47
The servo speed reference is
incorrect.
---
Adjust the servo speed
reference offset (zero
balance).
48
The axis is not in the
in-position range due to
external pressure applied
when positioning stopped.
With the CX-Motion or the
Teaching Box, monitor the error
counter and check whether the
axis is in the in-position range.
If positioning is stopped
outside of the in-position
range due to external
pressure, the G-language
program must be
changed so that
in-position monitoring
(Pass Mode operation)
will not be performed.
49
There are unusual
noises.
The machinery is vibrating.
Check for foreign objects in the
machinery’s moving parts, and
inspect for damage, deformation,
and looseness.
Make any necessary
repairs.
50
The speed loop gain is
insufficient. (The gain is too
high.)
---
Perform autotuning.
Manually adjust
(decrease) the gain.
51
The wrong Servomotor is
selected (so it cannot be
adjusted).
Check the torque and inertia
ratings and select another
Servomotor.
Change to a suitable
Servomotor.
52
There is eccentricity in the
couplings connecting the
Servomotor axis and the
mechanical system.
---
Adjust the mounting of
the Servomotor and
machinery.
No.
Problem
Probable causes
Items to check
Remedy
Содержание CS1W-MC221 -
Страница 1: ...Motion Control Units Cat No W359 E1 04 CS1W MC221 V1 421 V1 OPERATION MANUAL ...
Страница 2: ...CS1W MC221 V1 421 V1 Motion Control Units Operation Manual Revised February 2008 ...
Страница 3: ...iv ...
Страница 5: ...vi ...
Страница 11: ...xii ...
Страница 15: ...xvi ...
Страница 19: ...xx ...
Страница 27: ...xxviii Conformance to EC Directives 6 ...
Страница 133: ...106 Installation Section 2 2 2 2 4 Dimensions CS1W MC421 CS1W MC221 ...
Страница 173: ...146 Connecting Peripheral Devices Section 2 7 ...
Страница 227: ...200 Command Area Section 3 6 ...
Страница 351: ...324 Interface Specifics Section 5 4 ...
Страница 513: ...486 Absolute Encoder Interface Specifications Section 9 7 ...
Страница 575: ...548 Error Log Section 12 6 ...
Страница 589: ...562 Performance Appendix A ...
Страница 655: ...628 Control Bit Flag Timing Charts Appendix E ...
Страница 683: ...656 Origin Search Patterns Appendix F ...
Страница 685: ...658 Encoder Divider Rate and Rotation Speed for OMRON Servo Drivers Appendix G ...