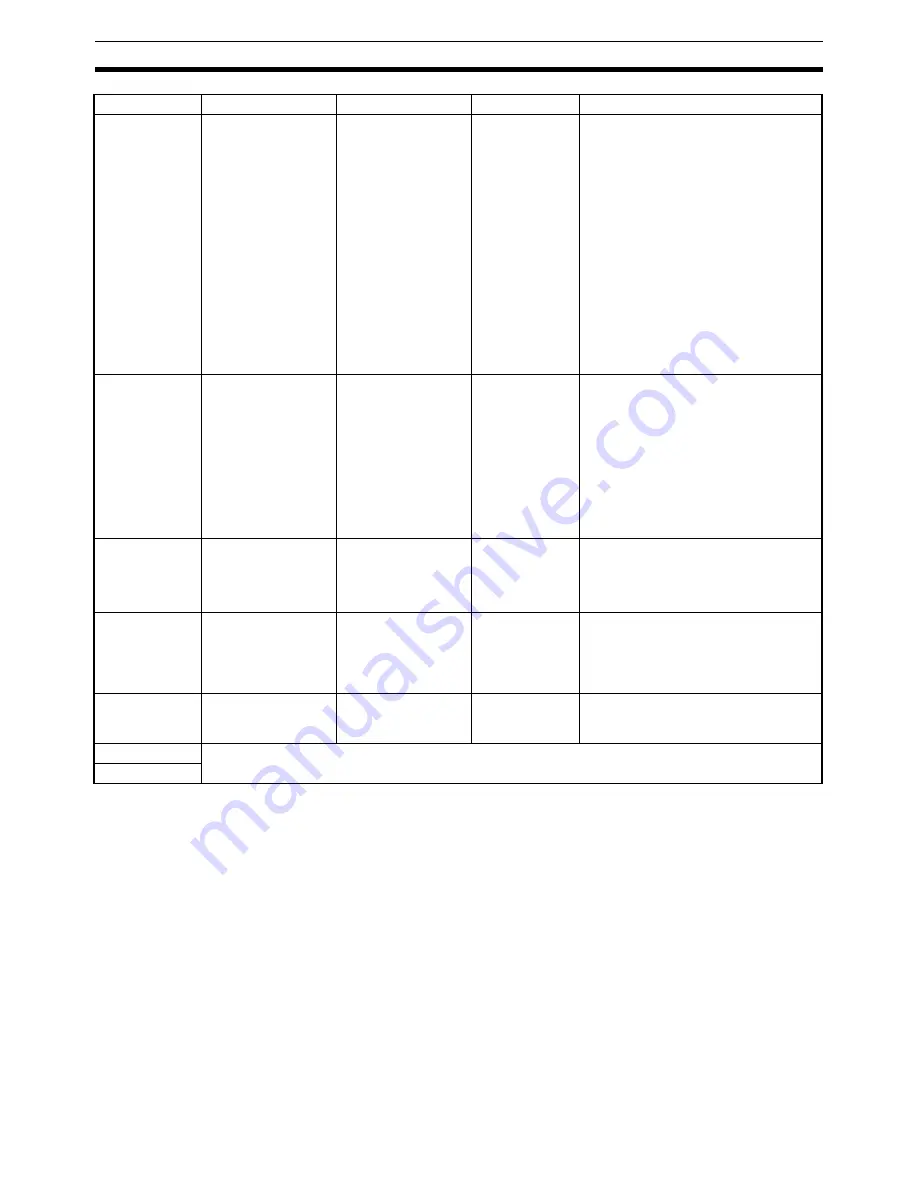
68
Overview of Version 1 Upgrades
Section 1-12
Note
(1) For version-1 MC Units, units are determined according to the parame-
ters. MPG can be pulses only.
(2) Up to 720 points can be set per axis. Their use, however, is limited by the
position data capacity.
• Values in this operand table are not reflected in real time (i.e., they are
reflected only when first executed).
• Hold the values in this operand table according to the following timing.
a.
In Stop Mode: Until electronic cam operation begins. (If a start condi-
tion is set, wait for the start condition.)
b.
In Pass Mode or In-position Check Off Mode: Until the electronic cam
function advances to the next block.
• An error (number out of range) will occur if a value outside of the range
shown in the above table is set, or if a value that cannot be specified is
set.
Note
An error will occur if a non-integer is specified for integer-only data.
+6
Start/end conditions
Latch
Input position
Repeat
1st digit: Start condi-
tion
0: None
1: Input axis position
2: General-purpose
input leading edge
3: Phase-Z leading
edge
2nd digit: End condi-
tion
0: 1 rotation only
1: Repeat
Note
Integers only
---
Start condition: Specifies the electronic
cam operation's start condition (trig-
ger). If MPG is used for the input axis,
the input axis position cannot be speci-
fied for the start condition.
If the phase Z input is specified, the
input for the axis to latch will be moni-
tored.
If a general-purpose input is specified,
the input for the axis number corre-
sponding to the axis to latch (X to U
correspond to 1 to 4, respectively) will
be monitored.
End condition: Specifies whether elec-
tronic cam operations are to end after
one rotation or be repeated with no
limit.
+7
Input axis position
±
39,999,999
Pulses
mm
deg
inch
(See note.)
Specifies the input axis position for
starting cam operation when the input
axis position is the start/end condition.
Electronic cam operation starts when
the position set here is crossed.
Note
If 0 is set, the electronic cam
function does not operate even if
the input axis starts from 0. In
that case, set the start/end con-
ditions to None (0).
+8
Cam table size
2 to 720
Note
Integers only
Per axis (See
note 2.)
Points
The cam table size is specified in
points. A set consisting of a cam angle
and stroke ratio is counted as one
point.
+9
Cam table data n
(cam angle)
0.0000 to 360.0000
Deg
Specifies the input axis position, in
increasing order, from 0
°
to 360
°
.
(Identical values are not possible.)The
beginning of the table must be 0
°
, and
the end of the table must be 360
°
.
+10
Cam table data n
(stroke ratio)
0.0000 to
±
3999.9999
Factor
Specifies the cam axis position as a
percentage of the input axis position.
The normal range is from 0 to
±
1.
+11
From here on, the descriptions are the same as for +9 and +10 according to the cam table size, alter-
nating between cam angle and stroke ratio.
+12 and higher
Data name
Data range
Unit
Description
Содержание CS1W-MC221 -
Страница 1: ...Motion Control Units Cat No W359 E1 04 CS1W MC221 V1 421 V1 OPERATION MANUAL ...
Страница 2: ...CS1W MC221 V1 421 V1 Motion Control Units Operation Manual Revised February 2008 ...
Страница 3: ...iv ...
Страница 5: ...vi ...
Страница 11: ...xii ...
Страница 15: ...xvi ...
Страница 19: ...xx ...
Страница 27: ...xxviii Conformance to EC Directives 6 ...
Страница 133: ...106 Installation Section 2 2 2 2 4 Dimensions CS1W MC421 CS1W MC221 ...
Страница 173: ...146 Connecting Peripheral Devices Section 2 7 ...
Страница 227: ...200 Command Area Section 3 6 ...
Страница 351: ...324 Interface Specifics Section 5 4 ...
Страница 513: ...486 Absolute Encoder Interface Specifications Section 9 7 ...
Страница 575: ...548 Error Log Section 12 6 ...
Страница 589: ...562 Performance Appendix A ...
Страница 655: ...628 Control Bit Flag Timing Charts Appendix E ...
Страница 683: ...656 Origin Search Patterns Appendix F ...
Страница 685: ...658 Encoder Divider Rate and Rotation Speed for OMRON Servo Drivers Appendix G ...