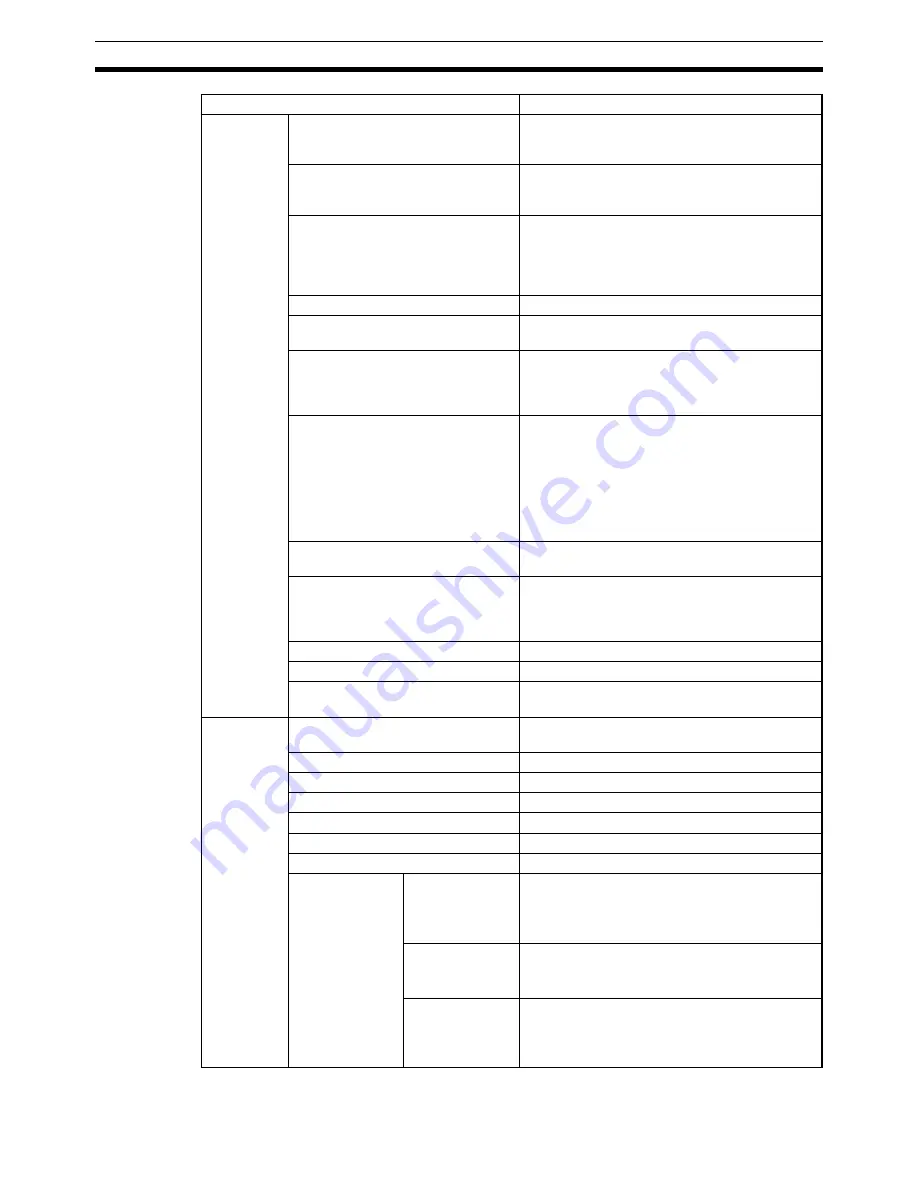
22
Specifications
Section 1-5
Automatic
Positioning with linear interpolation
Executes linear interpolation at the specified
interpolation feed rate for up to either two or four
axes simultaneously.
Positioning with circular interpolation
Executes clockwise or counterclockwise 2-axis
circular interpolation at the specified interpolation
feed rate.
Positioning with helical circular
interpolation
Executes clockwise or counterclockwise 2-axis
circular interpolation and 1-axis linear
interpolation (i.e., helical interpolation) at the
specified interpolation feed rate. (Available for
CS1W-MC421 only.)
Traverse function
Executes winding (traverse operation).
Speed control
Moves a maximum of either two or four axes at a
controlled speed.
Interrupt feeding
Moves a specified axis for a fixed amount when a
general input is turned ON. With interrupt feeding,
positioning without an interrupt signal can be
executed.
Switching to Pass Mode
Changes to Pass Mode, in which operations are
executed one by one with no deceleration stop. In
Pass Mode, the interpolation acceleration or
deceleration time of the previous operation can
be specified for the next operation (Pass Mode
time selection). A pass operation for only one axis
can be executed at a fixed acceleration (with a
fixed acceleration mode setting).
Switching to In-position Check OFF
Mode
Starts the next positioning operation without
waiting for the current one to be completed.
Stop-over function
Outputs an M code or a D code while axes are
being moved by a fixed amount (determined by
present position), without stopping the operation.
G codes are also possible for all operations.
Dwell timer
Pauses positioning for a specified time.
Workpiece origin return
Automatically returns to workpiece origin.
Automatic origin return
Automatically returns to reference coordinate
system origin.
Automatic
Cycle start
Executes a specified program from the first block,
or resumes execution of a stopped program.
Single block
Executes the program one block at a time.
Pause
Temporarily halts program execution.
Forced block end
Forcibly ends execution of a block.
Error reset
Clears error status.
M code reset
Resets the M code (for interlock).
Teaching
Creates position data for each task.
Auxiliary
Optional inputs
20 points: Specify input information to be
referenced by special G code.
Of the 20 input points, 4 can be specified as
general-purpose inputs for the MC Unit.
M code
0 to 999
0 to 499: M code for taking interlock
500 to 999: M code not taking interlock
D code (interrupt
code)
0 to 255
Starts a CPU Unit external interrupt task when
positioning is completed or when passing through
a particular position.
Item
Contents
Содержание CS1W-MC221 -
Страница 1: ...Motion Control Units Cat No W359 E1 04 CS1W MC221 V1 421 V1 OPERATION MANUAL ...
Страница 2: ...CS1W MC221 V1 421 V1 Motion Control Units Operation Manual Revised February 2008 ...
Страница 3: ...iv ...
Страница 5: ...vi ...
Страница 11: ...xii ...
Страница 15: ...xvi ...
Страница 19: ...xx ...
Страница 27: ...xxviii Conformance to EC Directives 6 ...
Страница 133: ...106 Installation Section 2 2 2 2 4 Dimensions CS1W MC421 CS1W MC221 ...
Страница 173: ...146 Connecting Peripheral Devices Section 2 7 ...
Страница 227: ...200 Command Area Section 3 6 ...
Страница 351: ...324 Interface Specifics Section 5 4 ...
Страница 513: ...486 Absolute Encoder Interface Specifications Section 9 7 ...
Страница 575: ...548 Error Log Section 12 6 ...
Страница 589: ...562 Performance Appendix A ...
Страница 655: ...628 Control Bit Flag Timing Charts Appendix E ...
Страница 683: ...656 Origin Search Patterns Appendix F ...
Страница 685: ...658 Encoder Divider Rate and Rotation Speed for OMRON Servo Drivers Appendix G ...